The Importance of Rebuilding Centerless Grinders
Centerless grinders are essential machine tools used in precision manufacturing processes to grind cylindrical workpieces without needing to center them. Unlike traditional grinding methods, centerless grinding allows for high productivity and efficiency. However, over time, these machines can wear down due to regular use, leading to decreased performance and accuracy. That's where the concept of rebuilding comes into play—a crucial process that restores these machines to their optimal operating conditions through refurbishing and upgrading.
What is a Centerless Grinder Rebuild?
A rebuild of a centerless grinder involves a comprehensive evaluation and refurbishment of various components of the machine. This typically includes the grinding wheels, spindles, bearings, and even the machine's structural elements. Depending on the specific condition and age of the grinder, the rebuilding process can vary significantly in scope and cost.
Rebuilding not only involves replacing worn-out parts but also upgrading systems to enhance performance, such as incorporating modern controls or better cooling systems. The goal is to extend the machine's lifespan, improve its efficiency, and maintain its precision capabilities.
Why Rebuild Instead of Replace?
Choosing to rebuild a centerless grinder rather than replacing it outright can have significant advantages. First, rebuilding can be a more cost-effective solution. Purchasing a new grinder can be a substantial financial investment, often running into the tens or hundreds of thousands of dollars. In contrast, a rebuild can significantly lower this expense while providing many of the same benefits as a new machine.
Additionally, rebuilding allows manufacturers to retain their existing machines, which may have been customized or integrate seamlessly with other systems in place. This minimizes downtime associated with training personnel on new equipment or recalibrating other connected systems.
Factors to Consider in a Rebuild
centerless grinder rebuild quotes
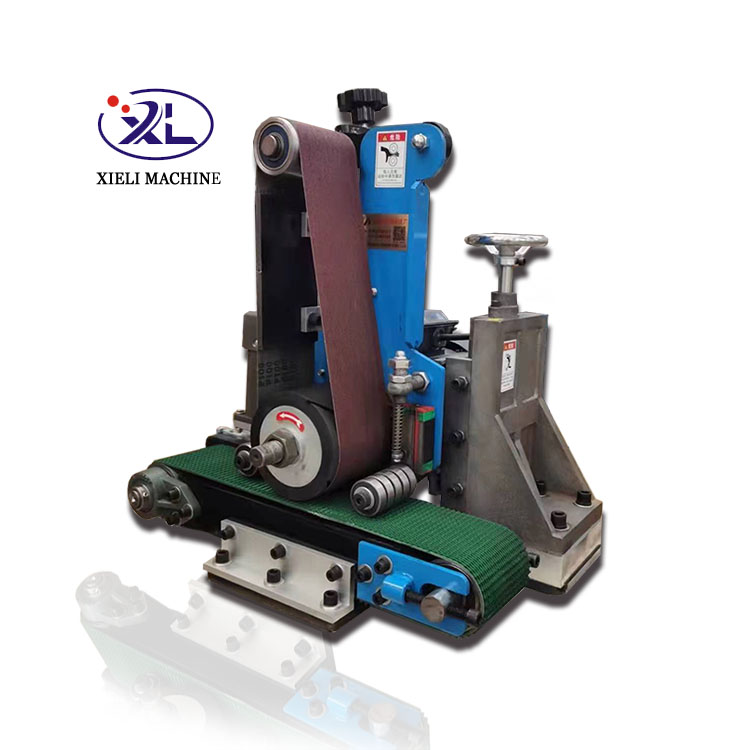
When considering a rebuild for a centerless grinder, several key factors should be taken into account
1. Machine Condition Assess the extent of wear and damage to the machine. Components like spindles and wheels often wear out first, but the structural integrity of the machine must also be evaluated.
2. Replacement Parts and Upgrades Identify which parts need to be replaced and what upgrades could enhance productivity. Modern technologies can often be integrated into older models, making them more competitive.
3. Cost and Budget Prepare a budget for the rebuild process. This should encompass not only parts but also labor and potential downtime costs.
4. Vendor Experience Choose a reputable service provider with experience in rebuilding centerless grinders. Their expertise can significantly impact the quality and reliability of the rebuild.
5. Downtime Consider the time required for the rebuild and how it will affect production schedules. Planning the rebuild process strategically can mitigate the impact on workflows.
Conclusion
Centerless grinder rebuilds present an excellent opportunity for manufacturers to enhance their operations without the hefty price tag of new machinery. By evaluating the condition of a machine and making strategic replacements and upgrades, businesses can extend the life of their equipment while improving efficiency and maintaining precision. As manufacturing continues to evolve, the flexibility and adaptability offered by a well-executed rebuild will keep companies competitive in a rapidly changing landscape. Whether it’s for cost savings, performance improvements, or the desire to retain an essential piece of machinery, considering a rebuild is a viable option worth exploring.