When it comes to precision machining, the centerless grinder stands out as a revolutionary innovation in the field of manufacturing. Unlike traditional grinding, where the workpiece is held between two centers, centerless grinding uses a work-rest blade to support the piece. This subtle yet powerful difference offers significant advantages, especially in mass production.

Centerless grinders are renowned for their ability to deliver high throughput without compromising on quality. This efficiency stems from the fact that there is no need for centering the workpiece, resulting in minimal setup time. Industries have seen dramatic reductions in lead times, especially when it comes to producing parts like automotive components, aerospace elements, and precision surgical instruments. This efficiency not only shortens the time from design to production but also significantly reduces costs, making it a compelling choice for manufacturers looking to streamline operations while maximizing profitability.
The precision and accuracy delivered by centerless grinders cannot be overstated. With capabilities to achieve tolerance levels as tight as 0.0001 inches,
these machines are at the pinnacle of grinding technology. This superb precision is essential in today’s manufacturing landscape, where even the smallest deviation can lead to catastrophic results in product performance. For instance, in the aerospace industry, where safety is paramount, the flawless execution of parts through centerless grinding can mean the difference between success and failure.
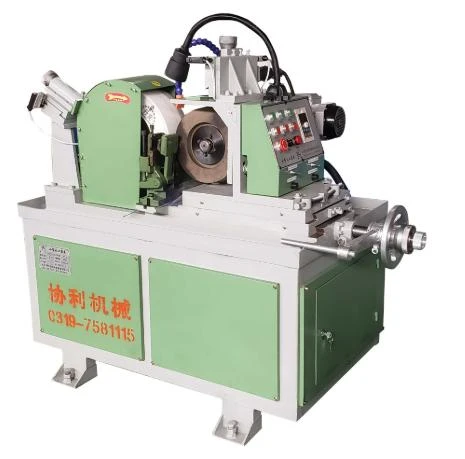
Another notable factor is the versatility of centerless grinders. These machines can work with a diverse range of materials, from everyday metals to exotic alloys and even composite materials. This adaptability is fueled by advancements in abrasive technology and machine design, allowing manufacturers to explore new possibilities in product design and material usage. Whether it’s hard-to-machine titanium for aircraft or stainless steel for medical devices, the centerless grinder offers a reliable and efficient solution.
centerless grinder
From an expertise standpoint, operating a centerless grinder requires skilled personnel who understand both the machinery and the nuances of material behavior. The operator’s ability to adjust parameters such as the speed of the rotation and feed rate is crucial. This expertise ensures that the final product not only meets quality standards but also adheres to the precise specifications required by engineers.
Moreover, the investment in centerless grinding technology signals a commitment to product excellence and innovation. It establishes a manufacturer’s authority in the field by showcasing their dedication to utilizing cutting-edge technology to produce premium quality parts. Companies that employ this technology are seen as leaders in manufacturing, setting benchmarks for quality and reliability in the industry.
Trustworthiness is naturally built over time, as the consistent delivery of superior quality parts strengthens relationships with clients. Manufacturers using centerless grinders can assure their customers of unrivaled quality and precision, fostering partnerships based on trust and dependability.
In conclusion, the centerless grinder is not just a piece of equipment; it represents a paradigm shift in manufacturing excellence. Its ability to deliver unparalleled precision, efficiency, and versatility is transforming industries and setting new standards for quality and performance. For manufacturers committed to staying at the forefront of innovation, investing in centerless grinding technology is not just wise—it’s essential.
For More Details Pls Contact Us
Fiberglass Reinforced Plastic (FRP), also known as fiber-reinforced plastic, is a composite material widely used across various industries.