The Significance of Tube Internal Polishing Machines in Modern Manufacturing
In the realm of modern manufacturing, precision and quality are paramount. One critical factor influencing the quality of various products, especially in industries such as aerospace, automotive, and medical, is the smoothness of the internal surfaces of tubes. This is where tube internal polishing machines come into play, revolutionizing the way manufacturers ensure the integrity and performance of their products.
Understanding Tube Internal Polishing
Tube internal polishing is a process that enhances the surface finish of the inner walls of tubes. This procedure is crucial for a multitude of applications. A smooth internal surface reduces friction, improves flow characteristics, and minimizes the risk of corrosion. Moreover, it can optimize the performance of fluid systems and helps in preventing contamination, which is particularly vital in industries like pharmaceuticals and food processing.
Internal polishing machines utilize various techniques, including mechanical polishing, chemical polishing, and electropolishing. Each method has its advantages, depending on the material of the tube and the required finish. Mechanical polishing involves the use of abrasives and polishing tools to achieve the desired surface finish. Chemical polishing, on the other hand, uses chemical agents to remove surface imperfections, while electropolishing employs an electrochemical process to achieve a mirror-like surface.
Types of Tube Internal Polishing Machines
There are several types of tube internal polishing machines designed to cater to different needs and specifications
1. Rotary Tube Polishing Machines These machines use a rotating action along with polishing tools to achieve a smooth finish. They are versatile and can handle various tube sizes and materials.
2. Cylindrical Polishing Machines Suitable for long tubes, these machines can polish the internal surface without the need for multiple setups, thus increasing efficiency.
3. High-Pressure Abrasive Polishing Machines These machines employ high-pressure abrasive media to effectively clean and polish the internal surfaces. They are ideal for tougher materials and thicker walls.
tube internal polishing machine
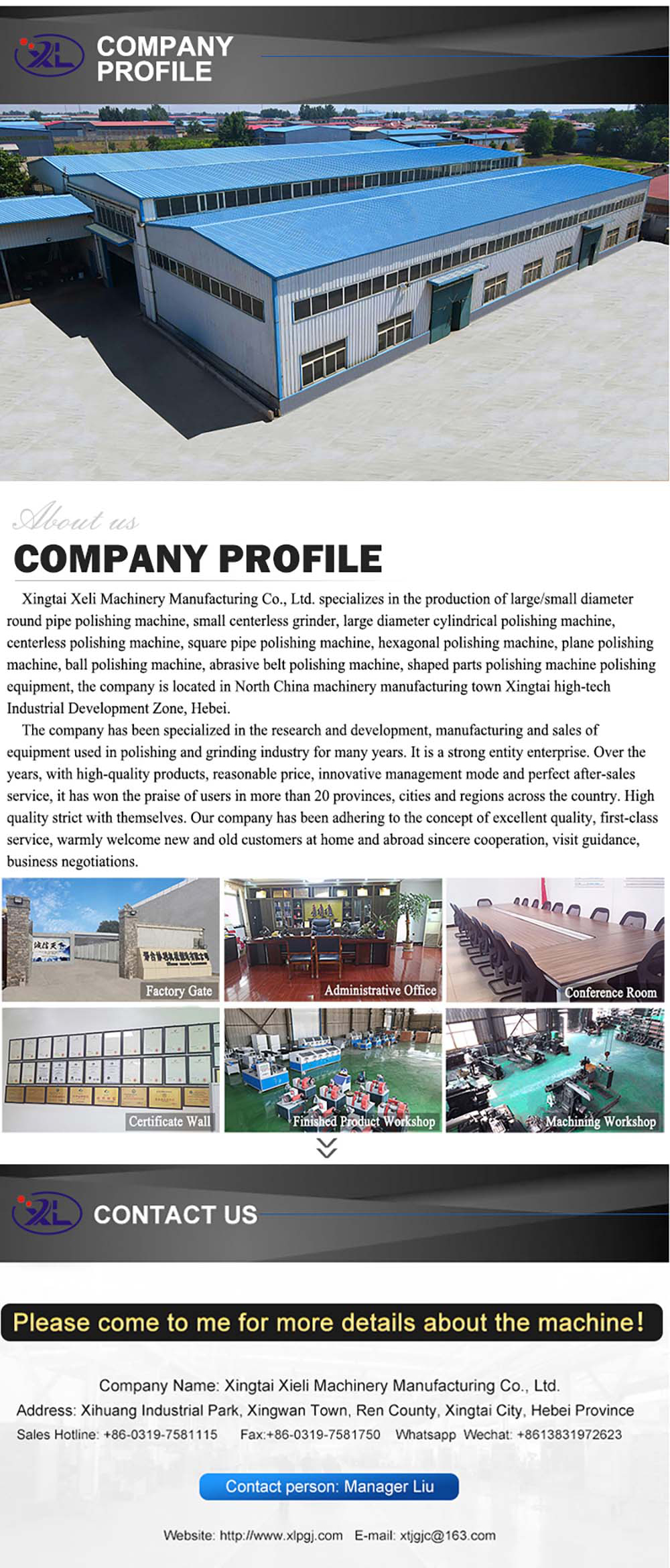
The Benefits of Using Tube Internal Polishing Machines
The implementation of these machines brings numerous benefits to manufacturers
- Improved Product Quality A smooth internal surface leads to better flow characteristics in fluid systems, enhancing overall product performance and reliability.
- Increased Longevity Polished tubes are less susceptible to wear and corrosion, resulting in longer-lasting products, which reduces replacement costs and resource consumption.
- Enhanced Safety In critical applications such as oil and gas, or medical tubing, the risk of contamination due to rough surfaces is minimized, ensuring safer end products.
- Cost-Effectiveness By investing in tube internal polishing machines, manufacturers can automate processes that would otherwise be labor-intensive, leading to lower operational costs over time.
- Flexibility Many modern polishing machines are designed with adjustable settings, enabling manufacturers to customize the polishing process based on specific material requirements or production demands.
Applications Across Industries
Tube internal polishing machines find applications in a wide array of industries. In the aerospace sector, they are used to enhance fuel lines and hydraulic systems, where performance and safety are critical. In automotive manufacturing, these machines help in producing components like brake lines, ensuring smooth fluid transfer. The medical industry requires polished tubes for devices like catheters and syringes, where sterility and precision are non-negotiable.
Conclusion
In summary, tube internal polishing machines play a vital role in modern manufacturing, contributing to higher quality standards and improved product performance. As industries continue to advance and demand more precision, the importance of these machines is only set to grow. Investing in advanced tube internal polishing technology not only boosts operational efficiency but also enhances the safety and reliability of the products delivered to end-users. Embracing these innovations is essential for manufacturers who wish to remain competitive in today’s fast-paced market.