Understanding Centerless Grinder Training for Manufacturers
Centerless grinding is a pivotal process in modern manufacturing, enabling precision machining of components without the need for a fixed spindle. This technique is particularly advantageous for producing cylindrical parts that require a high level of accuracy and consistency. For manufacturers, ensuring that operators are proficient in centerless grinding is critical for maintaining quality and operational efficiency. Therefore, centerless grinder training has become an essential aspect of workforce development.
The Importance of Centerless Grinder Training
Effective training programs for centerless grinders cover a variety of essential aspects, including machine operation, troubleshooting, maintenance, and safety protocols. With the rapid advancement in grinding technology and the introduction of automated systems, the need for comprehensive training is greater than ever. A well-trained workforce can significantly enhance productivity and reduce downtime caused by improper machine handling or maintenance procedures.
Key Components of Training Programs
1. Machine Operation and Setup Operators should receive detailed training on how to set up centerless grinding machines. This includes understanding the grinding wheel specifications, alignment of workpieces, and adjusting the infeed and regulating speeds. Proper setup is critical to achieving optimal grinding parameters and ensuring the desired surface finish.
2. Understanding Grinding Principles Knowledge of the fundamental principles of grinding, including the mechanics of material removal and the types of grinding wheels available, is essential. Training should cover topics such as the grinding cycle, the effects of wheel speed, feed rate, and the influence of coolant in the grinding process.
centerless grinder training manufacturers
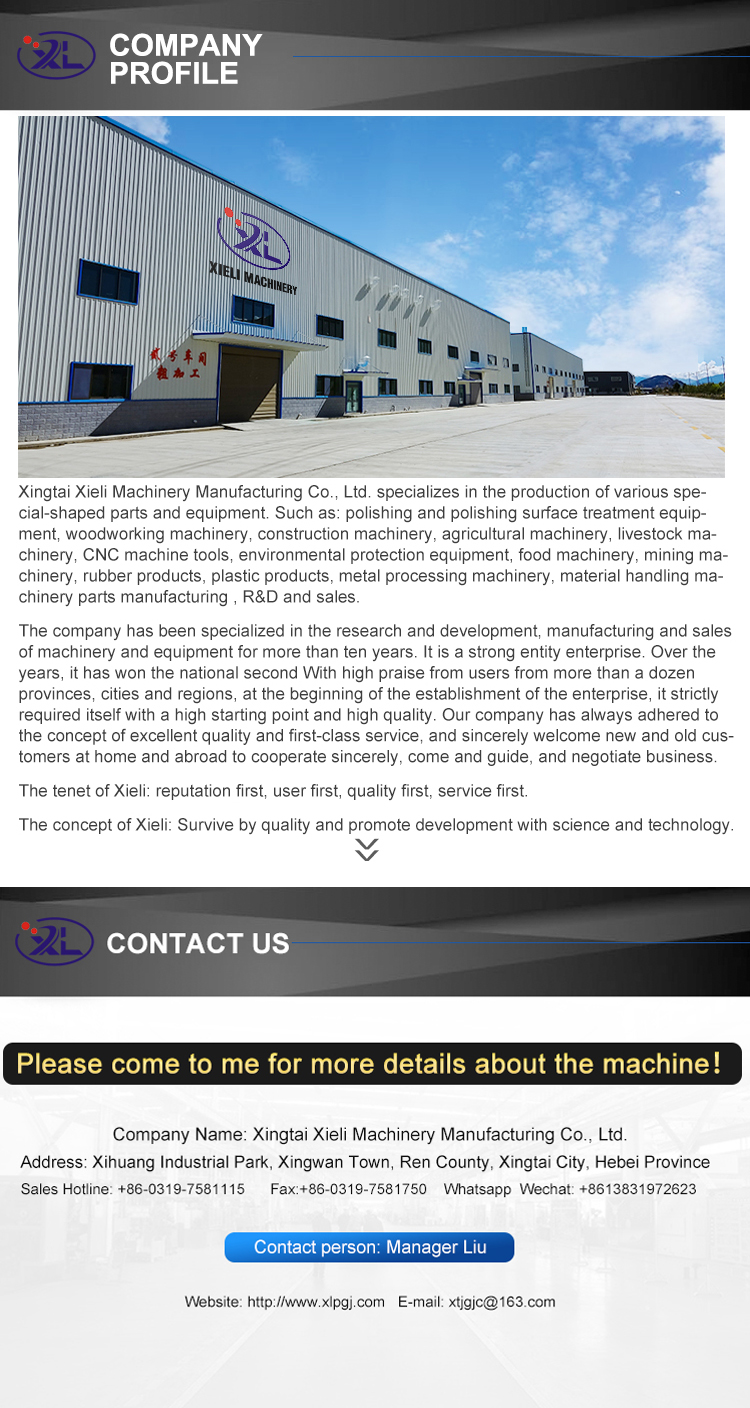
3. Troubleshooting Techniques Operators must be equipped with the skills to identify and resolve common issues that arise during grinding operations. This segment of training should teach participants how to diagnose problems, such as excessive wear on grinding wheels, misalignment of workpieces, or finish defects, and how to implement solutions effectively.
4. Maintenance Practices Regular maintenance and calibration of grinding machines are crucial for long-term performance. Training should emphasize the importance of routine inspections, changing the coolant, and maintaining grinding wheels. Operators should also learn to perform basic troubleshooting and maintenance tasks to minimize operational disruptions.
5. Safety Protocols Safety should always be a primary focus in any training program. Operators need to be trained in safe working practices, proper use of personal protective equipment (PPE), and emergency response procedures. Understanding the potential hazards associated with centerless grinding machines helps ensure a safe working environment.
The Role of Manufacturers in Training
Manufacturers should take a proactive approach to developing training programs tailored to their specific needs. Collaborating with industry experts and training organizations can enhance the quality of the training offered. Involving experienced operators in mentorship roles can also foster a culture of continuous learning and improvement within the workforce.
In conclusion, centerless grinder training is not just a formality; it is a strategic investment in a manufacturer’s operational success. By equipping operators with the necessary skills and knowledge, companies can improve product quality, enhance efficiency, and maintain a competitive edge in the manufacturing industry. As technology continues to evolve, ongoing training will be essential to adapt to new techniques and innovations in the grinding sector.