Custom Tube Polishing Machine Manufacturers Elevating Industry Standards
In the ever-evolving world of manufacturing, especially within the metalworking and finishing sectors, the demand for precision and quality has never been higher. A significant component in achieving such standards is the use of advanced machinery, particularly custom tube polishing machines. Manufacturers of these specialized machines play a pivotal role in various industries, including automotive, aerospace, and medical equipment fabrication. This article delves into the world of custom tube polishing machine manufacturers, exploring their significance, technological advancements, and the future of tube polishing solutions.
Understanding Tube Polishing Machines
Tube polishing machines are designed to enhance the surface finish of tubular products made from different materials such as stainless steel, aluminum, and brass. These machines are vital for applications requiring a high degree of aesthetic quality and corrosion resistance. From decorative finishes on handrails to the critical finishes on medical devices, the importance of tube polishing can’t be understated.
The Role of Customization
One of the key trends in the manufacturing sector is the move toward customization. Off-the-shelf solutions often fail to meet the specific needs of individual industries or businesses. Custom tube polishing machines are designed to cater to unique requirements, including different tube sizes, materials, and polishing specifications. Manufacturers often work closely with clients to develop tailored solutions that ensure optimal performance, efficiency, and quality.
This level of customization not only enhances the polishing process but also allows for better integration into existing production lines, minimizing downtime and maximizing productivity. Manufacturers that excel in this area often utilize advanced software and technology to create prototypes and simulations, ensuring that the final product aligns perfectly with client expectations.
Advanced Technologies in Tube Polishing
The evolution of technology in production machinery has led to significant improvements in tube polishing processes. Modern custom tube polishing machines incorporate automated controls, robotics, and high-precision sensors, leading to more consistent finishes and reduced labor costs. These advanced features allow machines to automatically adjust parameters such as speed, pressure, and polishing medium, resulting in enhanced output quality.
custom tube polishing machine manufacturers
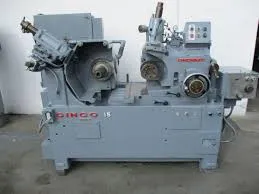
Furthermore, the integration of smart technologies and IoT (Internet of Things) capabilities allows for real-time monitoring and data collection. This data can be invaluable for manufacturers looking to optimize their processes, reduce waste, and predict maintenance needs, ultimately leading to cost savings.
Sustainability Considerations
As the global emphasis on sustainability increases, tube polishing machine manufacturers have also begun to incorporate eco-friendly practices into their designs. This includes the use of non-toxic polishing compounds, energy-efficient motors, and designs that minimize waste production. Additionally, many manufacturers are exploring the use of recycled and sustainable materials for their machines, aligning with the broader industry movement toward sustainability.
Companies that prioritize environmentally friendly practices not only contribute to the global effort to combat climate change but also gain a competitive edge as more clients seek to partner with sustainable businesses.
The Future of Tube Polishing Machines
Looking ahead, the future of custom tube polishing machines appears promising. The continuous rise in demand for high-quality finitions across various sectors indicates that manufacturers will need to innovate consistently. As industries evolve, manufacturers must remain agile, adapting to changing market needs and technological advancements.
Areas for potential growth include the development of machines with enhanced automation capabilities, improved efficiency in the polishing process, and the ability to handle a wider range of materials and finishes. Additionally, with the rise of additive manufacturing, there will be a growing need for polishing solutions that can accommodate 3D-printed components, presenting manufacturers with new opportunities.
Conclusion
Custom tube polishing machine manufacturers are integral to the manufacturing landscape, playing a key role in ensuring that industries achieve the high levels of quality and efficiency required in today's competitive markets. By focusing on customization, adopting advanced technologies, addressing sustainability, and preparing for the future, these manufacturers not only enhance their own offerings but also enable their clients to thrive. As we move into an increasingly sophisticated manufacturing era, the importance of bespoke solutions in tube polishing will continue to grow, shaping the industry for years to come.