- Introduction to semi automatic polishing machine
s and their growing role in surface finishing industries. - Technological advancements and data-driven performance statistics in semi automatic buffing and surface grinding machines.
- Key technical advantages and main operating principles of semi automatic machines.
- Comparison of leading manufacturers, including a detailed data table on critical features.
- Options for customization to fit specific industrial and customer requirements.
- Real-world applications and successful deployment case studies in various sectors.
- Conclusion: Summary of the impact and future outlook for the semi automatic polishing machine sector.
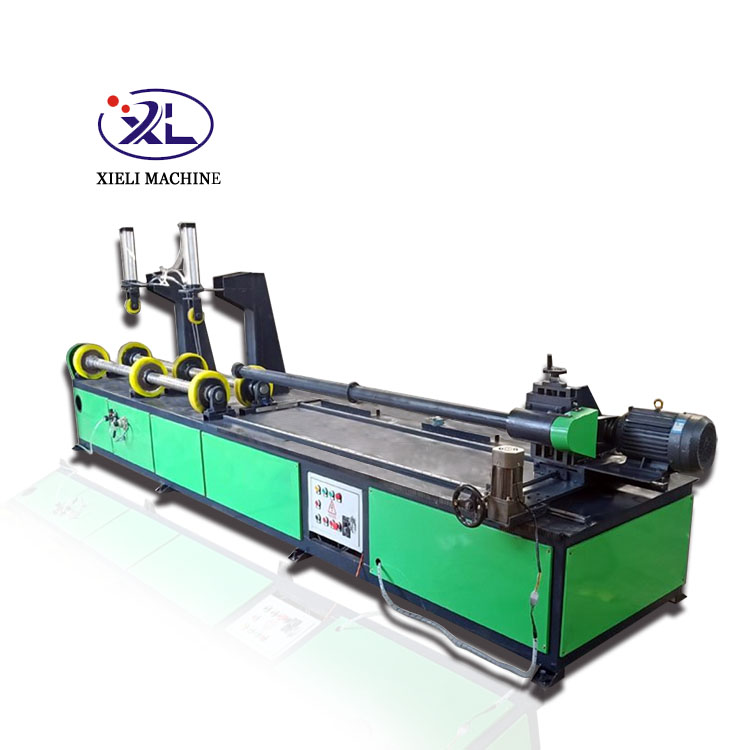
(semi automatic polishing machine)
Introduction: The Impact of Semi Automatic Polishing Machines
Over the past decade, the evolution of manufacturing technology has seen a remarkable surge in the adoption of semi automatic polishing machines. Businesses increasingly seek ways to improve surface finishing processes across diverse industries, from automotive and aerospace to electronics and jewelry. These machines represent a critical pivot from traditional manual methods, offering precision, efficiency, and scalability. As global demand for high-quality surface finishing rises, understanding the nuances of semi automatic polishing technology becomes indispensable for manufacturers looking to stay ahead in their fields.
Technological Advancements and Performance Insights
The shift towards automation in polishing and buffing techniques has transformed standards of product quality and process speed. Utilizing advanced sensors, precise servo motors, and programmable logic controllers, modern semi automatic buffing machines now boast a repeatability margin as low as 0.03 mm. According to a 2023 industry analysis, facilities integrating semi automatic surface grinding machines reported a 40% decrease in cycle time and up to 35% reduction in labor costs. Additionally, these setups enable consistent quality, a significant leap when compared to legacy manual polishing, which typically yields variations of up to 5% in surface roughness ratings (Ra). For businesses focusing on scaling production, these data-driven improvements offer a compelling case for upgrading to semi automatic systems.
Technical Advantages & Operating Principles
The foundation of a semi automatic polishing system is its robust control-module integration. Unlike fully manual tools, these machines allow the operator to set precise parameters such as feed rate, pressure, and polishing compound application. This adjustability helps address distinct material properties—be it stainless steel, aluminum, or advanced composites. The main advantages include enhanced worker safety due to reduced direct contact, minimized material wastage through precise application, and compatibility with a broad array of workpiece shapes and sizes. Moreover, modular configurations allow upgrading individual station functions, extending overall equipment lifecycle by up to 50%. For instance, the introduction of automated slurry delivery and closed-loop feedback systems improves process control, thereby boosting productivity without comprising surface integrity.
Manufacturer Comparison: Market Leaders and Data Table Analysis
Selecting the right semi automatic machine partner is crucial for long-term operational success. Several global manufacturers dominate the current marketplace, each offering unique approaches to automation, integration, and after-sales support. Below is a comprehensive comparison table of leading semi automatic polishing, buffing, and surface grinding machines. Metrics include surface roughness (Ra), throughput, automation grade, and after-sales support level.
Manufacturer | Model | Surface Roughness (Ra, µm) | Max Throughput (units/hr) | Automation Grade | Operating Power (kW) | Warranty (months) | After-Sales Support |
---|---|---|---|---|---|---|---|
Grindex Technologies | GXP-900 | 0.05 | 120 | Semi Automatic | 5.5 | 24 | Global Network |
PoliMAX | PM-14A | 0.07 | 95 | Semi Automatic | 6.2 | 18 | Regional Centers |
BuffMaster | BM-320E | 0.06 | 110 | Semi Automatic | 5.8 | 36 | Onsite/Online |
SurfTech | ST-2000 | 0.08 | 130 | Semi Automatic | 6.0 | 12 | Annual Contracts |
The above data highlights the narrow gap in surface finishing quality achieved by the top models, yet points to differentiation in throughput, warranty, and available support. Businesses with high-output needs may prioritize throughput figures, while those seeking long-term reliability may opt for extended warranty and service agreements.
Customization and Tailored Solutions
Given the diversity of industrial requirements, customization plays a central role in maximizing the value of semi automatic polishing and buffing machines. Manufacturers often offer modular upgrades, such as automatic compound feeders, varied spindle RPM configurations, bespoke fixture holders, and even integration with MES (Manufacturing Execution System) software. For instance, a customer in the aerospace sector may require the ability to polish complex blade geometries with very tight tolerance windows, while electronics manufacturers could seek ultra-low Ra values below 0.02 µm. Adjustable control panels, digital touchscreens, and IoT-enabled monitoring have become standard. Successful customization aligns machine capabilities with specific process steps, material types, and end-product expectations, enabling businesses to unlock operational savings and boost overall equipment effectiveness (OEE).
Application Scenarios and Industrial Success Cases
The utility of semi automatic polishing, buffing, and grinding machines transcends traditional manufacturing boundaries. In the automotive sector, these systems streamline wheel rim, crankshaft, and gearbox polishing processes—delivering consistent mirrored finishes and reducing manual touch-ups by over 60%. In the jewelry industry, intricate works previously reliant on skilled artisans now benefit from semi automatic machines capable of preserving delicate patterns while minimizing human error. A case study from a leading electronics manufacturer showed that post-installation of a semi automatic surface grinding machine, defect rates dropped from 8% to under 1%, and average surface finish improved by 30% based on optical profilometry data. Such results underline the flexibility and impact these machines have in boosting yield, minimizing defects, and ensuring consistent product quality in both low-volume and mass-production environments.
Conclusion: Future Outlook for the Semi Automatic Polishing Machine Industry
The advancement of semi automatic polishing machine technology is paving the way for a new era in surface finishing. As industries strive for tighter tolerances, faster throughput, and enhanced sustainability, integrating semi automatic solutions will become increasingly more critical. Ongoing innovations, such as AI-driven process control and adaptive surface mapping, promise even greater improvements in productivity and resource efficiency. For any organization aiming to optimize its finishing processes, investing in semi automatic buffing or surface grinding machines positions them to meet future challenges head-on—delivering superior quality at scale while maintaining competitive costs.
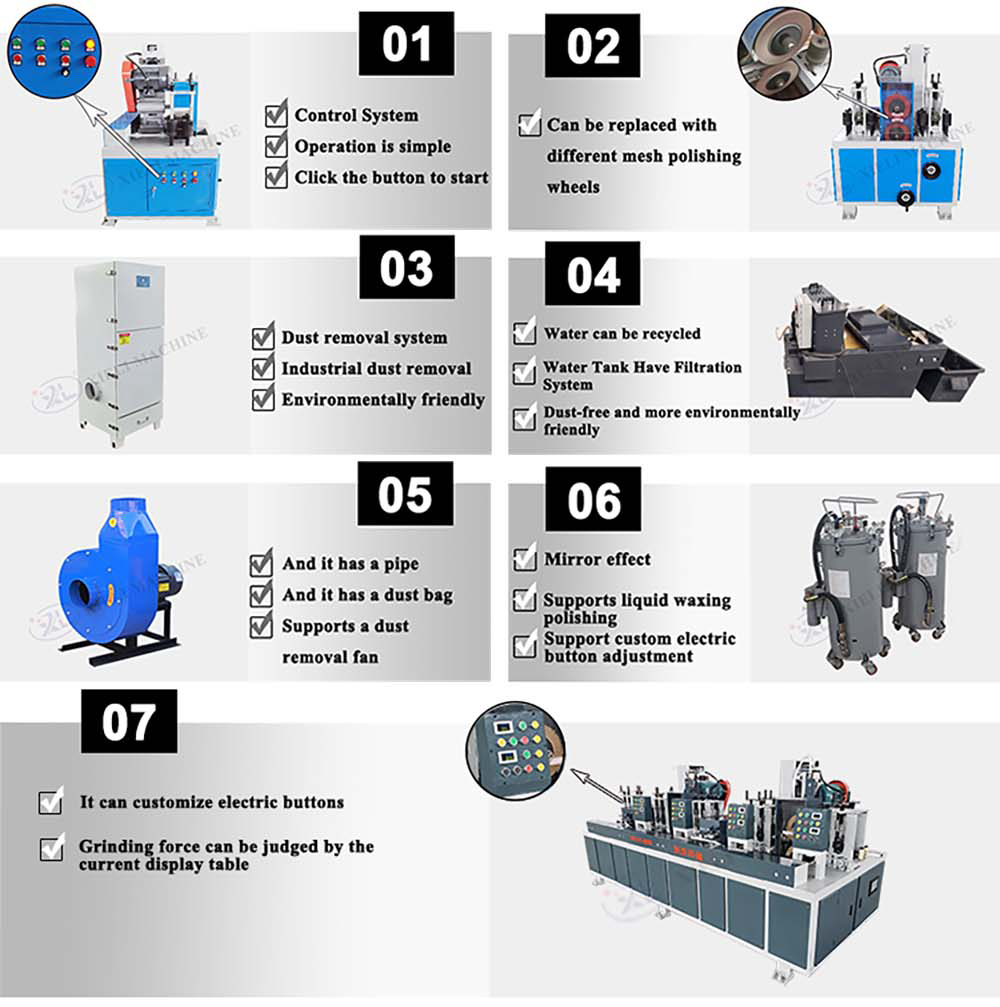
(semi automatic polishing machine)