The Advantages of Centerless Grinders Combined with Surface Grinders
In the world of manufacturing and machining, precision is the name of the game. One of the most efficient ways to achieve this level of precision is through the use of grinders, specifically centerless grinders and surface grinders. When these two machines are used in conjunction, they can significantly enhance the production process, providing numerous advantages for manufacturers.
Understanding Centerless Grinders
Centerless grinders are unique machines that allow for the grinding of cylindrical parts without the need for center holes or fixtures. This process is particularly beneficial for high-volume production runs. The key principle behind centerless grinding is that the workpiece is supported by a grinding wheel and a regulating wheel, which allows for a continuous grinding operation without the need for additional setups or handling. This not only speeds up production but also ensures consistent quality and dimensional accuracy.
The Role of Surface Grinders
Surface grinders, on the other hand, are designed for creating a flat or smooth surface on a workpiece. These machines use a grinding wheel to remove material to achieve the desired flatness or surface finish. The precision achieved with surface grinding is crucial for components requiring exact tolerances.
Combining the Two Technologies
Integrating centerless grinders with surface grinders can create a more versatile machining operation. By utilizing both types of grinders, manufacturers can handle a wider variety of machining tasks efficiently. This combination is particularly beneficial for organizations that handle different part geometries or require multiple surface finishes.
centerless grinder with a surface grinder supplier
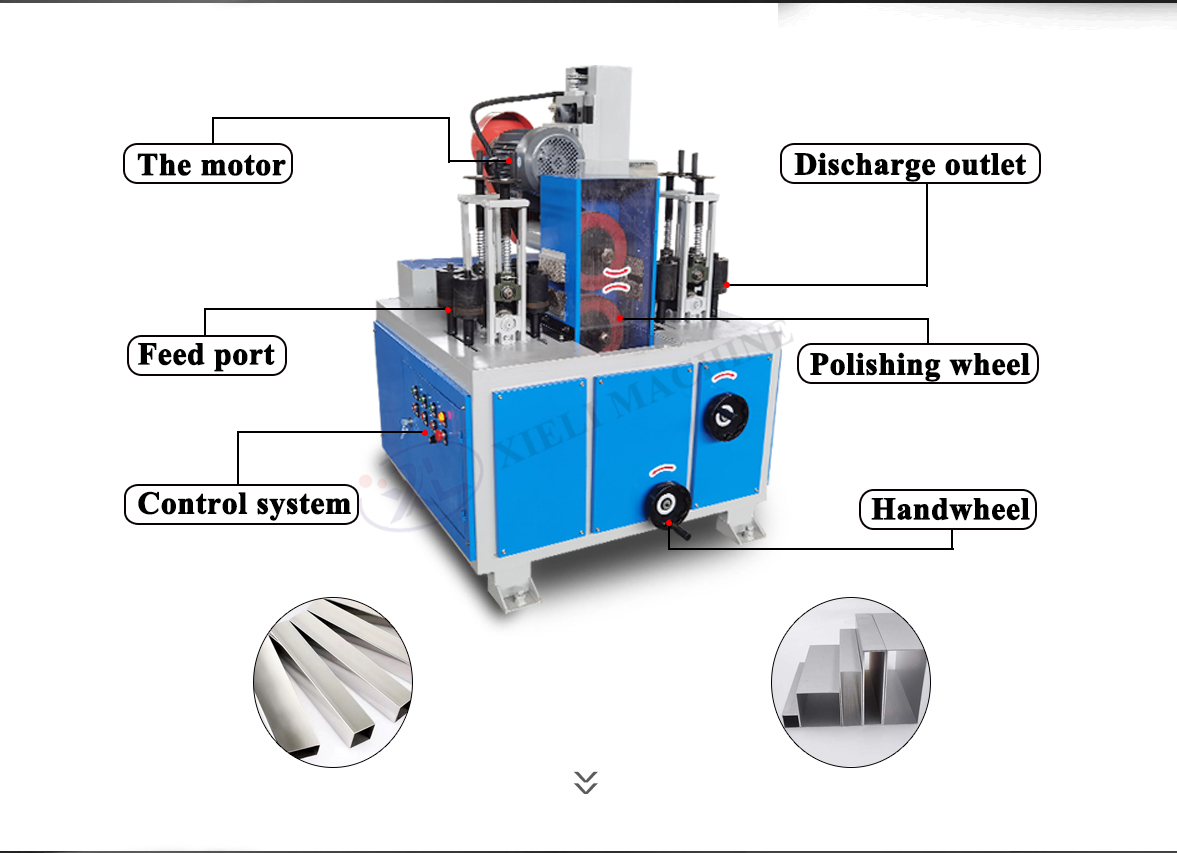
1. Increased Efficiency The combined setup of centerless and surface grinders allows for uninterrupted operations. Parts can be initially processed by a centerless grinder to achieve the necessary cylindrical form, and then routed to a surface grinder to refine the surface finish. This reduces the need for manual handling and setup changes, consequently increasing throughput.
2. Enhanced Precision Using both grinders in tandem ensures that parts not only meet circularity and dimensional tolerances but also have the required surface finish. This dual approach is vital for components that must fit precisely within larger assemblies, where even minor discrepancies can lead to larger operational issues.
3. Cost-Effectiveness Although investing in both a centerless grinder and a surface grinder may appear costly, the long-term savings resulting from increased efficiency and reduced scrap rates can outweigh the initial investment. Higher productivity coupled with minimized downtime results in lower operational costs.
4. Adaptability The flexibility offered by combining centerless and surface grinding capabilities allows manufacturers to respond quickly to market demands. Whether producing a batch of high-tolerance components or transitioning to a different product line, this dual setup can be adapted easily to meet varied manufacturing needs.
Key Considerations for Procurement
When considering the procurement of both centerless and surface grinders, it’s essential to select a reputable supplier. Look for suppliers that not only provide high-quality machinery but also offer comprehensive support and service. This includes advice on machine maintenance, operation training, and availability of replacement parts.
Conclusion
In conclusion, the synergy between centerless grinding and surface grinding technologies can significantly elevate production processes within manufacturing environments. By harnessing the strengths of both types of grinders, organizations can drive efficiency, enhance precision, and improve overall product quality. As manufacturers continue to optimize their operations, investing in this combination proves to be a strategic move worth considering.