Centerless Grinding Machine Parts Manufacturers An Overview
Centerless grinding is a precise and efficient machining process used to shape intricate parts without the constraints of traditional grinding methods. The technique involves placing the workpiece between two wheels a grinding wheel and a regulating wheel. As the grinding wheel spins at a high speed, the regulating wheel, which rotates at a slower speed, provides the necessary feed and alignment. This innovative method has gained popularity across various industries, including automotive, aerospace, medical, and manufacturing, leading to a burgeoning demand for high-quality centerless grinding machine parts.
Understanding Centerless Grinding Machines
Centerless grinding machines are specifically designed to handle cylindrical components, allowing for the removal of material from the outer diameter of a workpiece. Unlike conventional grinding machines, centerless grinders do not require fixtures or clamps, significantly increasing efficiency. Instead, parts are fed through the machine in a continuous process, which significantly boosts production rates.
These machines utilize a variety of components that are critical for their functioning, including grinding wheels, regulating wheels, work rests, and more. Each component must be manufactured to high precision standards to ensure the machine operates effectively and produces parts with the desired tolerances.
The Role of Manufacturers
Manufacturers of centerless grinding machine parts play a vital role in ensuring the efficiency and reliability of grinding operations. These manufacturers design and produce components that not only meet the operational demands of centerless grinders but also adhere to industry regulations. The quality of these parts directly impacts the overall performance, accuracy, and lifespan of the grinding machines.
A typical centerless grinding machine consists of several key components, including
1. Grinding Wheels These are the primary tools for removing material. Manufacturers must devise wheels from high-quality abrasives to enhance durability and optimize cutting performance.
centerless grinding machine parts manufacturers
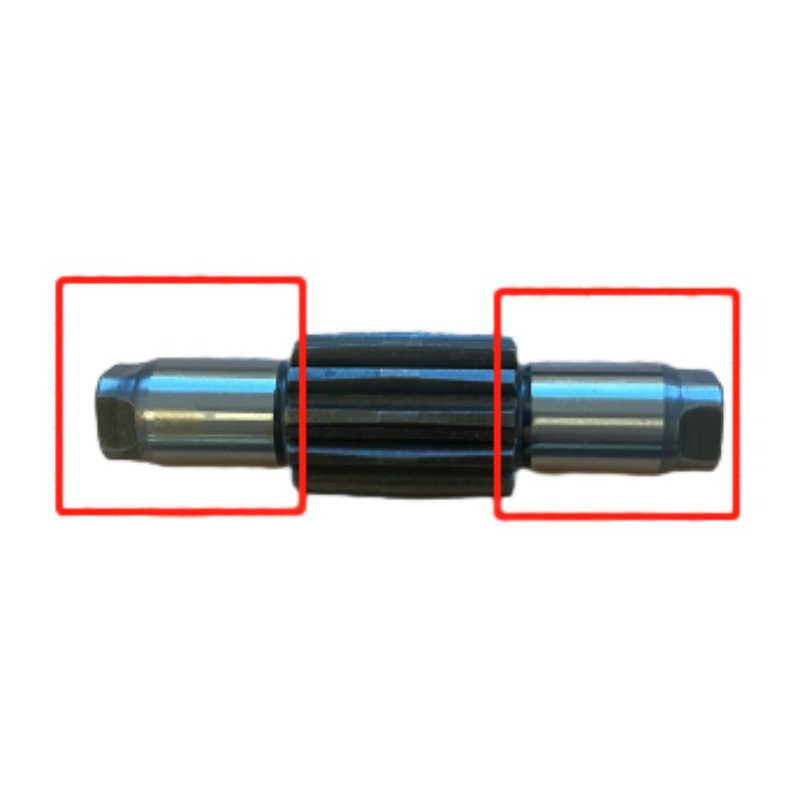
2. Regulating Wheels These help control the speed and movement of the workpiece. The precision of regulating wheels is essential for maintaining tolerances and achieving the desired surface finish.
3. Work Rests These provide support for the part being ground, ensuring stability during the grinding process. The design and material used in work rests must offer both support and resilience.
4. Frame and Base The structure of the machine must be rigid to withstand vibrations and maintain dimensional accuracy during operation. High-quality materials and construction methods are necessary to provide stability.
5. Hydraulic and Control Systems These components manage the operation of the machine, including speed settings and integration with automated feeding systems.
Factors Influencing Manufacturers' Choices
Several factors influence the decisions made by manufacturers in producing centerless grinding machine parts. These include technological advancements, material selections, and customer requirements. With the rapid development of automation and smart manufacturing technologies, manufacturers are increasingly adopting computer-aided design (CAD) and computer numerical control (CNC) machinery to enhance precision and streamline production processes.
Additionally, the demand for customized components has risen, prompting manufacturers to focus on tailor-made solutions that cater to specific customer needs. This has led to increased collaboration between manufacturers and machine operators to better understand the performance demands of various applications.
Conclusion
In conclusion, centerless grinding machine parts manufacturers play a pivotal role in the manufacturing ecosystem. Their ability to produce high-quality, precise components directly affects the performance of centerless grinding machines, which are indispensable in numerous industries. As technology continues to evolve, manufacturers must stay ahead of trends, adapting to changing demands while maintaining high standards in quality and precision. This commitment ensures that centerless grinding remains a vital and efficient machining process for years to come.