High-Quality Centerless Grinder Automation
In the realm of precision manufacturing, the centerless grinder has emerged as a pivotal tool, revered for its efficiency and capability to produce components with exceptional accuracy
. With the constant push towards automation, integrating high-quality centerless grinder automation systems has revolutionized the way industries approach mass production and quality assurance.Centerless grinding is a machining process that uses abrasive cutting to remove material from a workpiece. Unlike traditional grinders, centerless grinders do not require the workpiece to be mounted between centers. Instead, it is supported by a work rest blade and driven by a regulating wheel, providing immense versatility and speed. However, the introduction of automation has propelled this process into a new era, enhancing production capabilities while maintaining high quality.
One of the primary advantages of automating centerless grinding is the significant increase in throughput. Automated systems can manage multiple operations simultaneously, including feeding, grinding, and unloading components. This reduces human intervention, thus minimizing labor costs and potential errors. High-speed robotics can accurately position and transfer workpieces with precision, ensuring consistent flow through the grinding process. Consequently, companies can meet growing production demands while adhering to stringent timelines.
high quality centerless grinder automation
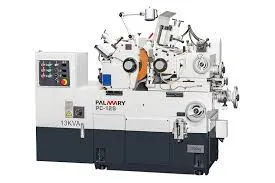
Moreover, the integration of advanced sensors and controls in automated centerless grinders ensures real-time monitoring of the grinding process. These smart systems track various parameters such as grind pressure, wheel wear, and temperature fluctuations. By leveraging this data, manufacturers can make timely adjustments to maintain optimal performance and prevent downtime. This predictive maintenance approach is crucial for sustaining high precision and extending the lifespan of machine tools.
Quality control is another area where automation shines. High-quality centerless grinder automation systems are equipped with inspection technologies that verify the dimensions and surface finish of the machined parts in real-time. Advanced vision systems utilize cameras and algorithms to detect deviations from specifications, allowing immediate corrective actions. This capability not only enhances product quality but also reduces waste and rework rates, contributing to overall efficiency.
Furthermore, modern automated centerless grinding solutions come with user-friendly interfaces that allow operators to set up and modify grinding parameters quickly. This adaptability is essential in today’s fast-paced manufacturing environments, where production runs may vary frequently. Operators can easily switch between different workpieces without extensive downtime, thus maximizing machine utilization.
In conclusion, the advent of high-quality centerless grinder automation has significantly transformed the manufacturing landscape. By enhancing throughput, ensuring consistent quality, and providing real-time feedback, automated grinding solutions empower manufacturers to remain competitive in an increasingly challenging market. As technology continues to advance, we can expect even greater integration of automation in centerless grinding processes, leading to improved efficiency, lower costs, and superior product quality. This evolution not only underscores the importance of precision engineering but also highlights the critical role of automation in shaping the future of manufacturing.