Understanding Ovality in Centerless Grinding
Centerless grinding is a widely used machining process that is particularly effective for shaping the external surfaces of cylindrical parts. The technique operates without the need for a fixed spindle, allowing for a continuous process of removing material from a workpiece. While centerless grinding is appreciated for its efficiency and high productivity, it is not without its challenges. One common issue that operators encounter is ovality, a condition where the workpiece takes on an elliptical shape rather than a perfect cylinder. This article delves into the causes, implications, and solutions associated with ovality in centerless grinding.
What is Ovality?
Ovality refers to the deviation of a cylindrical workpiece from its intended circular shape. In precise terms, it is the measure of how much a circle deviates from being a perfect circle, usually expressed as a percentage. This condition can lead to several operational difficulties, such as improper fit in assemblies, increased friction, and premature wear of components. When components do not fit together as designed, it can compromise the entire assembly's performance, leading to costly rework or replacements.
Causes of Ovality in Centerless Grinding
The emergence of ovality in centerless grinding can be attributed to several interrelated factors
1. Setup Issues Inadequate machine setup is one of the primary culprits behind ovality. If the workpiece is not correctly aligned or the centerline of the grinding wheel and workpiece do not coexist properly, it can lead to uneven material removal.
2. Wheel Condition The condition of the grinding wheel also plays a crucial role. A worn or improperly dressed wheel can lead to uneven cutting forces and, consequently, uneven surfaces. This can exacerbate the ovality issues.
3. Workpiece Material Properties The mechanical properties of the workpiece material, such as hardness and ductility, can influence how it behaves under grinding. Variations in these properties can lead to uneven wear, further contributing to ovality.
4. Infeed Rate and Speed The infeed rate and rotational speed of the workpiece are critical parameters. A too-aggressive infeed or an improper speed can cause excessive heat and distortion, leading to shaped deviations.
5. Stability and Vibration The overall stability of the grinding machine can affect ovality. Excessive vibration, either from the machine itself or external sources, can induce irregularities in the grinding process.
ovality in centerless grinder
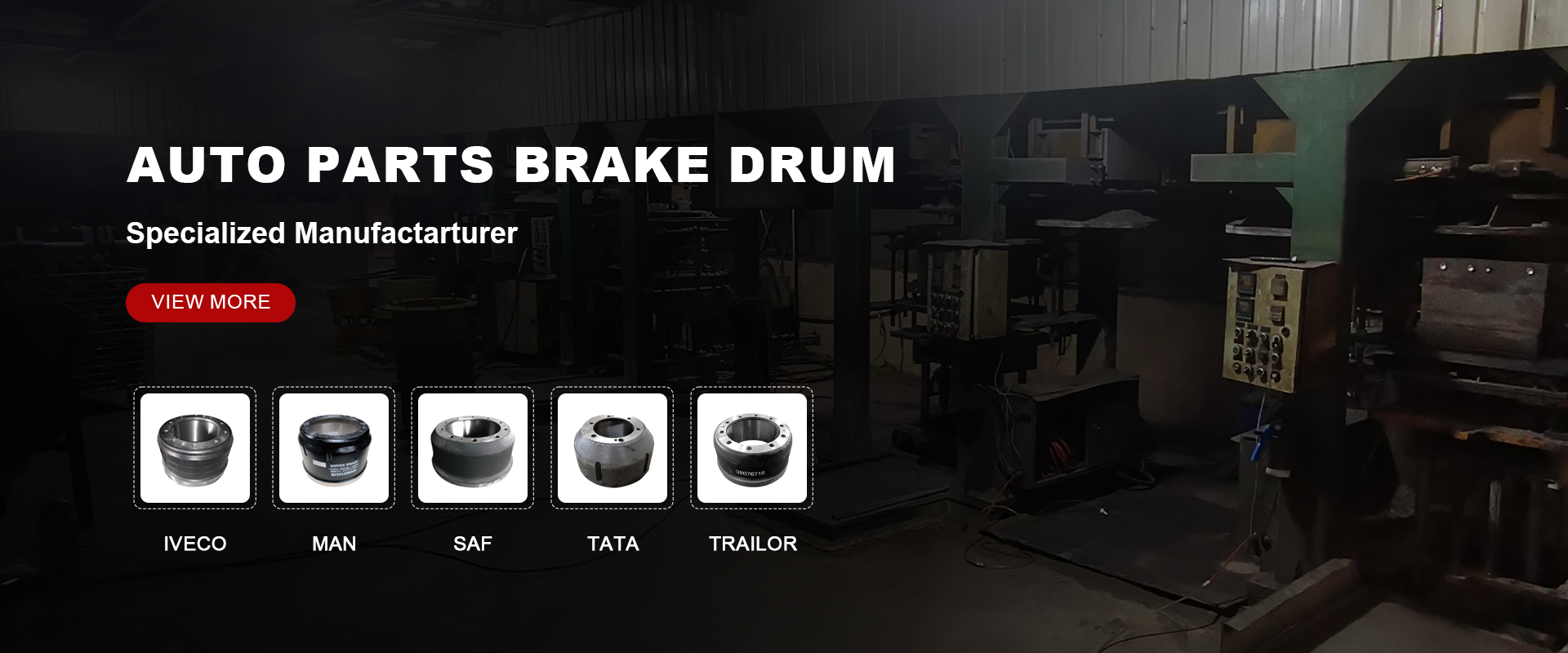
Implications of Ovality
The presence of ovality in machined parts can have significant consequences. For instance, parts that are intended to fit tightly may fail to do so, leading to operational failures. In precision applications, such as in aerospace or automotive industries, ovality can critically affect performance and safety. Furthermore, detecting and correcting ovality can require extensive rework, extending lead times and increasing production costs.
Solutions to Minimize Ovality
To combat ovality in centerless grinding, several best practices can be adopted
1. Proper Setup Ensuring precise alignment of both the workpiece and grinding wheel is critical. Using fixtures that maintain correct positioning can help minimize setup errors.
2. Regular Wheel Maintenance Frequent inspection, dressing, and, when necessary, replacing grinding wheels ensure they remain effective at removing material uniformly.
3. Material Selection Understanding the mechanical properties of the material being machined can help operators adjust parameters to suit the specific behavior of the material.
4. Optimizing Grinding Parameters Operators should carefully determine the optimal infeed rates and speeds to avoid aggressive cutting that could introduce ovality.
5. Stability Improvements Employing vibration damping techniques and ensuring that the grinding machine is placed on a solid foundation can significantly reduce the risk of excessive vibrations.
Conclusion
Ovality in centerless grinding is a multifaceted issue that can arise from various factors including machine setup, material properties, and operational parameters. By understanding these causes and implementing corrective measures, manufacturers can minimize the occurrence of ovality. Ultimately, maintaining shape accuracy is crucial for ensuring the quality and functionality of machined components across various industries. As technology advances, continuous improvements in grinding methods and equipment will further enhance the precision and efficiency of the centerless grinding process.