The Importance of Centerless Grinder Wheels in Industrial Applications
Centerless grinding is a vital machining process that has gained prominence across various industries due to its ability to produce precise and high-quality components. At the core of this process are centerless grinder wheels, which play an indispensable role in the overall efficiency and effectiveness of the grinding operation. This article explores the significance of these wheels, the companies that manufacture them, and key considerations for selecting the right grinding wheel.
Centerless grinding is particularly advantageous for manufacturing processes that require the production of cylindrical components. Unlike traditional cylindrical grinding, which uses centers to hold the workpiece, centerless grinding maintains the workpiece in place through a combination of gravitational and frictional forces. This eliminates the need for fixtures and allows for the processing of multiple parts simultaneously, significantly increasing productivity.
The Importance of Centerless Grinder Wheels in Industrial Applications
Several companies specialize in manufacturing centerless grinder wheels, providing a diverse range of products to cater to different industrial needs. Leading manufacturers include Norton Abrasives, 3M, MAJOR, and Radiac Abrasives. These companies have established themselves as reliable suppliers with a track record of innovation and quality. They invest heavily in research and development to create wheels that meet the evolving demands of the manufacturing sector.
centerless grinder wheels companies
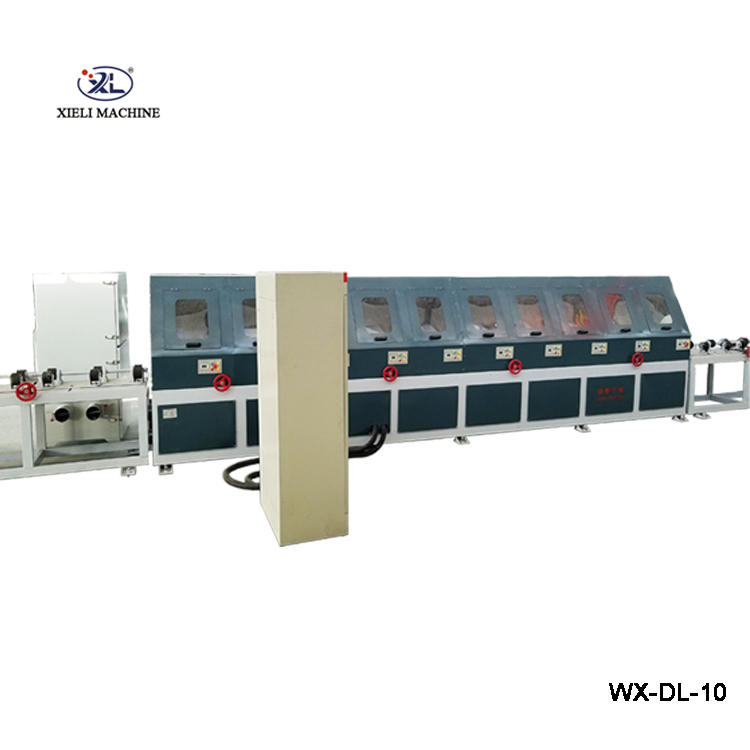
Norton Abrasives, a division of Saint-Gobain, is renowned for its high-performance grinding wheels that enhance productivity and reduce downtime. Their centerless grinding wheels offer exceptional durability and consistency, making them the preferred choice for many manufacturing plants. 3M, another industry giant, leverages its extensive experience in abrasive materials to provide innovative grinding solutions that improve efficiency and surface finishes.
In addition to established manufacturers, numerous smaller companies also contribute to the market by offering specialized options tailored to niche applications. These companies often focus on customized solutions, providing expertise and flexibility that larger firms may not offer. This diverse landscape ensures that manufacturers can find the right wheel for their specific grinding needs, irrespective of the scale of operation.
When choosing the appropriate centerless grinding wheel, several factors must be considered. First, the material of the wheel should match the workpiece material to ensure optimal grinding efficiency and longevity. Second, the grit size plays a crucial role in achieving the desired surface finish; finer grits produce smoother finishes, while coarser grits are more effective for material removal. Finally, the bond type—whether vitrified, resin, or metal—affects the grinding characteristics and durability of the wheel.
In conclusion, centerless grinder wheels are a fundamental component in the machining industry, driving efficiency and precision in the production of cylindrical parts. The landscape of manufacturers, ranging from industry leaders like Norton and 3M to specialized firms, offers a wide array of options for industries looking to enhance their grinding operations. By carefully considering the material, grit, and bond type, manufacturers can select the optimal centerless grinding wheel to meet their specific requirements, ensuring high-quality outputs in a competitive marketplace.