Ovality in Centerless Grinder Companies
In the realm of precision machining, centerless grinding stands out as a crucial process for producing cylindrical components with tight tolerances. This method is favored for its efficiency and ability to maintain consistent part dimensions. However, one persistent challenge faced by companies specializing in centerless grinding is ovality - the deviation from a perfectly circular cross-section of the finished part. Understanding the causes of ovality, its implications on product quality, and the strategies for its mitigation is essential for companies striving to optimize their grinding processes.
Ovality in Centerless Grinder Companies
For centerless grinder companies, ovality not only impacts product quality but also has financial implications. Parts with ovality often require rework or even scrapping, leading to increased operational costs and delays in delivery schedules. Moreover, customer satisfaction could be compromised as the reliability of the final product comes into question. It is vital for companies to implement stringent quality control measures to monitor and reduce ovality to meet industry standards.
ovality in centerless grinder companies
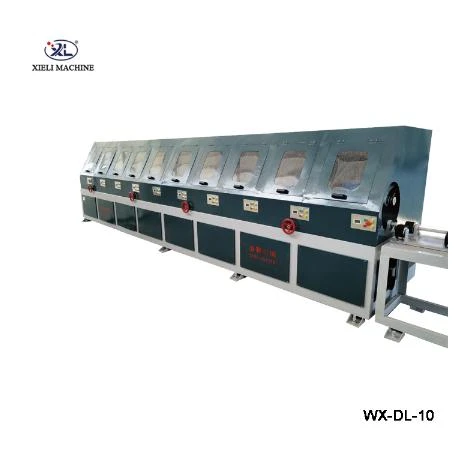
One approach to minimizing ovality is through regular maintenance and calibration of grinding machines. Ensuring that all components of the grinder, including the regulating wheel, grinding wheel, and work rest, are aligned and functioning correctly is crucial. Misalignment can lead to uneven grinding and result in ovality. Therefore, routine checks and adjustments can dramatically reduce the occurrence of this defect.
Additionally, the choice of materials plays a significant role in ovality. Companies must be attentive to the properties of the workpieces being processed. Variations in hardness and structural consistency can influence how materials respond to grinding. A thorough pre-grinding inspection of materials can help identify any potential issues before processing begins. Moreover, utilizing advanced materials that are more uniform can further mitigate the risks associated with ovality.
Another effective strategy is investing in advanced technology for monitoring and controlling the grinding process. The integration of sophisticated sensors and automated systems can provide real-time data on the grinding operation. By closely analyzing this data, operators can identify patterns that contribute to ovality and make necessary adjustments. Implementing CNC (computer numerical control) centerless grinders can also enhance precision and reduce human error, leading to improved dimensional consistency.
In conclusion, ovality in centerless grinding is a significant concern for machining companies. Understanding its causes and implications is essential for maintaining product quality and operational efficiency. Through regular machine maintenance, careful material selection, and the adoption of advanced technologies, companies can effectively reduce the incidence of ovality. By prioritizing these strategies, centerless grinder companies can enhance their competitive edge in the market, ensuring they meet the demanding standards of the industry while achieving customer satisfaction. As the manufacturing sector continues to evolve, addressing challenges like ovality will remain a critical focus for ensuring precision in machining processes.