Understanding OEM Centerless Grinder Parts
Centerless grinding is an essential machining process used for producing precision parts with a high degree of accuracy. The process involves the grinding of cylindrical workpieces without the need for a workholding device. This unique grinding technique relies on various components that contribute to the overall functionality of the machine. In this article, we will explore OEM (Original Equipment Manufacturer) centerless grinder parts, their importance, and maintenance tips to ensure optimal performance.
The Importance of OEM Parts
When it comes to centerless grinding, using OEM parts is crucial for several reasons. OEM parts are manufactured to the exact specifications of the original equipment, ensuring a perfect fit and optimal performance. Choosing OEM components over generic or aftermarket alternatives can make a significant difference in
1. Quality and Precision OEM parts are designed for specific models and applications, which means they maintain the precision and quality standards of the original machine. Using parts that do not meet these standards can lead to inaccuracies and lower product quality.
2. Reliability OEM parts are tested for longevity and durability. They are built to withstand the rigors of the manufacturing environment, resulting in fewer breakdowns and less downtime.
3. Warranty Protection Many OEM parts come with warranties that guarantee their quality and performance. Using non-OEM parts can potentially void the machine's warranty, putting manufacturers at risk.
4. Easy Integration Since OEM parts are made for specific machines, they integrate seamlessly with existing systems. This saves time during installation and reduces the risk of operational issues that can arise from using incompatible components.
Essential OEM Centerless Grinder Parts
A centerless grinder consists of various parts that work together to achieve the desired finish on workpieces. Here are some essential OEM components that play a significant role in its functionality
1. Grinding Wheels These are the primary cutting tools in the grinding process. OEM grinding wheels are designed for specific materials and applications, ensuring effective material removal and surface finish.
2. Regulating Wheels This part controls the rotation and speed of the workpiece during grinding. OEM regulating wheels provide the necessary balance and stability for precise grinding operations.
oem centerless grinder parts
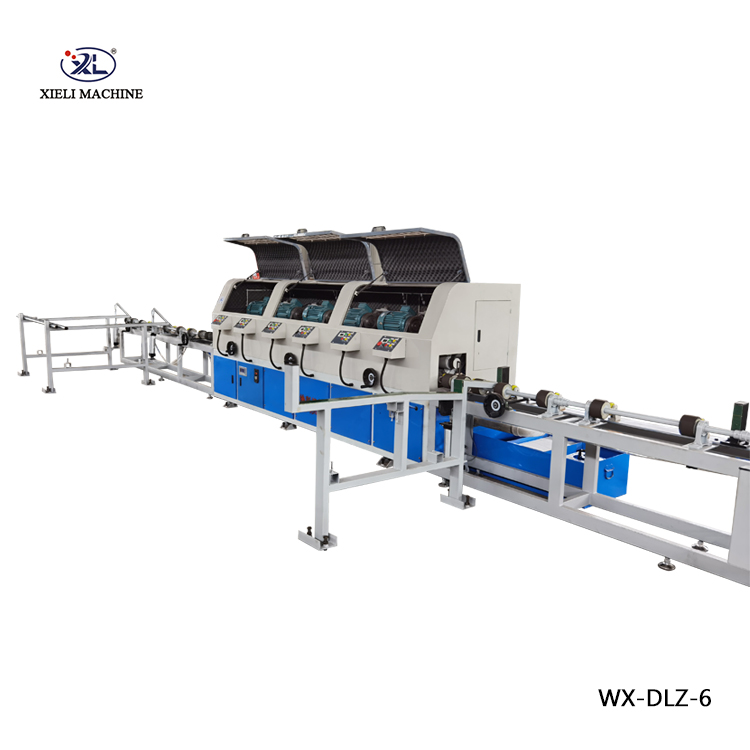
3. Dressers Used to maintain the shape and surface of grinding wheels, OEM dressers are essential for ensuring the grinding wheels perform at their best throughout their lifespan.
4. Work Rest Blades These help support the workpiece during the grinding process. OEM work rest blades are tailored to specific machines and applications to enhance stability and precision.
5. Spindles The spindle holds and drives the grinding and regulating wheels. OEM spindles are designed for optimal performance and durability, vital for maintaining the overall efficiency of the machine.
Maintenance Tips for Centerless Grinders
To ensure the longevity and performance of your centerless grinder, regular maintenance is indispensable. Here are some tips to consider
1. Routine Inspections Regularly inspect all OEM parts for signs of wear and tear. Early detection of issues can prevent significant breakdowns.
2. Proper Lubrication Ensure all moving parts are adequately lubricated. This reduces friction and wear, extending the life of the components.
3. Wheel Dressing Routinely dress grinding wheels to maintain their shape and cutting ability. This is crucial for ensuring consistent part quality.
4. Alignment Checks Keep the grinding and regulating wheels properly aligned. Misalignment can lead to poor grinding results and premature wear on components.
5. Dust and Debris Management Keep the machine clean and free of debris. Dust and particles can affect the movement of parts and degrade performance over time.
Conclusion
In summary, OEM centerless grinder parts play an integral role in the efficiency and precision of the grinding process. Their quality, reliability, and compatibility with the machine make them essential for manufacturers aiming to produce high-quality components. By understanding the significance of these parts and committing to regular maintenance, manufacturers can ensure their centerless grinding machinery operates at peak performance, ultimately leading to improved productivity and profitability.