Understanding Tube Internal Polishing Machines A Comprehensive Overview
In the realm of industrial manufacturing, the pursuit of precision and quality is paramount. One critical aspect of maintaining these standards is ensuring that the internal surfaces of tubes are polished to perfection. This is where tube internal polishing machines come into play. These specialized machines are designed to enhance the finish of tube interiors, improving both aesthetics and functionality. This article delves into the importance of tube internal polishing machines, their features, and their applications in various industries.
The Importance of Internal Polishing
The internal surface of a tube can significantly impact its performance, especially in industries such as automotive, aerospace, and food processing. Rough surfaces can lead to increased friction, reduced flow rates, and the potential for contamination or corrosion. By utilizing tube internal polishing machines, manufacturers can achieve a smoother surface finish, leading to several benefits
1. Improved Fluid Flow Smoother interiors result in reduced turbulence and resistance, enhancing the flow of liquids or gases through the tube. This is particularly crucial in applications such as chemical and pharmaceutical manufacturing, where precise flow rates are essential.
2. Enhanced Corrosion Resistance Polishing removes impurities and irregularities that can lead to corrosion or material degradation. This is vital for tubes used in harsh environments, ensuring longevity and reliability.
3. Aesthetic Appeal For industries where appearance matters, such as architecture or consumer goods, polished tubes can significantly enhance the visual appeal of the final product.
4. Reduced Maintenance Costs By improving the durability and performance of tubes, internal polishing can lead to decreased maintenance and replacement costs over time.
Features of Tube Internal Polishing Machines
Tube internal polishing machines come equipped with a range of features that make them versatile and efficient
- Adjustable Polishing Heads Many machines offer adjustable polishing heads that can accommodate various tube diameters and materials
. This flexibility allows for a wider range of applications, from small precision tubes to larger industrial pipes.tube internal polishing machine quotes
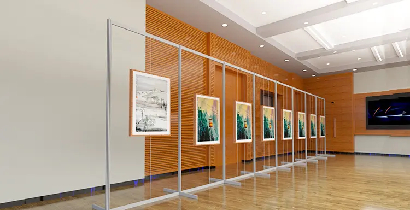
- Automated Processes Advances in technology have led to the development of automated polishing machines that can minimize human error and increase productivity. These machines can monitor polishing progress and adjust parameters in real time, ensuring consistent quality.
- Multiple Polishing Methods Tube internal polishing can be achieved through various methods, including mechanical polishing, chemical polishing, and abrasive blasting. The choice of method often depends on the specific requirements of the application, and many modern machines can switch between techniques.
- Integrated Cleaning Systems Some machines come with built-in cleaning systems that remove debris and contaminants from the tube post-polishing, further enhancing the overall efficiency of the process.
Applications Across Industries
The versatility of tube internal polishing machines makes them suitable for various sectors
- Automotive Industry In automotive manufacturing, polished tubes are essential for fuel lines, exhaust systems, and hydraulic systems, where efficient fluid flow is crucial.
- Aerospace Sector Aerospace applications demand not only lightweight materials but also components that can withstand extreme conditions. Polished tubes can improve performance and safety in aircraft systems.
- Food and Beverage The food industry requires strict hygiene standards. Smooth, polished tubes reduce the likelihood of bacterial buildup, making them easier to clean and maintain.
- Pharmaceuticals and Biotechnology Polished stainless steel tubes are critical in pharmaceutical manufacturing processes, where contamination can jeopardize product integrity.
Conclusion
In summary, tube internal polishing machines are a vital component in various manufacturing processes. They enhance the quality, durability, and performance of tubes across multiple industries. As technology continues to advance, the efficiency and capabilities of these machines will likely improve, offering even greater benefits to manufacturers. Investing in a high-quality tube internal polishing machine is not just about improving the aesthetics of the end product; it’s about ensuring reliability, performance, and ultimately, customer satisfaction. As industries become increasingly competitive, the importance of precision-engineered components cannot be overstated, making the role of these machines indispensable.