The Rise of Tube Internal Polishing Machine Manufacturers
The demand for high-quality metal tubes in various industries has significantly increased over the years. As a result, manufacturers of tube internal polishing machines have become pivotal players in the metal processing field. These specialized machines are designed to enhance the surface finish of metal tubes, ensuring their suitability for numerous applications, including automotive, aerospace, and medical industries.
The Importance of Internal Polishing
Internal polishing of metal tubes is crucial for several reasons. First and foremost, smooth internal surfaces minimize friction and improve the flow of fluids, which is particularly important in applications such as hydraulic lines or any system where the movement of liquids or gases is essential. A polished interior also reduces the risk of corrosion, as it helps eliminate microscopic imperfections where corrosive agents can accumulate. Additionally, in industries such as pharmaceuticals or food processing, maintaining a clean and polished interior is vital for hygiene and compliance with health standards.
Advancements in Technology
The evolution of tube internal polishing machines has been marked by advancements in technology. Modern machines are equipped with various innovative features, including automated controls, real-time monitoring systems, and programmable settings. These enhancements allow manufacturers to customize the polishing process according to the specific requirements of different tube materials and applications.
Moreover, the introduction of CNC (Computer Numerical Control) technology has revolutionized the way tube polishing is executed. CNC machines offer unparalleled precision and efficiency, enabling manufacturers to achieve consistent results with minimal human intervention. This not only increases production rates but also ensures that quality standards are maintained throughout the manufacturing process.
Choosing the Right Manufacturer
tube internal polishing machine manufacturer
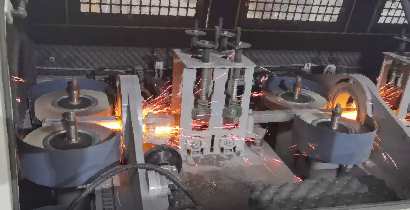
When selecting a tube internal polishing machine manufacturer, several factors should be considered. The manufacturer’s reputation in the industry, the quality of their machines, and the level of after-sales support they provide are all crucial elements. It is advisable to look for manufacturers who have extensive experience and can demonstrate a portfolio of successful projects across various industries.
Another important aspect is the availability of customizable solutions. Different industries have unique requirements, and a one-size-fits-all approach may not always yield the best results. Leading manufacturers often offer tailored solutions that cater to the specific needs of their clients, ensuring optimal performance and efficiency.
Sustainability in Manufacturing
With the growing focus on sustainability, many tube internal polishing machine manufacturers are also incorporating eco-friendly practices into their operations. This includes utilizing energy-efficient technologies, reducing waste during the polishing process, and offering machines that are capable of using biodegradable polishing compounds. Such practices not only benefit the environment but also align with the global push towards sustainable manufacturing methodologies.
Future Outlook
The future of tube internal polishing machine manufacturers appears robust, with numerous opportunities expected to arise. As industries continue to advance and evolve, the demand for high-quality polished tubes will only increase. This is particularly true in sectors such as renewable energy, where the requirement for highly efficient and durable components is paramount.
In conclusion, tube internal polishing machines play an essential role in modern manufacturing processes. The continuous advancements in technology, coupled with a focus on sustainability and customization, position manufacturers in this sector for growth and innovation. As industries push for higher quality and efficiency, the expertise of tube internal polishing machine manufacturers will be more critical than ever in delivering the solutions needed for future advancements. Whether it’s for aerospace components, medical devices, or automotive applications, the role of these specialized machines will undoubtedly continue to be significant in shaping the landscape of manufacturing.