Understanding Centerless Grinder Wheels Essential Components in Precision Machining
Centerless grinding is a manufacturing process that produces incredibly precise cylindrical components without the need for a spindle. At the heart of this process lies the centerless grinder wheels, which play a crucial role in shaping and finishing workpieces to meet stringent specifications. In this article, we will explore the significance of centerless grinder wheels, their types, applications, and key considerations for selecting the right wheels for your machining needs.
Centerless grinding involves two main wheels the grinding wheel and the regulating wheel. The grinding wheel is responsible for removing material from the workpiece, while the regulating wheel controls the speed and alignment of the component being processed. Together, these wheels ensure a consistent and efficient grinding operation, making them indispensable tools in the precision machining industry.
Types of Centerless Grinder Wheels
There are several types of grinding wheels used in centerless grinding, each designed for specific applications
. The most common types include1. Infeed Wheels Used for complex shapes and components that require precise grinding from various angles. 2. Thru-feed Wheels Ideal for high-volume production where cylindrical parts are fed through the machine. They provide a more straightforward and consistent grinding process.
3. Regulating Wheels These wheels are often softer than the grinding wheels and are designed to slow down the workpiece, ensuring that it is aligned perfectly during the grinding process.
centerless grinder wheels
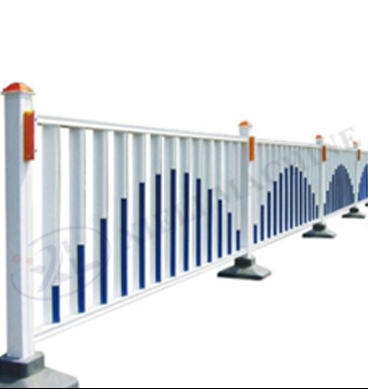
Each type of wheel comes in various materials, including aluminum oxide, silicon carbide, and diamond, each offering different cutting characteristics and performance levels. The choice of material depends on factors such as the type of workpiece, desired finish, and production volume.
Applications of Centerless Grinder Wheels
Centerless grinder wheels find applications across a range of industries, including automotive, aerospace, and medical. They are commonly used for grinding cylindrical parts like shafts, pins, and tubes, which require high precision and consistent surface finishes. In industries such as medical device manufacturing, the accuracy of components is critical, making centerless grinding an ideal choice for producing complex geometries with tight tolerances.
Selecting the Right Centerless Grinder Wheels
Choosing the right centerless grinder wheels involves several considerations. First, you need to identify the material of the workpiece to ensure compatibility with the grinding wheel's material. Secondly, the grit size and wheel structure should match the desired surface finish and removal rate. Lastly, consider the operating speed and settings of your grinding machine, as these factors can influence the performance of the grinding wheel.
In conclusion, centerless grinder wheels are vital for achieving high precision in various machining processes. By understanding their types, applications, and selection criteria, manufacturers can enhance their operational efficiency and product quality. As technology advances, the development of superior grinding wheels will continue to push the boundaries of what is possible in precision manufacturing.