The Evolution of Stainless Steel Plate Polishing Machines A Look into Factories and Innovations
In the ever-evolving world of manufacturing, the importance of surface finishing cannot be understated. Among various materials, stainless steel stands out due to its durability, corrosion resistance, and aesthetic appeal. Consequently, the demand for high-quality stainless steel products has surged, leading to the development of sophisticated stainless steel plate polishing machines. These machines, designed specifically for polishing stainless steel plates, have become essential in factories worldwide.
The primary function of a stainless steel plate polishing machine is to enhance the surface finish of stainless steel plates. This involves removing imperfections, scratches, and oxidization, resulting in a smooth, reflective surface. The polishing process not only improves the visual appeal of the material but also increases its resistance to corrosion and wear, making it suitable for various applications in industries such as construction, automotive, and food processing.
Modern stainless steel plate polishing machines come equipped with advanced technology, allowing for unparalleled efficiency and precision. Most factories leverage automated solutions, where machines are programmed to perform consistent and uniform polishing. This reduces the possibility of human error and increases production speeds, which is crucial in a competitive manufacturing environment. With numerical control (NC) and computer numerical control (CNC) systems, operators can input specific parameters to achieve the desired finish with utmost accuracy.
One distinguishing feature of these machines is their ability to cater to different grades and thicknesses of stainless steel. Factories often produce a wide range of products, from thin plates used in appliances to thicker ones utilized in structural applications. Thus, having a versatile polishing machine that can handle various requirements is a significant advantage. Additionally, manufacturers are continuously innovating, incorporating features such as adjustable speed settings and multiple polishing heads to optimize the polishing process for different types of stainless steel.
stainless steel plate polishing machine factory
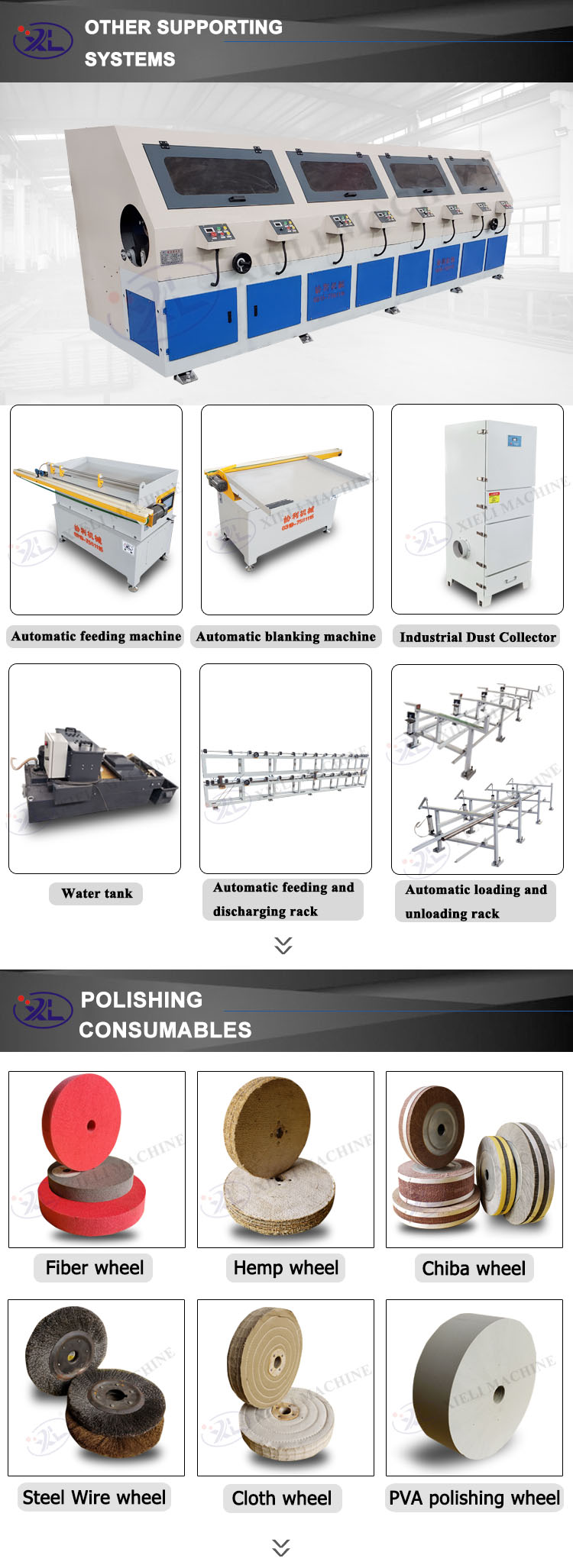
Environmental considerations have also driven innovations in stainless steel plate polishing machines. Factories are now seeking machines that are more energy-efficient and generate less waste. Modern polishing techniques often use water-based compounds instead of solvent-based ones, thus minimizing environmental impact while ensuring effective polishing results. This shift aligns with the global trend towards sustainable manufacturing practices, where reducing the carbon footprint and adhering to environmental regulations is essential.
Moreover, the importance of worker safety in factories cannot be overlooked. Manufacturers are increasingly investing in machines that not only provide high performance but also prioritize safety features. This includes automatic shut-off mechanisms, noise reduction systems, and ergonomic designs that reduce strain on operators. By ensuring a safer working environment, factories can enhance productivity while also complying with occupational safety regulations.
As the demand for polished stainless steel continues to grow, the market for polishing machines is expected to expand. Innovations in technology, coupled with an emphasis on efficiency and sustainability, will shape the future of stainless steel plate polishing. From fully automated systems to machines designed with the environment in mind, the evolution of these tools reflects the broader trends in manufacturing.
In conclusion, stainless steel plate polishing machines play a vital role in the production of high-quality stainless steel products. As factories adapt to changing market demands, the focus on innovative, efficient, and safe polishing solutions will be pivotal. With advancements in technology and a commitment to sustainability, the future of stainless steel plate polishing looks promising, paving the way for better products and practices in the manufacturing industry.