Understanding Throughfeed Centerless Grinders A Comprehensive Overview
Throughfeed centerless grinding is an efficient machining process that has gained popularity for its ability to produce high volumes of precision components with minimal waste. This technique is primarily used for cylindrical parts, allowing for smooth and seamless production lines that are critical in today’s fast-paced manufacturing environment.
What is Throughfeed Centerless Grinding?
At its core, throughfeed centerless grinding operates on the principle of using wheels to grind the workpiece without the need for any workholding devices. The workpiece is fed through the machine on a platform and is supported by a regulating wheel and a grinding wheel. The regulated wheel controls the feed rate, while the grinding wheel removes material from the surface of the workpiece. The continuous flow of material through the grinding process—hence the name throughfeed—significantly boosts productivity.
Advantages of Throughfeed Grinding
1. High Efficiency One of the primary benefits of throughfeed centerless grinding is its efficiency. The ability to process multiple parts in a single run allows manufacturers to achieve high output without sacrificing quality. This is particularly advantageous in production environments where speed and volume are crucial.
2. Versatility Throughfeed grinders can handle a wide range of part sizes and types, making them suitable for various industries, including automotive, aerospace, and medical devices. This versatility allows manufacturers to adapt quickly to changing production needs without investing in different types of machinery.
3. Reduced Handling Since parts are fed continuously, there is less need for manual handling, which not only speeds up the process but also reduces the risk of operator error and contamination.
4. Precision and Consistency Throughfeed grinding ensures that parts are produced with high precision and repeatability. The process can maintain tolerances as tight as a few microns, making it ideal for producing components that require stringent quality standards.
throughfeed centerless grinder quotes
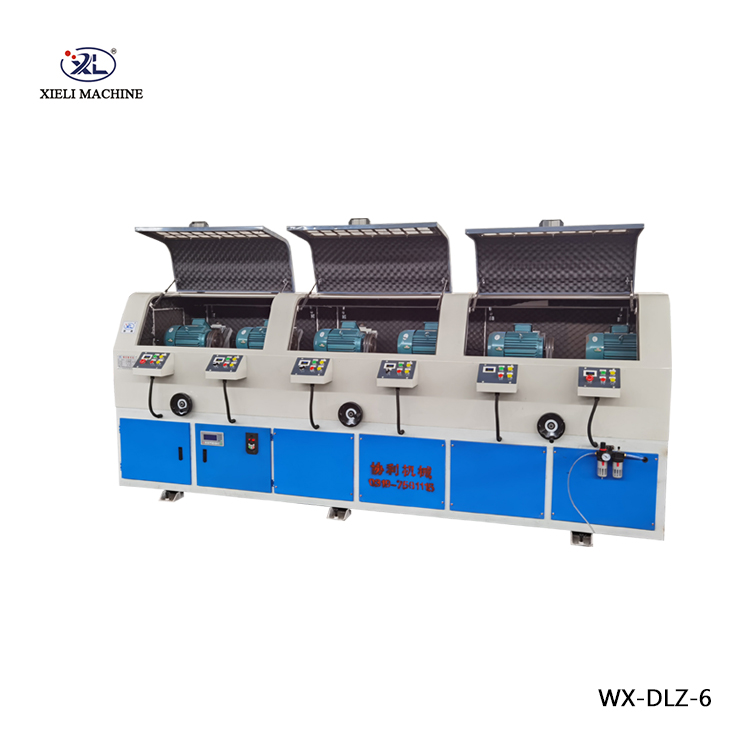
5. Cost-effectiveness Although the initial investment in centerless grinding machinery can be significant, the long-term savings on labor, material waste, and manufacturing time often make it a cost-effective solution.
Key Considerations
While throughfeed grinding boasts numerous advantages, there are essential considerations to keep in mind
1. Part Design Not all components are suitable for throughfeed grinding. Parts must possess a specific design, including an appropriate length-to-diameter ratio, to ensure efficient processing.
2. Material Limitations The materials suitable for throughfeed grinding can be limited. Harder materials may pose challenges during the grinding process, necessitating a careful selection of grinding wheels and parameters.
3. Setup Time While throughput is high, the setup time may be longer compared to other grinding processes, particularly when switching between different part types or sizes. Therefore, consistent production of the same part is preferred to maximize efficiency.
4. Machine Maintenance Regular maintenance is essential to keep the grinding machines in optimal condition, ensuring high precision and extending the machine’s lifespan.
Conclusion
Throughfeed centerless grinders represent a sophisticated and efficient choice for manufacturers looking to enhance their production capabilities. By understanding the mechanics and benefits of this grinding process, companies can leverage technology to improve output, ensure precision, and reduce costs. Investing in throughfeed grinding technology can transform a manufacturing line, enhancing performance and meeting the rigorous demands of various industries. In a world where efficiency and quality are paramount, mastering throughfeed grinding can provide a competitive edge.