Exploring the intricacies of Cincinnati centerless grinder parts unveils a world where precision meets excellence in machining. In the heart of manufacturing, where machines operate with unparalleled efficiency, these grinder parts play a crucial role in shaping the future of industry. Cincinnati machines, recognized for their reliability and precision, are a staple in many workshops around the globe.
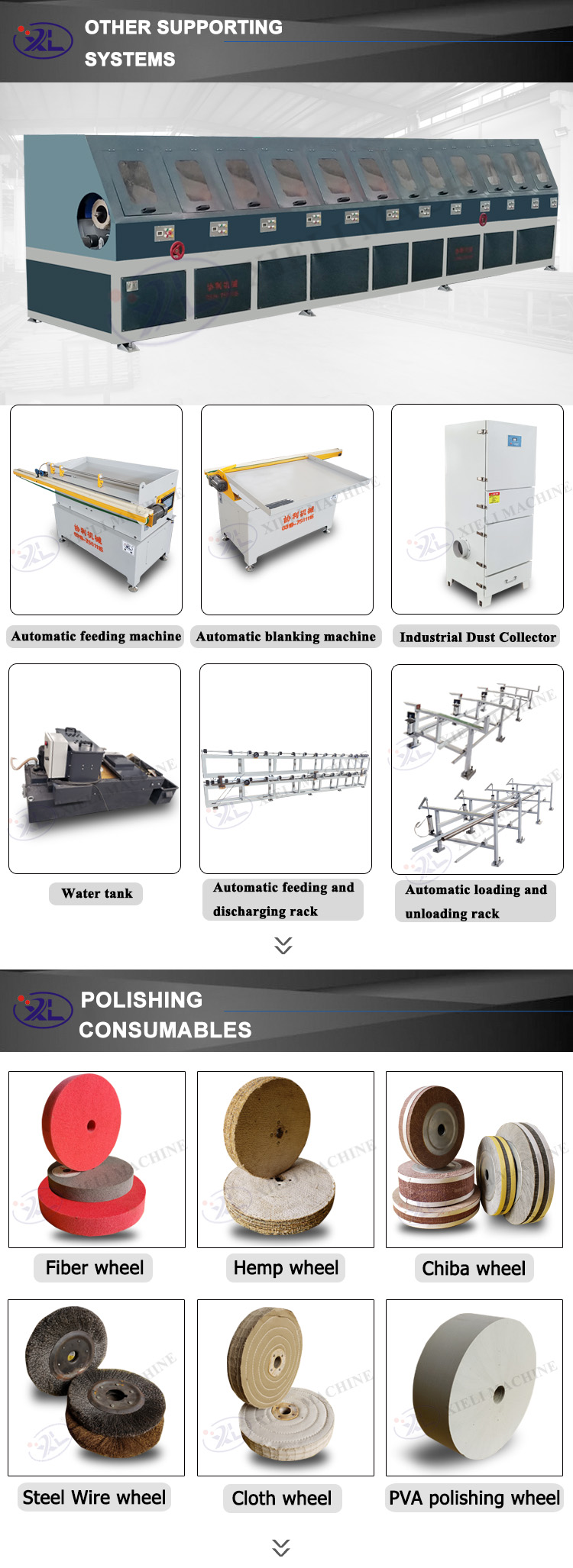
Cincinnati centerless grinders are renowned for their ability to deliver exceptional precision and high productivity levels. The essence of their performance lies in the parts that makeup these sophisticated machines. From wheels to spindles, each component must meet rigorous standards to ensure seamless operation and optimal output. Customization is often the key; many users opt for parts specifically tailored to their manufacturing processes, enhancing both the machine's efficiency and longevity.
One of the standout components is the grinding wheel. Selecting the right wheel is paramount, as it directly impacts the quality of the finished product. A thorough understanding of material compatibility, grit size, and bond type is essential for achieving the desired outcomes. Experienced operators often conduct tests to gauge the effectiveness of different grinding wheels, adjusting variables until the sweet spot of productivity and precision is attained.
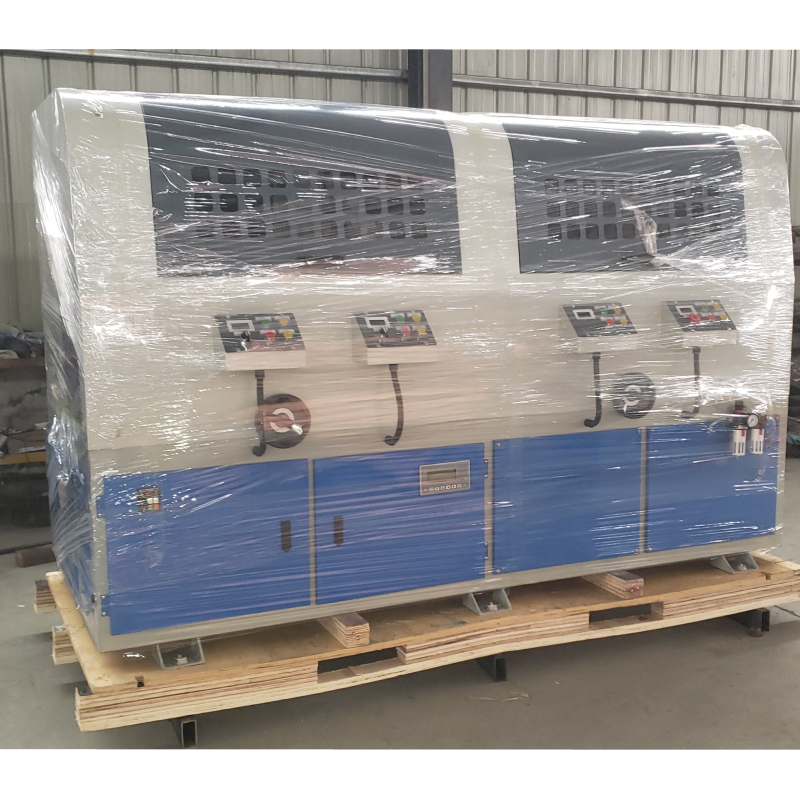
Not to be overlooked are the machine's spindles. They serve as the backbone of the grinder's operation, responsible for the rotation of the grinding wheel. High-quality spindles are characterized by their durability and ability to maintain accuracy under high-stress conditions. In the realm of centerless grinding, where even minuscule deviations can lead to substantial discrepancies, high-precision spindles are indispensable.
Another critical area is the selection of regulating wheels. These components dictate the speed and direction of the workpiece. In scenarios demanding high-output volumes, speed control becomes a focal point. The choice of regulating wheels should align with specific production requirements, ensuring consistency and precision throughout the process.
cincinnati centerless grinder parts
Moreover, the role of automated systems in enhancing the efficiency of Cincinnati grinders cannot be underestimated. Integration of automation in part replacement and adjustment can significantly reduce downtime, thus boosting productivity. Workshops that embrace such technologies often witness exponential improvements in their operational workflows.
The expertise required to maintain and replace Cincinnati centerless grinder parts is significant. Regular training and knowledge updates for technicians enable smooth operations and prevent costly downtimes. Many manufacturers offer specialized training sessions to equip their workforce with the necessary skills to manage these advanced machines. Acquiring technical knowledge directly from these sessions or through mentorship programs with seasoned professionals is invaluable.
In the competitive landscape of manufacturing, standing out requires a blend of superior technology and skilled operation. Cincinnati centerless grinders, with their robust design and focus on precision, exemplify this synergy. By investing in high-quality parts and ensuring that operational knowledge is top-notch, businesses can achieve unprecedented levels of efficiency and product quality.
In summary, the world of Cincinnati centerless grinder parts is a domain where precision, knowledge, and innovation intersect. Through expert selection and maintenance of these critical components, businesses can ensure that their operations not only meet but exceed industry standards. Embracing advancements and fostering continuous learning within teams will pave the way for future successes in manufacturing precision tools and components.
For More Details Pls Contact Us
Fiberglass Reinforced Plastic (FRP), also known as fiber-reinforced plastic, is a composite material widely used across various industries.