Understanding Centerless Grinder Parts and Their Importance in Manufacturing
Centerless grinding is a precise manufacturing process widely used in various industries to create cylindrical components. This process is distinct from traditional grinding methods, as it does not require the part to be centered. Instead, the part is held in place by a support blade and ground between a grinding wheel and a regulating wheel. The importance of this technique lies not only in its efficiency but also in the critical role played by the individual parts of the centerless grinder.
Key Components of Centerless Grinders
1. Grinding Wheel The grinding wheel is arguably the most critical part of a centerless grinder. It is responsible for removing material from the workpiece. Wheels are made from various materials, including aluminum oxide or silicon carbide, depending on the specific application. The choice of wheel diameter, width, and grit affects the surface finish and the rate of material removal.
2. Regulating Wheel This component works in tandem with the grinding wheel to control the speed at which the workpiece is fed through the grinder. The regulating wheel is typically set at a lower speed than the grinding wheel and is crucial for maintaining the precision of the grinding process.
3. Work Support Blade The work support blade plays an essential role in holding the workpiece steady during the grinding process. This component must be expertly aligned and adjustable, as it can significantly influence the precision and quality of the final product.
4. Machine Frame The machine frame provides stability and rigidity to the grinding setup. A well-constructed frame minimizes vibrations and contributes to consistent grinding, which is vital for maintaining high tolerances.
5. Feed Mechanism The feed mechanism determines how the workpiece is advanced through the grinder. Whether it’s manual or automated, the feed system can significantly influence the operational efficiency and accuracy of the grinding process.
6. Coolant System Effective cooling is necessary to prevent overheating, which can affect both the grinder’s performance and the integrity of the workpiece. A well-designed coolant system will help maintain the temperature and prolong the life of grinding wheels.
centerless grinder parts factories
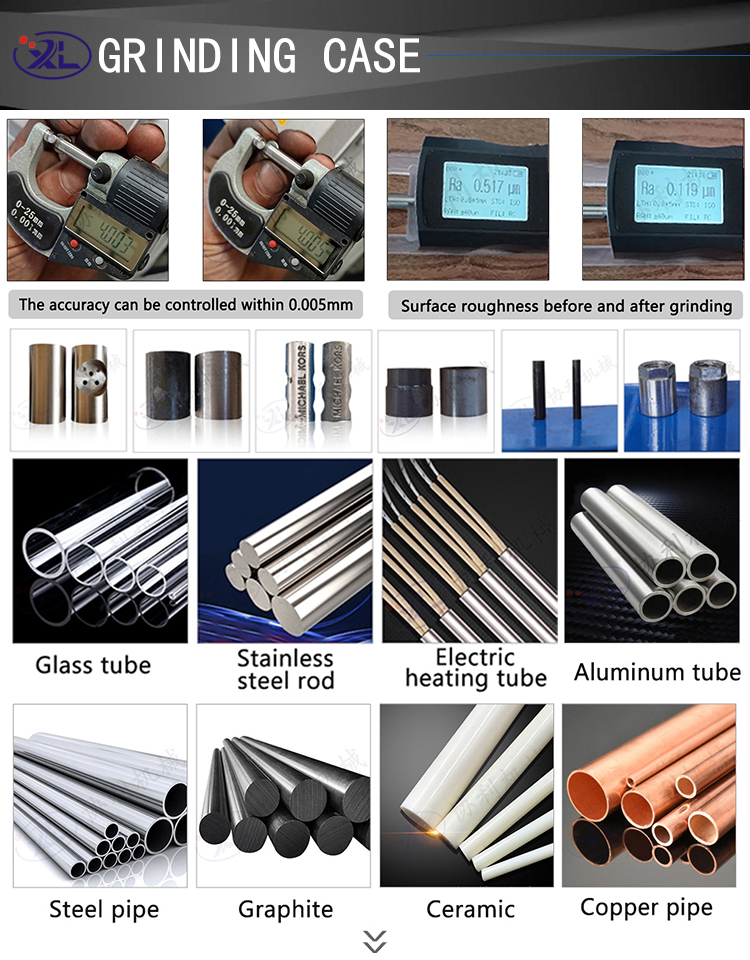
Importance of Quality Parts
The performance of a centerless grinder is heavily influenced by the quality of its parts. Factories specializing in manufacturing these components must adhere to strict tolerances and standards. High-quality parts not only enhance the operational efficiency of grinders but also reduce downtime and maintenance costs.
Using subpar components can lead to issues such as excessive wear and tear, reduced precision, and increased vibrations, all of which can compromise the manufacturing process. Therefore, it’s crucial for manufacturers to source their components from reputable factories that prioritize quality and adhere to industry standards.
The Role of Innovation in Component Manufacturing
As technology advances, the manufacturing of grinder parts is also evolving. Innovations in materials science and engineering have led to the development of more durable and efficient components. For instance, advancements in ceramic bonding technologies have resulted in grinding wheels that offer better performance and longer life.
Moreover, automation in the manufacturing of centerless grinder parts is becoming more prevalent. Utilizing CNC machines and robotic automation can significantly enhance precision and consistency, ensuring that each part meets the required specifications.
Conclusion
In conclusion, centerless grinder parts are integral to the success of precision manufacturing processes that produce cylindrical components. Understanding the function and importance of each part, as well as the quality and innovation in their production, is vital for manufacturers aiming for operational efficiency and product excellence. As industries continue to advance, the significance of high-quality grinder parts will only grow, driving the need for continuous improvement and innovation in part manufacturing.