Custom Filmatic for Centerless Grinder Machine
In the rapidly evolving landscape of manufacturing, precision and efficiency are paramount. One area that has seen significant advancements is the centerless grinding process, which is crucial for producing high-quality cylindrical parts. The introduction of custom filmatic solutions tailored for centerless grinding machines has revolutionized the way manufacturers approach this process. These tailored solutions not only enhance grinding efficiency but also ensure consistency and precision in the final output.
Centerless grinding is a method where the workpiece is held in place by a combination of rotating wheels without the need for a fixture. This technique allows for high production rates and is ideal for parts that require precise dimensions and finishes. However, achieving optimal performance in centerless grinding demands meticulous attention to detail, especially regarding the coolant applied during the process. This is where custom filmatic solutions come into play.
A custom filmatic for centerless grinders is essentially a specialized coolant delivery system designed to meet the unique needs of specific grinding applications. Unlike standard coolant systems, a custom-designed filmatic provides targeted flow and pressure, ensuring that the coolant fully penetrates the grinding area. This targeted application leads to enhanced cooling, reduced wear on grinding wheels, and improved chip removal. Consequently, it minimizes the risk of thermal damage to the workpiece while facilitating a smoother grinding operation.
custom filmatic for centerless grinder machine
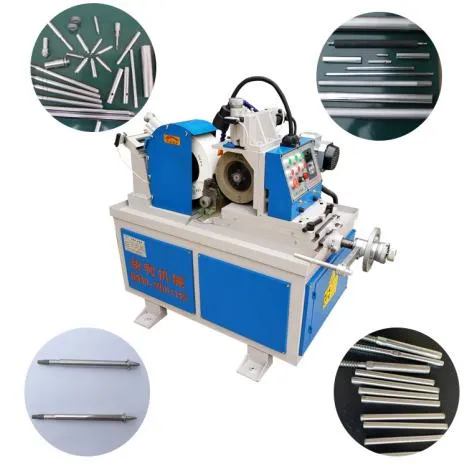
Moreover, the formulation of the coolant in a custom filmatic can be adapted to various materials and grinding conditions. Manufacturers often work with composite blends that optimize lubrication and cooling properties, which are critical for maintaining the integrity of the job. For instance, different grinding operations on metals, plastics, or ceramics may require varying formulations for optimal results. Custom filmatic systems can be engineered to adapt to these different materials and processes, ensuring versatile application without compromise on performance.
Another vital aspect of implementing a custom filmatic solution in centerless grinding is the ecological impact. By optimizing coolant usage and reducing waste, manufacturers can minimize their environmental footprint. Furthermore, advancements in biodegradable coolants can be integrated into these filmatic systems, promoting sustainability in manufacturing practices while still achieving the desirable outcomes in performance and efficiency.
Efficiency gains from custom filmatic systems are also reflected in labor productivity. With consistent application of coolant and proper chip removal, workers spend less time on setup and troubleshooting, allowing them to focus on higher-value tasks. This efficiency can enhance overall production throughput and significantly decrease downtime.
In conclusion, the integration of custom filmatic solutions into centerless grinder machines represents a critical advancement in manufacturing technology. By providing tailored coolant delivery systems, manufacturers can achieve enhanced performance, reduce waste, and ensure sustainability. As competition intensifies and the demand for precision manufacturing grows, adopting these innovations will be key to staying ahead in the industry. The future of centerless grinding is bright, driven by the trends towards customization and efficiency that meet the challenges of modern manufacturing head-on.