Homemade Centerless Grinder Manufacturers A Guide to Building Your Own Precision Tool
The world of machining and metalworking continuously evolves, with numerous tools and techniques becoming essential for precision work. Among these, the centerless grinder stands out as an invaluable asset for achieving high levels of accuracy and repeatability in cylindrical workpiece processing. However, commercial centerless grinders can be costly, prompting hobbyists and small manufacturers to consider the possibility of creating their own homemade solutions.
Understanding the Centerless Grinding Process
Before delving into the construction of a homemade centerless grinder, it's important to grasp the fundamentals of how centerless grinding operates. Unlike traditional grinding methods that use fixtures to hold the workpiece, centerless grinding relies on the support of two rotating wheels—the grinding wheel and the regulating wheel. This setup allows the workpiece to be held in place without the need for central fixtures, facilitating a continuous and uninterrupted grinding process conducive to high production rates.
Benefits of Homemade Centerless Grinders
1. Cost Savings The primary advantage of building your own centerless grinder is cost efficiency. Commercial options can range from thousands to tens of thousands of dollars, whereas a homemade version can be constructed with recycled materials and lower-cost components.
2. Customization One of the most significant benefits of a homemade tool is the ability to tailor features to specific needs. Builders can adjust dimensions, motor types, and grinding wheel specifications based on the unique requirements of their projects.
3. Skill Enhancement The process of designing and constructing a centerless grinder offers valuable hands-on experience that enhances not only mechanical skills but also engineering principles and problem-solving abilities.
Key Considerations for Building Your Own Centerless Grinder
homemade centerless grinder manufacturers
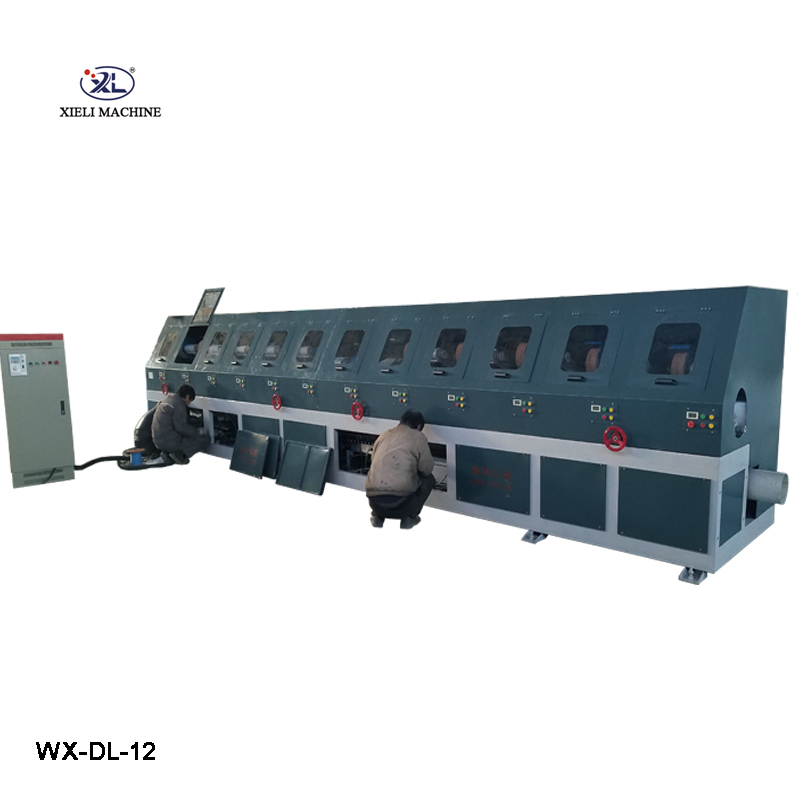
1. Design Proper design is crucial. A basic understanding of the mechanics involved in centerless grinding will help in creating an effective layout. Considerations should include the size of the workpieces, the materials to be ground, and the desired finish.
2. Materials Selecting appropriate materials is essential for durability and performance. Commonly used materials include steel for the frame, bearings for smooth rotation, and various types of wheels designed for the specific grinding task.
3. Motor Choice The motor used will significantly affect the grinding speed and efficiency. A variable-speed motor can provide versatility, allowing operators to adjust the speed according to the material being processed.
4. Safety Features Incorporating safety mechanisms is non-negotiable. Due to the nature of high-speed grinding, it is vital to include guards and emergency stop buttons to ensure safe operation.
5. Research and Prototyping Before embarking on the full build, research existing designs and gather insights from experienced builders. Prototyping your design with smaller components can help identify potential issues and streamline the construction process.
Resources and Community Support
Various online platforms and forums dedicated to machining enthusiasts provide excellent resources for those interested in building a homemade centerless grinder. Videos, schematics, and step-by-step guides from seasoned makers can offer invaluable insights. Engaging with a community can provide troubleshooting advice and inspiration from others who have successfully tackled similar projects.
Conclusion
Creating a homemade centerless grinder can be a rewarding venture, combining engineering knowledge with practical skills. By carefully considering design, materials, and safety, hobbyists and small manufacturers can produce high-quality grinders that significantly enhance their machining capabilities. The journey not only equips builders with a powerful tool but also fosters a deeper understanding of the grinding process—an essential aspect of precision manufacturing.