The Importance of Tube Internal Polishing Machines in Modern Manufacturing
In the realm of modern manufacturing, precision and quality are paramount. Industries ranging from aerospace to automotive rely on various machinery to ensure that their products meet stringent standards. One such critical piece of equipment is the tube internal polishing machine. This advanced technology plays a vital role in enhancing the internal surface finish of tubes, which can significantly affect both the performance and longevity of the finished product.
What is a Tube Internal Polishing Machine?
A tube internal polishing machine is designed to improve the internal surface of tubular components. It utilizes abrasive media and advanced polishing techniques to remove imperfections, burrs, and other surface irregularities caused by manufacturing processes such as welding, cutting, or machining. The result is a smooth, reflective finish that not only enhances the visual appeal of the tube but also improves its functionality.
Benefits of Using Internal Polishing Machines
1. Enhanced Fluid Flow One of the primary benefits of internal polishing is the improved flow characteristics within the tube. A smooth internal surface reduces turbulence and friction, which can lead to more efficient flow of liquids or gases. This is especially crucial in industries like oil and gas, chemical processing, and food and beverage, where flow dynamics can significantly impact overall efficiency.
2. Corrosion Resistance The polishing process helps to remove contaminants and oxidation layers from the internal surfaces of tubes. A smoother surface is less prone to corrosion, which is vital in environments where tubes are exposed to harsh chemicals or extreme temperatures. By investing in internal polishing, manufacturers can extend the lifespan of their products and reduce maintenance costs.
3. Improved Cleanliness In industries such as pharmaceuticals and food production, hygiene is non-negotiable. Internal polishing machines facilitate a cleaner product by providing surfaces that are easier to clean and less likely to harbor bacteria or contaminants. This is essential for compliance with health and safety regulations and for ensuring the integrity of the final product.
tube internal polishing machine product
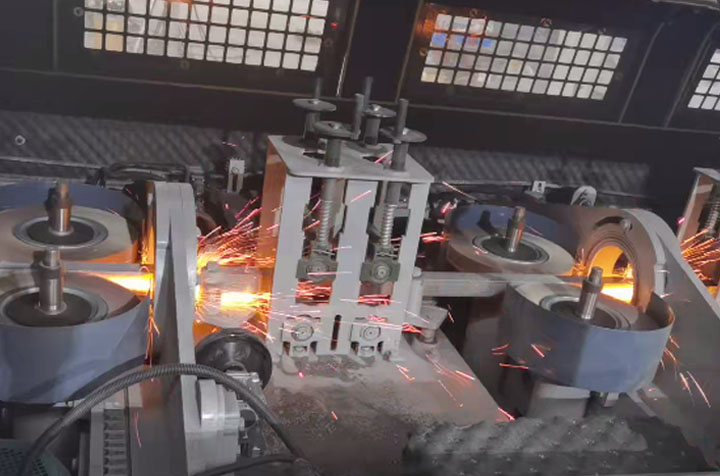
4. Cost Efficiency While the initial investment in a tube internal polishing machine may seem significant, the long-term savings can be substantial. By reducing the incidence of failures due to surface imperfections, manufacturers can decrease warranty claims, improve customer satisfaction, and enhance brand reputation. Furthermore, streamlined production processes can lead to increased throughput and reduced labor costs.
Choosing the Right Tube Internal Polishing Machine
When selecting a tube internal polishing machine, manufacturers must consider several factors to ensure they choose the right equipment for their needs. Key considerations include
- Tube Material Different materials require specific polishing techniques and abrasives. Stainless steel, aluminum, and titanium each have unique properties that affect the polishing process. - Tube Dimensions The size and shape of the tubes being polished can influence machine selection. Some machines are designed for larger, heavy-duty applications, while others are more suitable for small, intricate tubes.
- Production Volume Manufacturers should assess their production needs to determine the appropriate machine capacity. High-volume operations may require automatic polishing systems, while smaller shops may benefit from manual or semi-automatic machines.
Conclusion
In conclusion, tube internal polishing machines are an essential component in modern manufacturing. They not only enhance the appearance of products but also improve functionality, longevity, and compliance with industry standards. As industries continue to evolve, the demand for high-quality, precision-engineered components will only increase. Investing in advanced polishing technology is not just a trend; it is a strategic move towards ensuring product excellence and operational efficiency. By embracing this technology, manufacturers can meet the challenges of the future head-on while maintaining a competitive edge in the marketplace.