Centerless grinders have long been an integral tool in the field of metalworking, enabling manufacturers to achieve precise and efficient material removal. In recent years, however, an unexpected phenomenon known as tiger stripe has sparked curiosity and concern among machinists and engineers alike. This article delves into the intricacies of centerless grinders, explores the genesis of tiger stripe patterns, and offers insights into mitigating this issue to boost operational efficiency and product quality.

Centerless grinding stands out due to its unique operation without spindles or fixtures, utilizing two rotary wheels to secure and process workpieces from the outside. This design offers unmatched speed and precision, ideal for high-volume production lines and diverse applications, from automobile components to aerospace parts. Nevertheless, the occurrence of tiger stripes—distinct, contrasting line patterns on the surface of ground workpieces—can pose substantial quality control challenges.
Tiger stripes can emerge due to various factors, frequently linked to mechanical dynamics within the grinding process. One primary cause is the vibration, which could result from imbalanced grinding wheels, improper alignment, or external environmental influences. Vibrations can alter the interaction between the workpiece and wheels, leading to inconsistent material removal and the characteristic striped appearance. Additionally, wheel wear and coolant delivery inconsistencies can exacerbate the phenomenon.
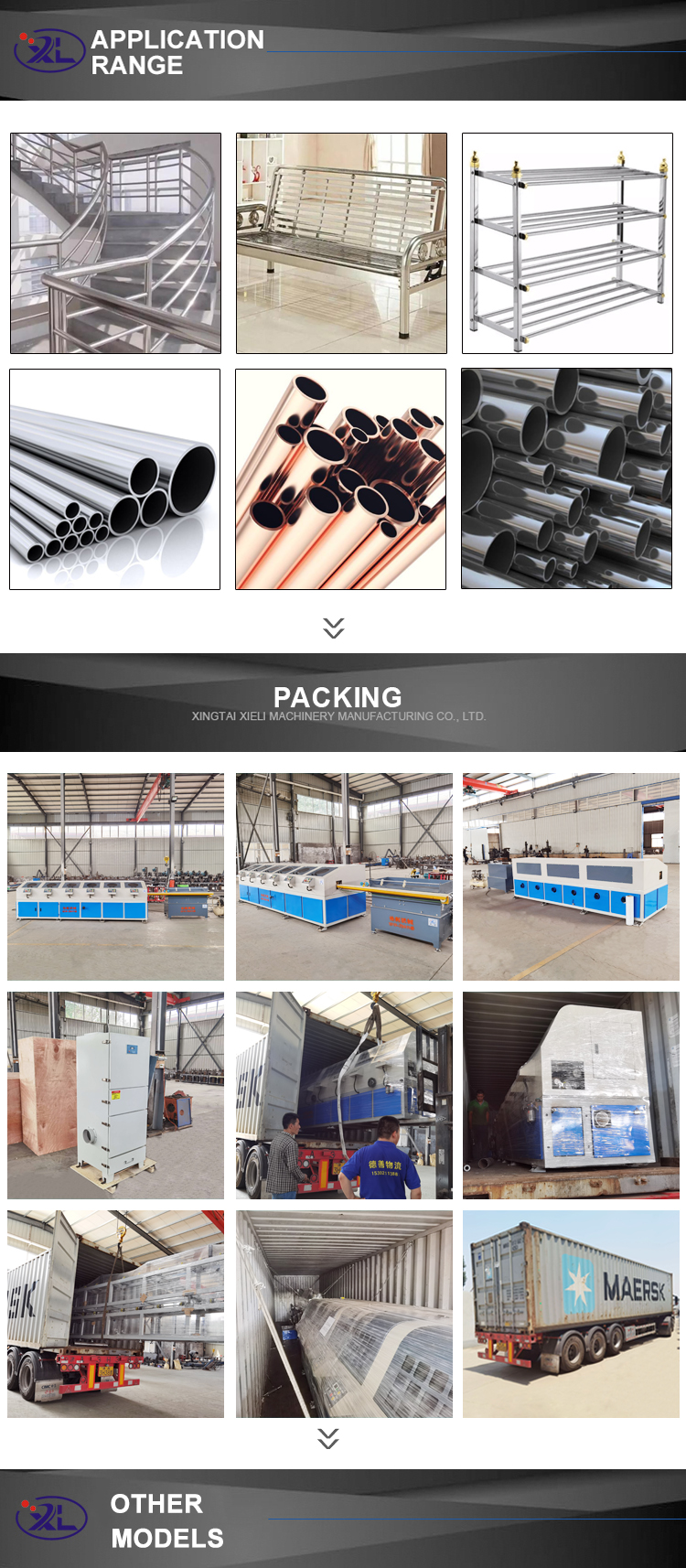
It's crucial to address this issue head-on to maintain the integrity of the workpiece and ensure the longevity of the centerless grinder itself. First and foremost, predictive maintenance plays a pivotal role. Regularly inspecting and servicing grinding wheels to address wear and imbalance can significantly reduce vibrational influences. Moreover, implementing advanced technology such as sensors and IoT devices can facilitate real-time monitoring of machine performance, allowing for proactive adjustments and maintenance scheduling.
Balancing is another critical factor. Properly calibrating the wheels not only curtails vibration but also ensures even pressure distribution on the workpiece, minimizing the risk of uneven grinding patterns. Modern centerless grinders often come equipped with automated balancing systems, providing a reliable solution to what was once a painstaking manual process.
Coolant application also demands attention. Uneven cooling can lead to thermal expansion, distorting workpiece dimensions and inducing surface irregularities like tiger stripes. Engineers can optimize coolant delivery systems by employing nozzle designs that ensure consistent distribution across the grinding interface. Additionally, exploring alternative coolant compositions that enhance heat dissipation may further refine surface finishes.
centerless grinder tiger stripe
Furthermore, leveraging cutting-edge computational simulations offers insight into potential stripe formation. By modeling the centerless grinding process and simulating dynamic conditions under various operational parameters, manufacturers can pinpoint vulnerabilities that may contribute to striping and refine their setups accordingly.
Training is pivotal to enhancing operator expertise. By equipping machinists with knowledge about the factors leading to tiger stripe formation and encouraging a culture of continuous improvement, organizations can harness their human capital to mitigate the risk of defective workpieces. Training initiatives could involve workshops, hands-on demonstrations, and collaborations with experienced technicians who understand the nuances of centerless grinding.
From an authoritative perspective, establishing industry-wide standards could help address the tiger stripe issue more comprehensively. By working with associations and stakeholders to develop guidelines that highlight best practices for setup, maintenance, and process optimization, manufacturers can collectively elevate product quality and operational efficiency across the sector.
Ultimately,
garnering trust is critical. As customers increasingly demand impeccable surface finishes and high-performance components, effectively tackling the tiger stripe issue fortifies a manufacturer’s reputation. By demonstrating a commitment to continuous improvement and excellence in centerless grinding practices, companies not only address immediate production challenges but also build long-lasting relationships based on quality assurance and reliability.
In conclusion, while the appearance of tiger stripes in centerless grinding may seem daunting, a combination of preventive maintenance, technological innovation, and expert training can significantly alleviate this issue. By understanding the root causes and taking decisive actions to enhance machinery and process standards, manufacturers can ensure that their centerless grinders continue to deliver superior results in today’s competitive landscape.
For More Details Pls Contact Us
Fiberglass Reinforced Plastic (FRP), also known as fiber-reinforced plastic, is a composite material widely used across various industries.