Centerless grinders represent one of the pinnacle achievements in machining technology, offering unparalleled advantages in precision and throughput for an array of industries. At the heart of their functionality lies the tooling – the unsung hero which ensures the machine operates at its maximum capacity. Understanding and optimally utilizing centerless grinder tooling is paramount for anyone striving to excel in this field.
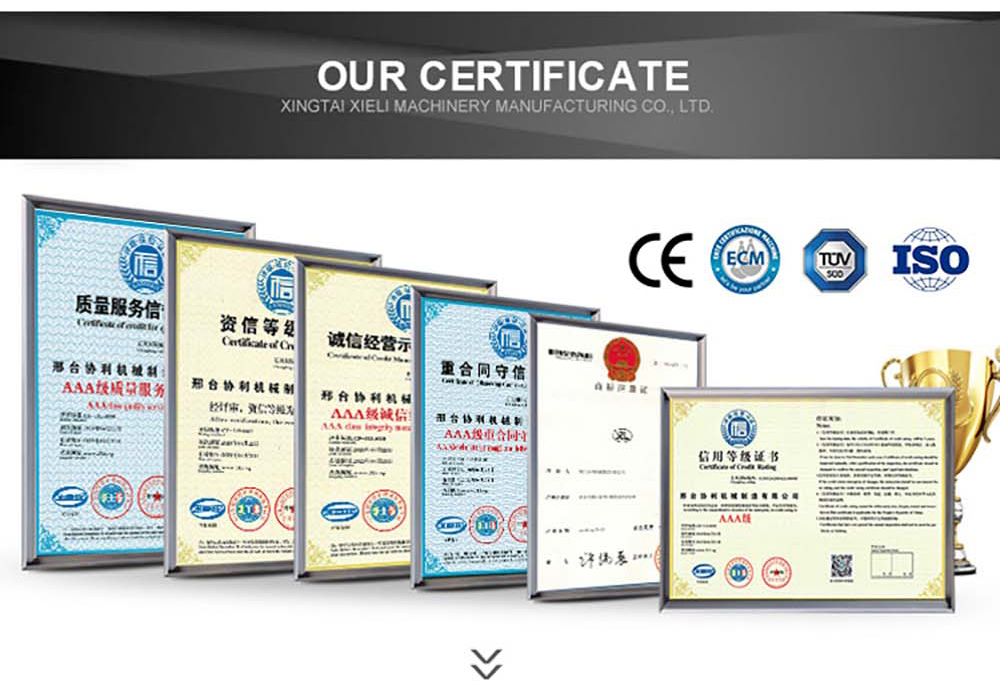
Precision tooling in centerless grinders revolves fundamentally around two key components the grinding wheel and the regulating wheel. These components must be carefully selected and precisely balanced to achieve specific machining tasks. The choice of the grinding wheel itself depends on several critical factors including material hardness, type, desired finish, and the rate of material removal. Grinding wheels come in various abrasive types, predominantly aluminum oxide and silicon carbide, and their grains are bonded together in multiple ways to optimize efficiency and durability.
A high degree of expertise is required to select the appropriate tooling, as even small inaccuracies can lead to inefficiencies or defects. For example, utilizing a grinding wheel with incorrect grit size could distort the workpiece, leading to potential project setbacks. Experts in the field recommend continuous assessment and adjustment of these components to maintain precision and efficiency.
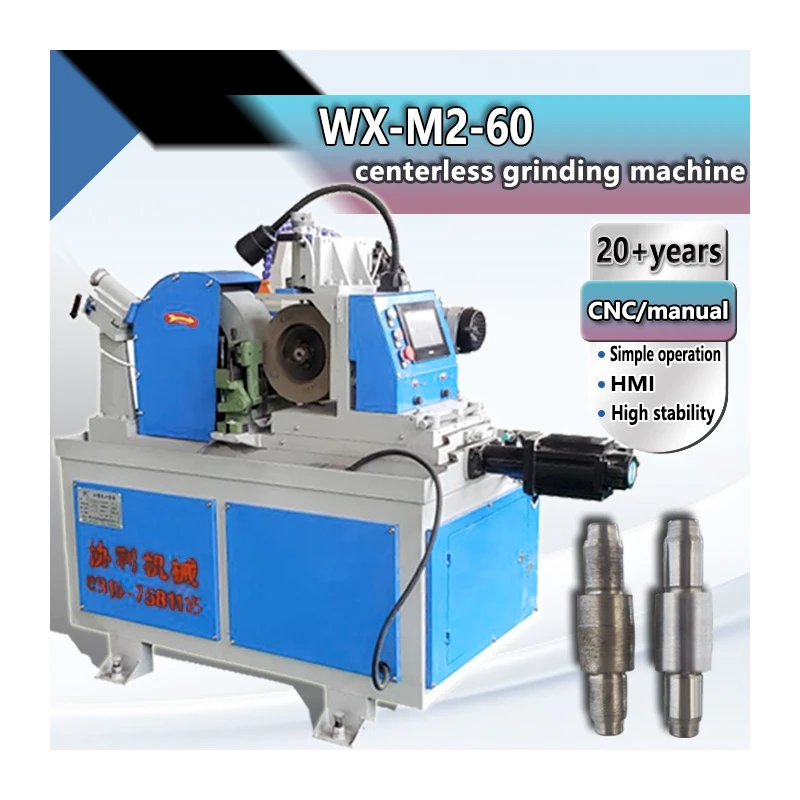
Regulating wheels, meanwhile, directly contribute to maintaining the stability of the workpiece as it passes through the grinding wheel. This critical component ensures a consistent and even grinding process, granting the operator control over the speed and feed rate. An expert understanding of the relationship between these parameters is essential. For instance, a finer grit on the regulating wheel may offer better control but could also slow the process, so adjustments must reflect the specific requirements of the task at hand.
In addition to the primary components, there are supporting elements that compound the success of centerless grinder tooling.
These include tooling fixtures and dressing tools. Tooling fixtures are crucial in providing the necessary stability to support the workpiece and control vibration, which can adversely affect the precision and surface integrity. Advanced setup techniques and clamping systems are often adopted to exploit the full potential of the grinder tooling.
centerless grinder tooling
Moreover, the dressing tools play a pivotal role in maintaining the condition and performance of the grinding and regulating wheels. Regular dressing not only extends the lifecycle of the wheels but also ensures that they perform accurately. This aspect of grinder tooling demands a profound understanding of the materials and their interactions, reinforcing the necessity for skilled personnel to ensure peak performance.
Trustworthiness in the tool selection process can be enhanced through collaboration with reputable suppliers who provide technical support as well as validated, high-quality materials. Using tooling from verified sources minimizes the risk of unexpected failures and helps maintain operational credibility. Furthermore, regular training and updated procedural manuals for machinery calibrations can bolster the authority of the operators and the institution, ensuring that practices are consistent with the current standards in machining technology.
While centerless grinder tooling may not hold the spotlight in everyday discussions, its importance cannot be understated within high-precision manufacturing environments. The ability to expertly select, manage, and maintain these components ensures that industries continue to produce with the highest standards of accuracy and efficiency. To cultivate such expertise, practitioners must embrace a commitment to ongoing learning and adaptation in this technologically versatile field.
This commitment to precision and expertise ensures that the use of centerless grinder tooling not only meets but exceeds expectations in performance, providing an essential cornerstone in the world of advanced manufacturing and machining. Through such diligent practice and the operational mastery of tooling, the door to unparalleled production capacity and product excellence remains wide open.
For More Details Pls Contact Us
Fiberglass Reinforced Plastic (FRP), also known as fiber-reinforced plastic, is a composite material widely used across various industries.