In the realm of industrial machinery, the centerless grinder stands out as a vital tool in various manufacturing sectors. These machines are essential for creating precision parts, ensuring smooth surface finishes, and maintaining high production efficiency. When discussing centerless grinders, it is crucial to consider safety protocols and regulations, such as those established by the Occupational Safety and Health Administration (OSHA). Understanding these components can significantly impact the safety, efficiency, and overall success of operations in a factory setting.
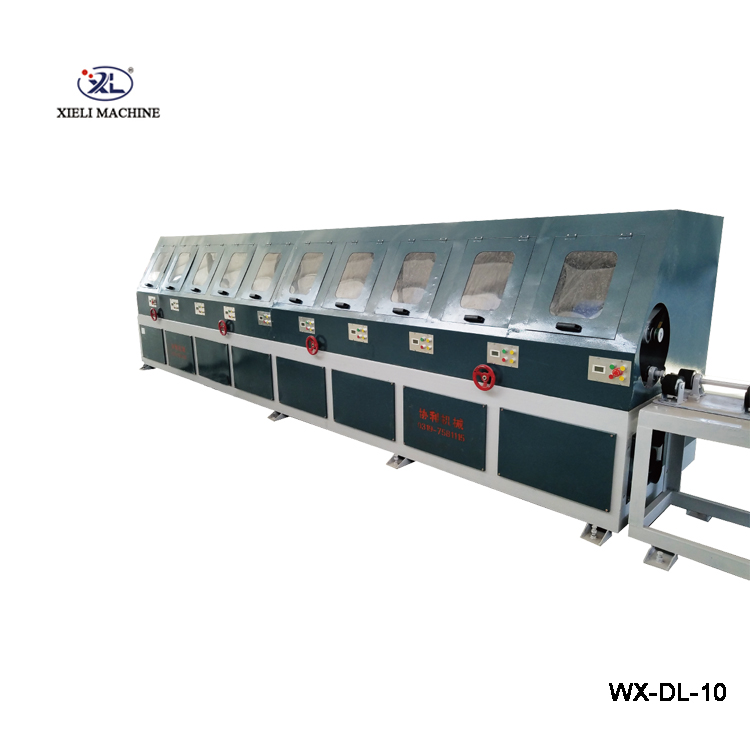
Centerless grinding is a particular method of grinding where workpieces are secured between a regulating wheel and a grinding wheel. The process does not require workpiece spindles, which allows for the rapid processing of various components, enhancing production speeds. While efficient,
the inherent design of centerless grinders poses specific safety challenges. Without the right protective measures, operators can be at risk of injury from high-speed wheels, the handling of heavy materials, and potential mechanical malfunctions.
OSHA guidelines play an instrumental role in mitigating these risks. Adherence to OSHA standards not only assures compliance with federal laws, thus avoiding costly fines and legal issues, but also fosters a safer work environment. These guidelines cover the correct installation, operation, and maintenance of centerless grinding machines. For instance, OSHA mandates the use of appropriate personal protective equipment (PPE) such as goggles, gloves, and ear protection to shield workers from grinding particles and noise. Moreover, adequate training and understanding of emergency stop procedures are vital for all operators to swiftly deal with unexpected events.
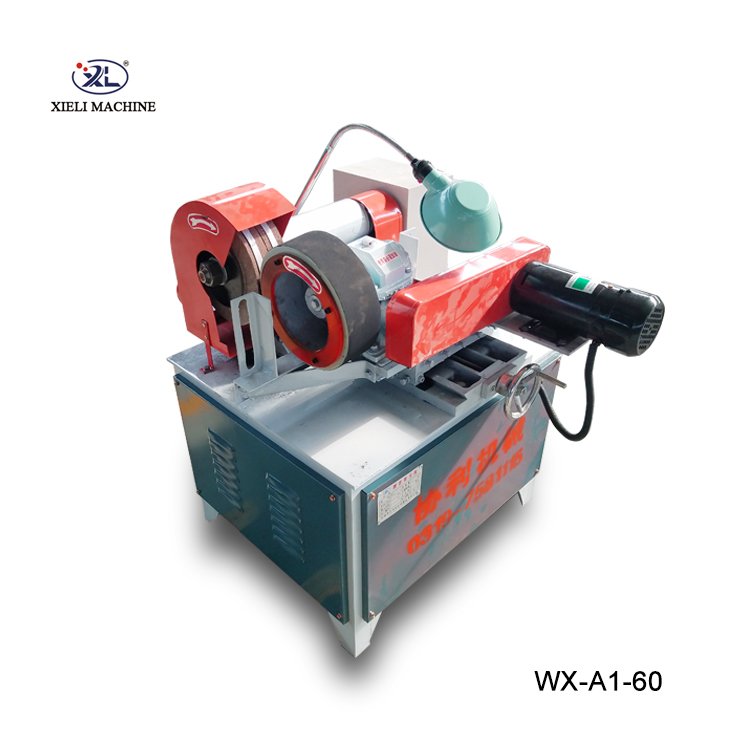
Experience in the field highlights that routine maintenance and inspections are non-negotiable for the safe and efficient use of centerless grinders. Over time, components like grinding wheels and control systems can wear down, leading to diminished performance and potential safety hazards. Factories that commit to regular upkeep schedules experience fewer unexpected downtimes and achieve longer machine lifespans. Furthermore, expertise in selecting the appropriate grinder for specific tasks is crucial. Different models and features are available, making it essential to choose grinders that best match the material characteristics and production requirements.
osha centerless grinder factory
In the pursuit of authoritative expertise, manufacturers often collaborate with seasoned professionals and machinists who understand the nuances of grinding operations. These experts can conduct workshops and practical sessions that equip factory teams with the skills and knowledge to operate centerless grinders safely and efficiently. This ongoing education fosters an environment of continuous improvement and upskilling, crucial for staying competitive in the manufacturing industry.
Trustworthiness is built through transparent operational practices and the consistent demonstration of machine knowledge and capability. Factories often rely on case studies and real-world success stories to showcase their adherence to safety standards and operational excellence. By sharing these experiences, companies not only bolster their reputation in the industry but also provide valuable insights to peers striving to enhance their grinder operations.
In conclusion, centerless grinders are indispensable in various manufacturing domains, but they require careful handling governed by stringent OSHA standards. By prioritizing safety, routine maintenance, and continuous education, factories can significantly elevate their production capabilities. Experience and expertise form the backbone of these efforts, while authoritative practices and trustworthiness establish a factory's standing as a leader in the industrial machinery landscape. For any company looking to optimize their centerless grinder operations, adherence to these principles is not just recommended—it is essential.
For More Details Pls Contact Us
Fiberglass Reinforced Plastic (FRP), also known as fiber-reinforced plastic, is a composite material widely used across various industries.