Troubleshooting Centerless Grinders A Guide for Suppliers
Centerless grinders play a vital role in various manufacturing processes, primarily in the precision grinding of cylindrical parts. However, like any other machinery, they can encounter issues that affect their performance. Understanding these problems and their solutions is essential for suppliers who want to offer exceptional service to their customers. This article outlines common troubleshooting strategies for centerless grinders.
Common Issues in Centerless Grinding
1. Workpiece Not Being Ground Properly One of the most frequent issues is the workpiece not receiving the correct finish. This can be caused by several factors, including incorrect wheel alignment, improper feed rate, or worn grinding wheels. Suppliers should educate operators to check alignment regularly and recalibrate machines as necessary.
2. Inconsistent Part Size If parts are coming out with varying sizes, it may indicate a problem with the grinding wheel or the setup of the machine. Suppliers can recommend a thorough inspection of the grinding wheel for wear and ensure that the part's references and dimensions are properly set up. Regular maintenance checks can prevent this issue from recurring.
3. Excessive Wheel Wear Grinding wheels can wear unevenly, leading to inefficiencies and increased costs. Factors contributing to excessive wheel wear might include incorrect wheel speed, inappropriate feed rates, or using the wrong type of wheel for the material being processed. Suppliers should guide customers on selecting the right wheels and parameters for their specific applications.
Best Practices for Trouble-Free Grinding
centerless grinder troubleshooting suppliers
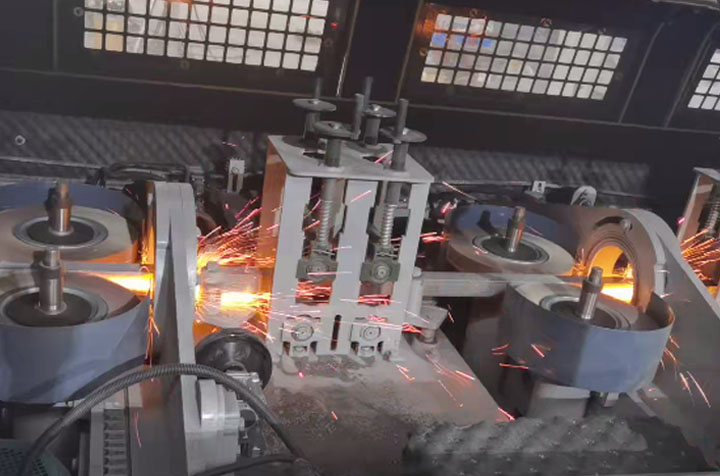
1. Routine Maintenance Regular maintenance is crucial for preventing issues. Suppliers should emphasize the importance of keeping machinery clean and well-lubricated. A maintenance schedule that includes checking the alignment, inspecting wheels, and cleaning can greatly enhance the longevity of the grinder.
2. Training Operators Well-trained operators are indispensable in minimizing troubleshooting issues. Suppliers should offer comprehensive training programs that cover machine operation, troubleshooting techniques, and safety measures. Knowledgeable operators can quickly identify problems and take corrective actions.
3. Adopting Technology Modern centerless grinders often come equipped with advanced diagnostic tools and monitoring systems that can preempt potential issues. Suppliers should encourage their customers to utilize these technologies to track machine performance and identify anomalies before they escalate into major problems.
4. Keeping Spare Parts Having essential spare parts readily available can significantly reduce downtime in the event of a malfunction. Suppliers should offer a wide range of replacement parts for the different makes and models of centerless grinders and advise their customers on which parts to stock based on their usage patterns.
Conclusion
Centerless grinders are pivotal in achieving precision in manufacturing. For suppliers, understanding common issues and their solutions is not just beneficial but essential for enhancing customer satisfaction. By providing training, emphasizing maintenance, and encouraging the use of technology, suppliers can ensure that their customers are equipped to troubleshoot and resolve issues effectively. Offering support in these areas can establish stronger relationships and drive long-term success in the competitive manufacturing industry.