Custom Throughfeed Centerless Grinder Elevating Precision Machining
In today's fast-paced manufacturing landscape, precision and efficiency are paramount. For industries requiring high-accuracy cylindrical parts, custom throughfeed centerless grinders have emerged as vital tools that enhance productivity while ensuring superior quality. These advanced machines are tailored to meet the specific needs of various applications, thereby driving innovation in manufacturing processes.
Understanding Throughfeed Centerless Grinding
Centerless grinding is a machining process that removes material from a workpiece while it is held between two grinding wheels. Unlike traditional grinding methods, where the workpiece is held in a fixture, throughfeed centerless grinding allows for continuous movement of the workpiece through the grinder. This results in remarkable productivity gains, making it an ideal choice for high-volume production.
In a custom throughfeed centerless grinder setup, the design is modified to accommodate unique shapes, sizes, and materials specific to the client's needs. This customization ensures that manufacturers can achieve the desired tolerances and surface finishes vital for their components.
Benefits of Customization
1. Tailored Solutions Each manufacturing operation has distinct requirements, and a custom throughfeed grinder can be engineered to meet these specifications. Whether it's for grinding different workpiece diameters, lengths, or specific materials, customization allows manufacturers to optimize their processes effectively.
2. Enhanced Efficiency A well-designed custom grinder can significantly reduce cycle times, enabling manufacturers to produce more parts in less time. The throughfeed mechanism minimizes setup times and ensures that parts can be continually fed into the grinder without interruption.
3. Improved Quality Control With precise engineering and design, custom grinders can achieve higher levels of accuracy and consistency. This leads to superior surface finishes and tighter tolerances, which are essential in industries like automotive, aerospace, and medical device manufacturing.
custom throughfeed centerless grinder
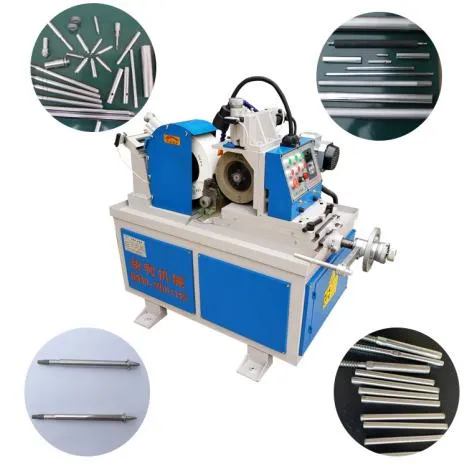
4. Adaptability As customer demands and market conditions evolve, the ability to customize grinding equipment becomes increasingly valuable. Manufacturers can adapt their machinery to accommodate new production challenges, ensuring they stay competitive.
Applications of Custom Throughfeed Centerless Grinders
Custom throughfeed centerless grinders are utilized across various industries, including
- Automotive In the automotive sector, these grinders are crucial for manufacturing components like fuel injectors, shafts, and bearings, where precision is critical for performance and safety.
- Aerospace The aerospace industry requires components that can withstand extreme conditions. Custom grinders can produce parts with the precise specifications needed for engines and fuselage components.
- Medical Devices The manufacture of medical instruments and implants requires stringent quality and precision. Custom grinders ensure that these devices meet the necessary regulatory standards while delivering outstanding performance.
- General Manufacturing Various factory operations benefit from the speed and efficiency of throughfeed grinding, allowing for rapid production cycles and meeting diverse manufacturing needs.
Conclusion
The evolution of custom throughfeed centerless grinders marks a significant advancement in the machining sector. By integrating cutting-edge technology with tailored solutions, manufacturers can achieve higher levels of precision, efficiency, and adaptability. As industries continue to demand smaller tolerances and faster production rates, the role of custom throughfeed centerless grinders will undoubtedly become even more integral to the manufacturing process, enabling companies to thrive in a competitive marketplace. By investing in these innovative machines, manufacturers can ensure they are well-equipped to meet current and future challenges while delivering high-quality products.