The Importance of Quality Parts in Centroless Grinding A Focus on Cinco 2015
In the realm of precision machining, centerless grinding stands out as a technique that enhances productivity while achieving exceptional surface finish quality. At the heart of this process is the equipment itself—a centerless grinder, which relies on a myriad of parts working seamlessly together to deliver optimal performance. This article sheds light on the significance of quality parts in centerless grinders, particularly through the lens of Cinco, a prominent manufacturer known for its commitment to excellence in 2015 and beyond.
Centerless grinding is a type of cylindrical grinding where the workpiece is supported on its outer surface by a work-rest blade. The fundamental components of a centerless grinder include the grinding wheel, regulating wheel, work-rest blade, and various support structures. Each of these parts must be meticulously designed and manufactured to ensure reliable operation and consistent output.
Cinco, as a parts manufacturer, has been at the forefront of innovation in the manufacturing of centerless grinder components. The company harnessed advanced materials and precision engineering techniques in 2015, setting a new standard for durability and performance in the industry. This was particularly important as the demand for high tolerances increased across various sectors, including automotive, aerospace, and medical industries. Each of these sectors requires specific characteristics from the grinding process that only high-quality components can deliver.
One of the critical advancements made by Cinco in 2015 was the development of proprietary grinding wheel materials that improved abrasive performance while reducing wear. This innovation allowed grinders to maintain high efficiency and longer operational life, minimizing downtime for maintenance and replacements. As a result, businesses could achieve higher production rates without sacrificing the quality of their products.
cinco 15 centerless grinder parts manufacturer
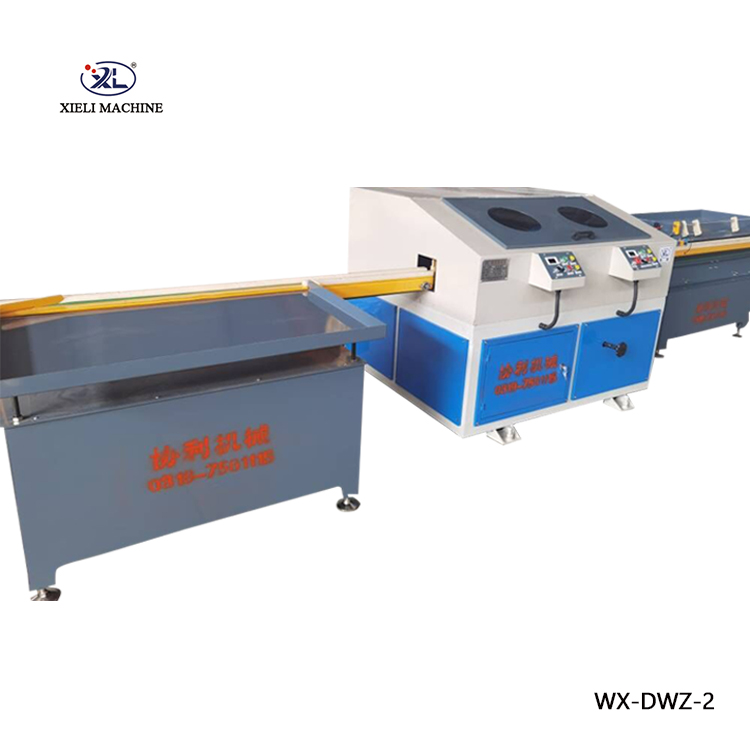
Moreover, Cinco focused on enhancing the regulating wheel design, optimizing its coefficient of friction to ensure that the workpiece is held securely during the grinding process. A well-designed regulating wheel is vital for achieving accurate dimensions and smooth surface finishes. The attention to detail in this component translates into higher precision in the final product, which is essential for industries where every micron counts.
The work-rest blade is another crucial element that has seen significant improvements thanks to Cinco's advancements. The company engineered blades made from wear-resistant materials and incorporated ergonomic designs, providing operators with ease of use while maintaining cutting-edge precision. This integration of form and function reflects Cinco's dedication to understanding the needs of their customers and developing products that not only meet but exceed expectations.
In 2015, Cinco also prioritized sustainability in their manufacturing processes, reducing waste and promoting the use of environmentally friendly materials. This commitment has not only helped the environment but has also attracted a growing market of eco-conscious businesses looking for sustainable machining solutions.
In conclusion, the seamless operation of centerless grinders relies heavily on the quality of their parts. Cinco’s 2015 innovations in component design and material science have established a benchmark in the industry, ensuring that customers receive top-performing machines capable of meeting the demands of modern manufacturing. By investing in quality components from reputable manufacturers like Cinco, businesses can enhance their operational efficiency, product quality, and overall competitiveness in the global market.