The Importance of OEM Centerless Grinders in Precision Manufacturing
In the ever-evolving landscape of manufacturing, precision and efficiency are paramount. One of the essential tools in achieving these objectives is the centerless grinder. This article explores the significance of Original Equipment Manufacturer (OEM) centerless grinders, their applications, and the advantages they provide to the manufacturing industry.
Understanding Centerless Grinding
Centerless grinding is a method of removing material from a workpiece without the need for a specific fixture or chucking device. Unlike conventional grinding processes, centerless grinding utilizes two main wheels—the grinding wheel and the regulating wheel—to perform the task effectively. The workpiece is held between these wheels, allowing it to rotate and move linearly through the grinding process. This unique method enables the production of cylindrical parts with high precision and uniformity.
The Role of OEMs in Centerless Grinding
Original Equipment Manufacturers (OEMs) produce machinery, tools, and equipment that meet the specific needs of various industries. When it comes to centerless grinders, OEMs play a crucial role in ensuring that these machines are designed and manufactured with precision, durability, and efficiency in mind. OEM centerless grinders are engineered to perform consistently, providing manufacturers with reliable tools that can withstand the rigors of daily operations.
Applications of OEM Centerless Grinders
OEM centerless grinders are widely used across several industries, including automotive, aerospace, medical devices, and general manufacturing. In these sectors, the demand for precision components is high, and OEM grinders offer the capability to produce parts that meet stringent tolerances. For instance, in the automotive industry, centerless grinding is employed to manufacture various components, including shafts, rods, and valves. The aerospace sector also relies heavily on precision-ground parts for critical aircraft mechanisms, where even the slightest deviation can lead to catastrophic failures.
oem centerless grinder
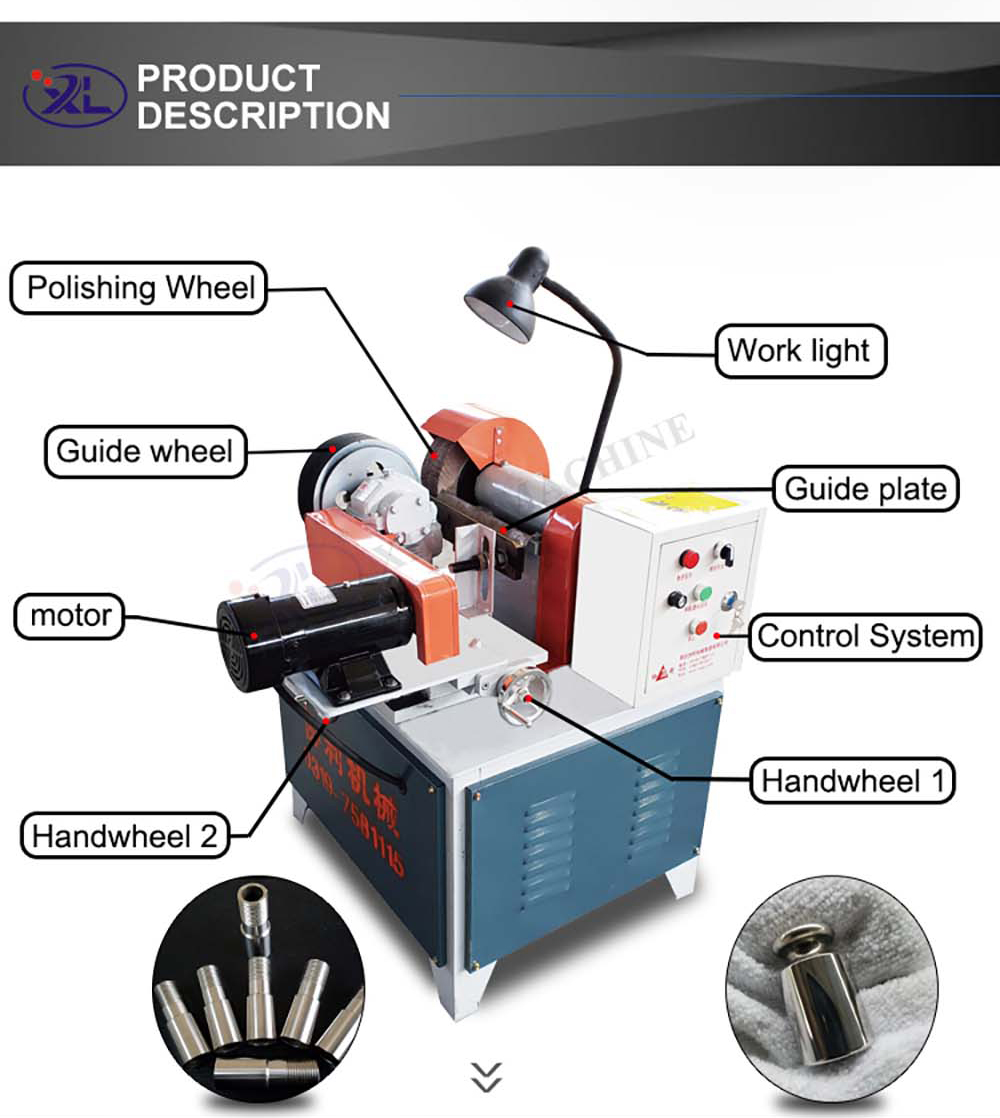
Advantages of Using OEM Centerless Grinders
1. Precision and Accuracy One of the paramount advantages of OEM centerless grinders is their ability to achieve high precision and accuracy. The intricate design and technology used in their manufacture ensure that the final products meet the exact specifications required by clients.
2. Consistency and Repeatability OEM grinders are designed for consistency. Once set up, they can reproduce identical parts with minimal deviation. This repeatability is essential in large-scale production where uniformity is critical.
3. Efficiency and Productivity Centerless grinding is a fast operation that allows for continuous feeding of parts. This leads to increased productivity and reduced cycle times, enabling manufacturers to meet high demand while maintaining quality standards.
4. Versatility OEM centerless grinders can handle various materials and shapes, making them versatile tools for diverse applications. They can be used on hard and soft metals, plastics, and other materials, allowing manufacturers to adapt to changing market needs.
5. Cost-Effectiveness While the initial investment in an OEM centerless grinder may be higher than other grinding methods, the long-term benefits outweigh the costs. The efficiency and reduced waste lead to significant savings in the manufacturing process.
Conclusion
In conclusion, OEM centerless grinders are invaluable assets in the world of precision manufacturing. Their ability to produce high-quality components quickly and efficiently makes them essential for industries where precision is non-negotiable. As manufacturing technologies continue to advance, the role of these grinders will only become more significant. Investing in OEM centerless grinders not only enhances production capabilities but also ensures that manufacturers remain competitive in an increasingly globalized market. By leveraging the advantages offered by OEM grinders, businesses can achieve operational excellence and meet the demands of contemporary manufacturing challenges.