The World of Centerless Grinders An Overview
Centerless grinding is a manufacturing process that has gained significant importance in the precision machining industry. At the heart of this process lies the centerless grinder, a specialized machine designed for grinding cylindrical parts without the need for a center hole to be drilled in the workpiece. This innovative technology allows for increased efficiency and accuracy, making it a preferred choice for many manufacturers.
Understanding Centerless Grinding
Centerless grinding is distinct from traditional grinding methods where the workpiece is held between two centers. Instead, in centerless grinding, the workpiece is supported by an external feeder and held in place by a combination of a grinding wheel, a regulating wheel, and a work-rest blade. This setup allows for continuous feeding of parts, increasing productivity and minimizing the handling time.
The primary components of a centerless grinder include the grinding wheel, which does the actual cutting, the regulating wheel, which controls the rotation and movement of the workpiece, and the work-rest blade that supports the part. The alignment and angling of these components are crucial for achieving the desired precision and finish on the workpiece.
Advantages of Centerless Grinding
One of the main advantages of centerless grinding is its ability to perform high-speed operations. Because the process does not require centers, it can easily accommodate long, slender workpieces. This area of expertise makes centerless grinders ideal for producing components such as shafts, pins, and tubes, which are widely used in automotive, aerospace, and consumer goods manufacturing.
Another significant benefit is the reduction in labor costs and time. Since the machine operates with minimal manual intervention, manufacturers can allocate resources more efficiently. Furthermore, the continuous production flow ensures a reducing cycle time, promoting cost-effective manufacturing processes.
Centerless grinding also offers enhanced dimensional accuracy and a superior surface finish. The precise control over the grinding process allows manufacturers to meet tight tolerances and achieve finishes that are often required for critical applications. This capability positions centerless grinders as an essential tool in industries that prioritize precision and quality.
Types of Centerless Grinders
3 centerless grinder
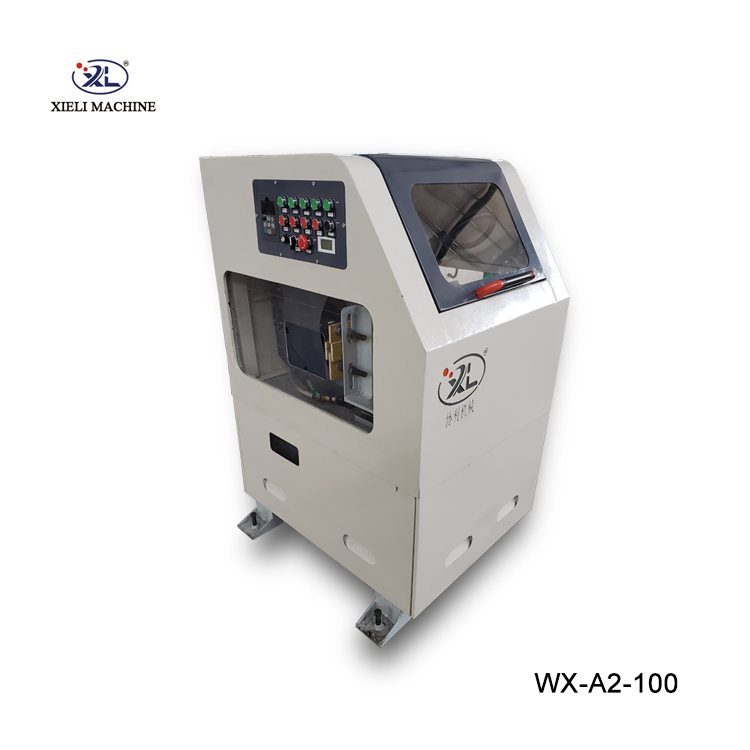
There are several types of centerless grinders, each designed for specific applications. The most common types include
1. Through Feed Grinders These are used for workpieces that can be fed straight through the machine. It is particularly useful for producing long parts and offers the highest level of production efficiency.
2. In-Feed Grinders This type is suitable for grinding workpieces that are not of uniform length. The operator manually places the part into the grinding zone, allowing for greater flexibility in handling various shapes and sizes.
3. End-Feed Grinders These machines are designed to handle workpieces that require grinding only on the ends. This makes them ideal for certain specialized applications where only specific sections of the part need processing.
Applications of Centerless Grinding
The versatility of centerless grinders means that they are employed across many industries. In the automotive sector, for example, they are used to manufacture engine components, transmission shafts, and steering columns. In the aerospace industry, they create critical components such as landing gear parts and fuel injectors with impeccable tolerances and finishes.
Additionally, medical device manufacturing relies heavily on centerless grinding to produce precision components for surgical tools and implantable devices. The high standards of quality and precision that these industries demand make centerless grinders an indispensable part of the production process.
Conclusion
In conclusion, centerless grinders represent an essential technology in modern manufacturing. Their ability to provide high precision, efficiency, and cost-effectiveness makes them a valuable asset for various industries. As technology continues to advance, the role of centerless grinding is likely to expand, offering new possibilities for enhancing production processes and meeting the evolving needs of manufacturing. Companies investing in centerless grinding technology can expect significant returns in productivity and product quality, thereby securing their competitive edge in the marketplace.