Centerless Grinding on Surface Grinders A Comprehensive Overview
Centerless grinding is a precision machining process that has become increasingly popular in various manufacturing industries. This technique involves the grinding of cylindrical parts without the necessity for centering the workpiece, allowing for enhanced efficiency and productivity. While centerless grinding is commonly associated with dedicated centerless grinding machines, surface grinders can also be adapted for this purpose, merging versatility with precision.
The primary advantage of centerless grinding is the elimination of the need for a fixture to hold the workpiece. Instead, the workpiece is supported by a combination of a regulating wheel and a grinding wheel, allowing for continuous operation and unattended grinding. This setup not only speeds up the machining process but also significantly reduces the risk of workpiece damage, which is often encountered in traditional grinding methods.
When employing surface grinders for centerless grinding applications, several considerations come into play. The surface grinder must be equipped with appropriate fixtures and modifications to support the centerless setup. With the right adjustments, surface grinders can achieve similar results to dedicated centerless grinding machines while still offering the flexibility to switch between different grinding operations.
centerless grinding on surface grinder products
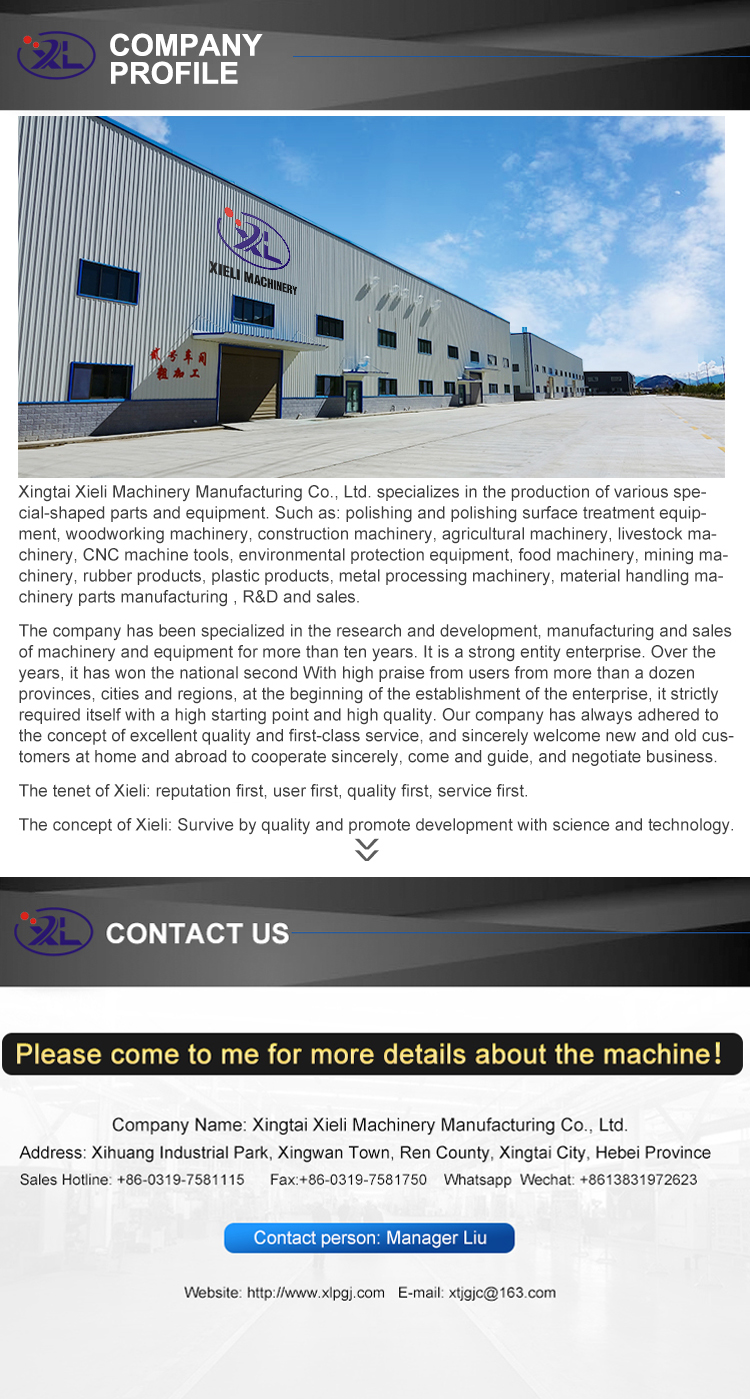
The versatility of surface grinders is a significant benefit in a manufacturing environment where diverse machining tasks are prevalent. This adaptability can lead to reduced setup times and a more streamlined workflow. The centerless grinding process allows manufacturers to produce high-precision components with improved surface finishes, making it an attractive option for industries such as automotive, aerospace, and general engineering.
Another critical aspect of centerless grinding on surface grinders is the ability to maintain tight tolerances. The uniformity achieved through this method is essential for parts that require precise dimensions and surface qualities. The interplay between the regulating wheel and the grinding wheel is crucial; adjustments can be made to control the speed and angle of the wheels, resulting in better control over the grinding process.
Moreover, the proper selection of abrasives and grinding parameters is vital for optimizing the performance in a centerless grinding setup. Different materials may require specific types of grinding wheels to achieve the desired finish and durability. Understanding the material removal rates and the thermal aspects of the grinding process can lead to improved efficiency and longer tool life.
In conclusion, integrating centerless grinding on surface grinders offers a unique approach to enhancing productivity and precision in manufacturing. With the right setups and parameters, manufacturers can leverage the capabilities of surface grinders to achieve efficient, high-quality results. As technology advances, the combination of these techniques is likely to become even more prevalent, further pushing the boundaries of what is achievable in precision machining. Ultimately, centerless grinding on surface grinders allows for a flexible and efficient solution tailored to the diverse needs of modern manufacturing.