Reviving Precision The Role of Centerless Grinder Rebuilders
In the world of manufacturing, precision is paramount. One tool that has consistently proven essential in achieving high levels of accuracy is the centerless grinder. Used for precision grinding of rotating parts, centerless grinders offer unique advantages, such as continuous workpiece production without the need for chucking or centering. However, like any mechanical device, they require regular maintenance and occasional refurbishing. This is where centerless grinder rebuilders come into play, breathing new life into aging machinery and ensuring consistent production standards.
Understanding Centerless Grinding
Before delving into the importance of rebuilders, it’s essential to grasp the principles of centerless grinding. Unlike conventional grinding machines, which support the workpiece at its center, centerless grinders employ a different approach. The workpiece is placed between two rotational wheels the grinding wheel and the regulating wheel. This arrangement allows for the continuous feed of material, producing large volumes of precision parts in a compact space.
The key advantages of centerless grinding include the ability to handle complex shapes and maintain tight tolerances, making it an indispensable choice for industries such as automotive, aerospace, and tooling. However, with continual use, these machines can experience wear and tear, leading to decreased performance and precision—highlighting the need for timely rebuilding services.
The Importance of Rebuilding
Rebuilding a centerless grinder involves comprehensive restoration processes aimed at extending the machine's lifespan and improving its efficiency. When a centerless grinder is rebuilt, it typically undergoes several critical procedures
1. Disassembly and Inspection The machine is taken apart, and each component is inspected for wear and defects. This step ensures that any underlying issues are identified early and addressed.
2. Replacement of Worn Parts Components such as bearings, spindles, and wheels that show signs of wear are replaced with high-quality replacements. This not only restores functionality but also enhances the precision of the machine.
3. Alignment and Calibration Ensuring correct alignment is crucial in a centerless grinder. After rebuilding, machines are meticulously calibrated to meet precise specifications, ensuring they produce accurate parts on par with new machines.
centerless grinder rebuilders product
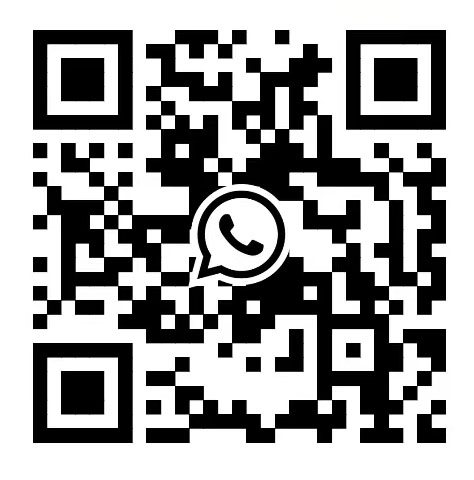
4. Upgrading Components Many rebuilders offer the option to upgrade certain machine components with more advanced technologies, such as improved cooling systems or electronic controls, which can lead to enhanced performance and energy efficiency.
5. Final Testing and Certification Once rebuilt, the machine undergoes rigorous testing to verify its operational capabilities. A reliable rebuilder will often provide certification, giving users peace of mind regarding the machine’s performance.
Benefits of Choosing a Centerless Grinder Rebuilder
Engaging with a professional centerless grinder rebuilder offers multiple benefits for businesses
- Cost Efficiency Rebuilding is generally more cost-effective than purchasing a new machine, allowing businesses to save money while maintaining productivity.
- Minimized Downtime Rebuilders often have the expertise and resources to complete refurbishments in a timely manner, minimizing downtime and keeping production lines running smoothly.
- Sustainability By refurbishing existing machinery, companies contribute to sustainability efforts, reducing waste and the need for new materials.
- Expert Support Rebuilding services often include ongoing support and maintenance options, helping businesses maintain machine performance long after the rebuild process.
Conclusion
In an era where precision and efficiency are critical for success in manufacturing, centerless grinder rebuilders play an invaluable role in restoring and enhancing operations. By investing in expert rebuilding services, businesses can ensure their machinery remains at the forefront of technology and performance, safeguarding their ability to deliver quality products consistently. Ultimately, choosing to rebuild rather than replace can lead to significant savings, improved productivity, and a reinvigorated commitment to excellence in manufacturing processes. Embracing these services not only preserves existing resources but also fosters a culture of innovation and efficiency in the manufacturing landscape.