Understanding Centerless Grinder Wheels An Essential Tool for Precision Machining
Centerless grinders are crucial machines in the manufacturing industry, especially for producing precision components. At the heart of these machines lie centerless grinder wheels, specialized tools designed to grind workpieces without the need for a central support. This innovative approach has several advantages, including increased productivity, enhanced precision, and improved versatility.
Centerless grinding operates on a simple principle the workpiece is held in place between two wheels – a grinding wheel and a regulating wheel. The grinding wheel removes material from the workpiece, while the regulating wheel controls the speed and position of the piece. This unique setup allows for continuous operation, making it particularly effective for high-volume production.
One of the primary benefits of centerless grinder wheels is their ability to produce highly accurate parts. The continuous engagement of the grinding wheel ensures a consistent finish and dimensional accuracy. This is particularly essential in industries such as automotive, aerospace, and medical, where precision is paramount. By employing dedicated abrasives tailored for specific materials, manufacturers can achieve desired surface finishes and tolerances, elevating the overall quality of the finished product.
Another advantage of centerless grinding is its efficiency in handling differing workpiece sizes and shapes. Unlike traditional grinding methods that require complex setups for varying dimensions, centerless grinding can accommodate a range of workpieces with minimal adjustments. This flexibility reduces downtime and increases productivity, allowing manufacturers to meet tight deadlines without compromising quality.
centerless grinder wheels products
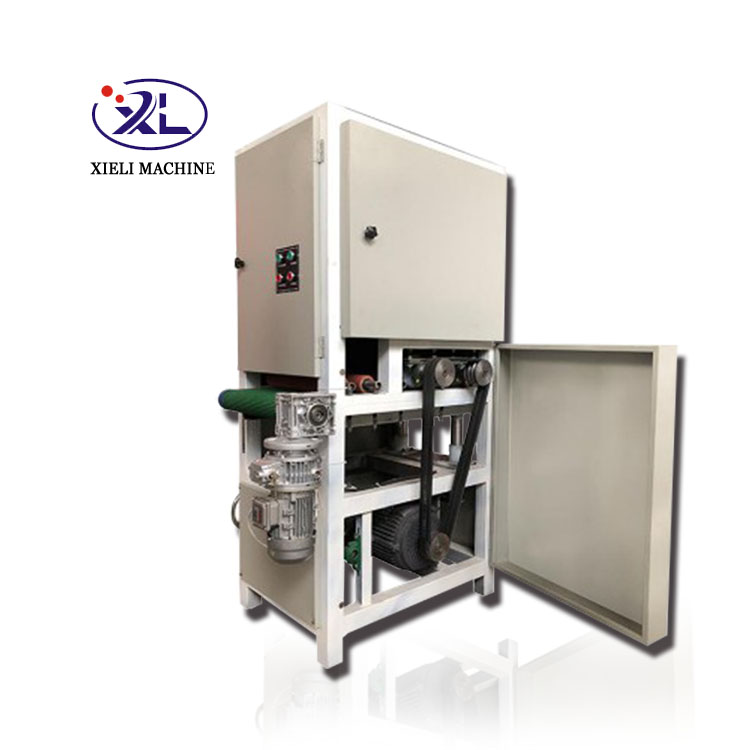
Moreover, the choice of grinding wheels can significantly impact the performance of centerless grinding. Various types of wheels, including aluminum oxide, silicon carbide, and diamond wheels, are available to cater to different applications. The abrasiveness, bonding agent, and structure of the wheel can be customized according to the specific grinding requirements, enabling manufacturers to optimize their processes further.
The maintenance of centerless grinder wheels is also critical for sustained performance. Regular inspection and replacement of worn wheels are necessary to ensure consistent grinding results. Additionally, proper alignment and setup of the machine help in preventing issues such as wheel wear and workpiece damage.
In recent years, advancements in technology have led to the development of more efficient and durable centerless grinder wheels. Innovations such as improved bonding agents and enhanced abrasive materials contribute to longer life spans and better grinding performance. These developments not only benefit manufacturers by lowering operational costs but also lead to increased competitiveness in the market.
In conclusion, centerless grinder wheels play a vital role in the precision machining landscape. Their ability to deliver high accuracy, efficiency, and adaptability makes them indispensable tools in modern manufacturing. As technology continues to evolve, we can anticipate even greater enhancements in the performance and capabilities of these essential abrasive components, further solidifying their importance in industrial applications.