Understanding OEM Tube Polishing Machines Enhancing Surface Quality and Efficiency in Manufacturing
In the manufacturing industry, the demand for high-quality finished products is continuously on the rise. One crucial aspect that contributes to the quality of these products is the surface finish. For manufacturers dealing with metal tubes, an OEM (Original Equipment Manufacturer) tube polishing machine has become an essential tool. This article explores the significance, functionality, and benefits of these machines in the manufacturing sector.
What is an OEM Tube Polishing Machine?
An OEM tube polishing machine is specifically designed for polishing various types of metal tubes, including stainless steel, aluminum, and brass. These machines simplify the process of achieving a fine, mirrored surface finish that enhances the aesthetic appeal of the product and adds to its resistance against corrosion and wear. The technology behind these machines enables manufacturers to standardize their polishing process, ensuring consistency across production batches.
The Importance of Tube Polishing
Surface quality plays a vital role in the performance and durability of metal tubes. Polished tubes not only look more attractive but also provide better resistance to scratches, corrosion, and other environmental factors. In industries such as automotive, aerospace, and plumbing, polished tubes are often preferred due to their ability to withstand harsh conditions and maintain structural integrity over time. Moreover, the smooth surface facilitates easier cleaning and reduces friction, which is particularly beneficial in fluid transport applications.
How OEM Tube Polishing Machines Work
OEM tube polishing machines employ various methods to achieve the desired surface finish. Typically, these machines use abrasives, which may include polishing compounds and brushes, along with mechanical action to remove surface imperfections. The most common types of tube polishing methods include
1. Belt Polishing Using a sanding belt, the machine removes layers from the tube surface, providing an even finish. This method is effective for larger production runs.
2. Brush Polishing This method utilizes rotating brushes that apply polishing compounds to the tube surface, allowing for intricate finishes and the ability to reach hard-to-access areas.
oem tube polishing machine
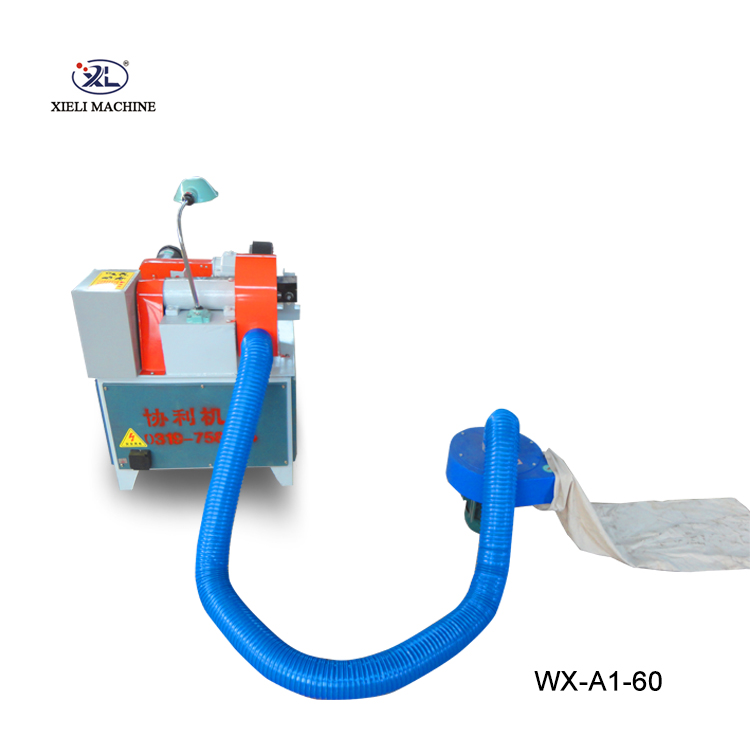
4. Centrifugal Polishing This involves using a rotating bowl that mixes media with the tubes, providing consistent surface finishes while reducing labor costs.
Benefits of Using OEM Tube Polishing Machines
Investing in a dedicated tube polishing machine brings numerous advantages to manufacturers
- Increased Efficiency Automating the polishing process significantly reduces the time required for manual labor, allowing for more refined production schedules.
- Consistent Quality OEM machines ensure that every tube is polished to the same standard, minimizing discrepancies that can arise from manual polishing methods.
- Cost-Effectiveness By reducing labor hours and material waste and increasing production capacity, manufacturers can achieve a better return on investment.
- Customization Many OEM tube polishing machines can be tailored to specific manufacturing needs, accommodating different tube sizes, materials, and target finishes.
Conclusion
The adoption of OEM tube polishing machines signifies a step forward in modern manufacturing processes. As industries strive for superior quality and efficiency, these machines play a critical role in enhancing the surface quality of metal tubes. By delivering consistent, high-quality finishes, manufacturers can ensure their products meet the rigorous standards of today’s competitive market. Investing in this technology not only boosts production capabilities but also your brand's reputation for quality and reliability. As the market continues to evolve, embracing innovative solutions like OEM tube polishing machines will be vital for sustainable growth and success.