Understanding Centerless Grinding Machine Parts
Centerless grinding is a precision machining process that plays a vital role in manufacturing various components used in different industries. The machine operates without a centers or fixtures to hold the workpiece in place, relying instead on the geometry of the grinding operation itself. This article delves into the essential parts of a centerless grinding machine, highlighting their functions and importance.
1. Machine Frame The foundation of any centerless grinding machine is its frame. Generally constructed from robust materials like cast iron or welded steel, the machine frame provides support and stability during the grinding process. Its design is crucial for minimizing vibrations, which can adversely affect precision and surface finish.
2. Grinding Wheel The grinding wheel is one of the most critical components, as it is the tool that removes material from the workpiece. Typically made of abrasive materials, the grinding wheel comes in various sizes and grit options, enabling it to accommodate different materials and desired surface finishes. Proper selection and maintenance of the grinding wheel are essential for achieving optimal performance.
3. Regulating Wheel In a centerless grinding machine, the regulating wheel is crucial for controlling the speed and rotation of the workpiece. This wheel is positioned at an angle against the grinding wheel, enabling it to drive the workpiece forward while also controlling its diameter. The synchrony between the grinding wheel and the regulating wheel ensures efficient material removal and helps maintain dimensional accuracy.
centerless grinding machine parts product
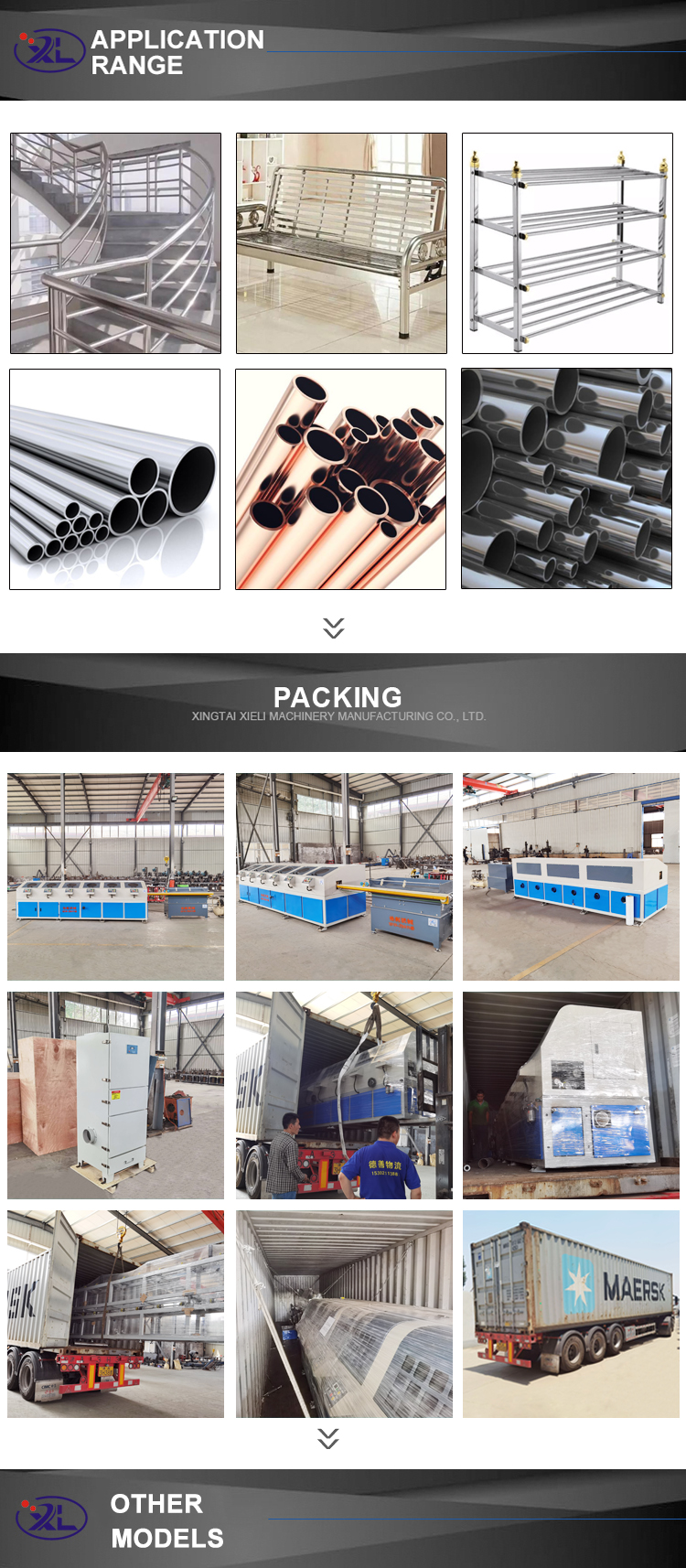
4. Workrest Blade The workrest blade supports the workpiece during grinding, providing stability and helping to maintain the desired height. The workrest blade can be adjusted based on the workpiece's diameter, allowing for versatility in handling various sizes. It's critical that this component is both rigid and accurately positioned to prevent vibrations and deflection.
5. Adjustment Mechanisms Centerless grinding machines often come with various adjustment features that allow operators to change the position of the grinding wheel and regulating wheel. These mechanisms enable precise control over the grinding process, including the depth of cut and the angle of approach. Operators can easily adjust these parameters to achieve the desired specifications for each unique job.
6. Coolant System A well-designed coolant system is vital to the operation of a centerless grinding machine. It serves to cool the grinding area, reducing heat buildup that can alter material properties and lead to premature tool wear. Additionally, the coolant acts as a lubricant, minimizing friction and improving the surface finish of the workpiece.
7. Control Systems Advanced centerless grinding machines often incorporate CNC (Computer Numerical Control) systems that allow for higher precision machining. These systems enable operators to program specific grinding profiles, resulting in consistent production and reduced chances of human error.
Conclusion The parts of a centerless grinding machine work in harmony to achieve efficient and precise material removal. Understanding the function of each component is crucial for operators and engineers alike, as it directly impacts the quality of the final product. With advancements in technology, modern centerless grinding machines continue to evolve, further enhancing their capabilities and efficiency in the manufacturing sector. Proper maintenance and calibration of these machine parts are essential to ensure sustained performance and the longevity of the equipment.