The Importance of Coolant in Centerless Grinding
Centerless grinding is a precision manufacturing process that plays a pivotal role in shaping and finishing workpieces with tight tolerances and superior surface quality. Among the various components of a centerless grinding system, coolant remains one of the most crucial elements, significantly affecting both the grinding process and the overall performance of the machinery. This article will explore the essential role of coolant in centerless grinding, the types of coolants available, and best practices for their use.
Role of Coolant in Centerless Grinding
During the centerless grinding process, the grinding wheel plays a vital role in removing material from the workpiece. However, this generates heat due to friction, which can adversely impact both the grinder and the workpiece. Excessive heat can lead to several problems, such as decreased grinding efficiency, loss of dimensional accuracy, and even thermal damage to the workpiece. This is where coolant comes into play.
Coolant serves multiple functions during the grinding operation
1. Temperature Control The primary function of coolant is to dissipate heat generated during grinding. By maintaining an optimal operating temperature, coolant helps prevent warping, cracks, or other thermal defects in the workpieces.
2. Lubrication Coolants possess lubricating properties that reduce friction between the grinding wheel and the workpiece, extending the life of both components. Efficient lubrication can lead to a smoother grinding process and a better finish on the workpiece.
3. Chip Removal The grinding process generates metal chips and particulate matter that can contaminate the work area and affect grinding performance. Coolant helps carry these chips away from the grinding zone, preventing recirculation and buildup that could lead to defects.
4. Surface Integrity Proper coolant flow can result in improved surface finishes on the workpiece. By effectively cooling and lubricating the grinding area, coolants help achieve a superior finish while maintaining dimensional accuracy.
Types of Coolants
There are various types of coolants suited for use in centerless grinding operations
. These includecenterless grinder coolant
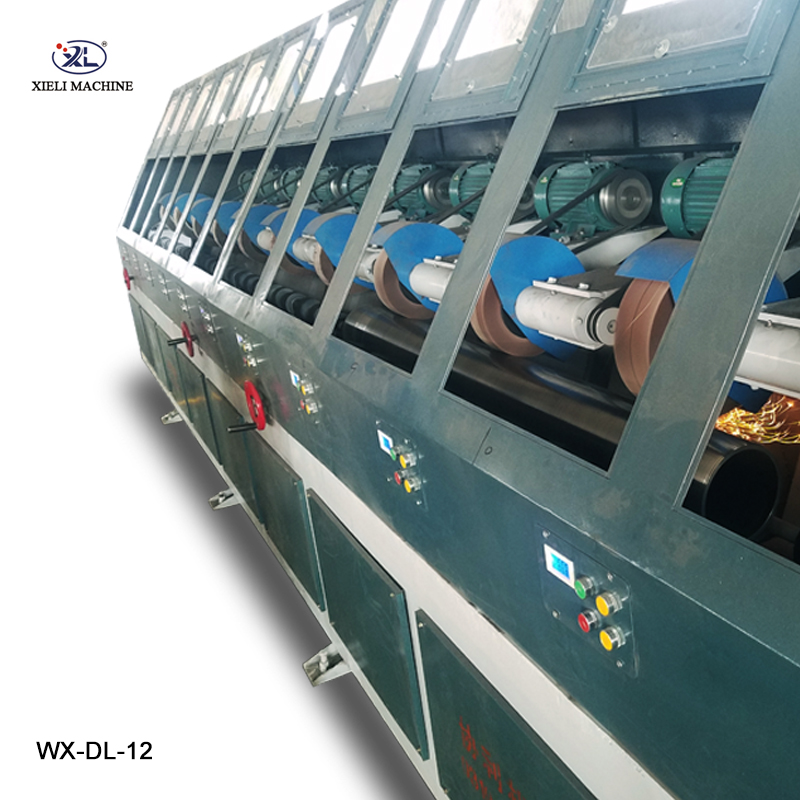
1. Water-Soluble Oils These emulsions are created by mixing oil with water, providing excellent cooling and lubrication properties. They are widely used due to their cost-effectiveness and efficient heat dissipation capabilities.
2. Straight Oils These oils are oil-based, providing superior lubrication but less effective cooling compared to water-soluble oils. They are often used for specific applications where lubricity is critical.
3. Synthetic Coolants These coolants consist of a combination of chemicals that provide excellent cooling properties and inhibit rust and corrosion. Synthetic coolants can often offer longer service life and better performance than traditional oils.
Best Practices for Coolant Use
To maximize the benefits of coolant in centerless grinding, users should adhere to several best practices
1. Regular Monitoring and Maintenance Frequent checks of coolant concentration and quality are essential. Ensure that contamination from metal chips or foreign particles is minimized, and replace coolant as necessary.
2. Correct Application Properly applying coolant directly to the grinding zone can maximize its effectiveness. This might involve using high-pressure systems or fine nozzles for optimal fluid delivery.
3. Temperature Control Keep the coolant within the recommended temperature range to maintain its effectiveness in cooling and lubrication.
4. Choosing the Right Coolant Match the coolant type to the material being ground and the specific requirements of the grinding operation for optimal results.
Conclusion
In summary, coolant is an indispensable component of centerless grinding that enhances efficiency, improves workpiece quality, and extends the life of grinding equipment. By understanding the role of coolant and implementing best practices for its use, manufacturers can ensure effective grinding operations while achieving desired precision and surface finish. Investing in the right coolant and its management is essential for achieving excellence in centerless grinding applications.