Understanding Centerless Grinder Parts
Centerless grinding is a manufacturing process used to produce precise cylindrical parts without the need for a fixed center. This method offers numerous advantages, including high productivity, versatility, and the capability to handle long workpieces. Essential to the efficiency and accuracy of a centerless grinder are its various parts, which work together to ensure smooth operation and high-quality output.
Key Components of a Centerless Grinder
1. Grinding Wheels At the heart of the centerless grinding process are the grinding wheels. The setup typically includes two wheels the grinding wheel and the regulating wheel. The grinding wheel removes material from the workpiece, while the regulating wheel controls the speed and position of the workpiece. The choice of wheel materials, grits, and sizes plays a crucial role in achieving the desired finish and tolerances.
2. Work Rest Support This component supports the workpiece during the grinding operation. The work rest should be adjustable to accommodate different workpiece lengths and diameters. Its design helps maintain the workpiece in a stable position, preventing it from tilting or moving during the grinding process.
3. Regulating Wheel The regulating wheel not only controls the feed rate of the workpiece but also influences the surface finish and part geometry. The wheel's angle and speed can be adjusted, impacting the cutting action and ensuring that the part is ground evenly and precisely.
centerless grinder parts
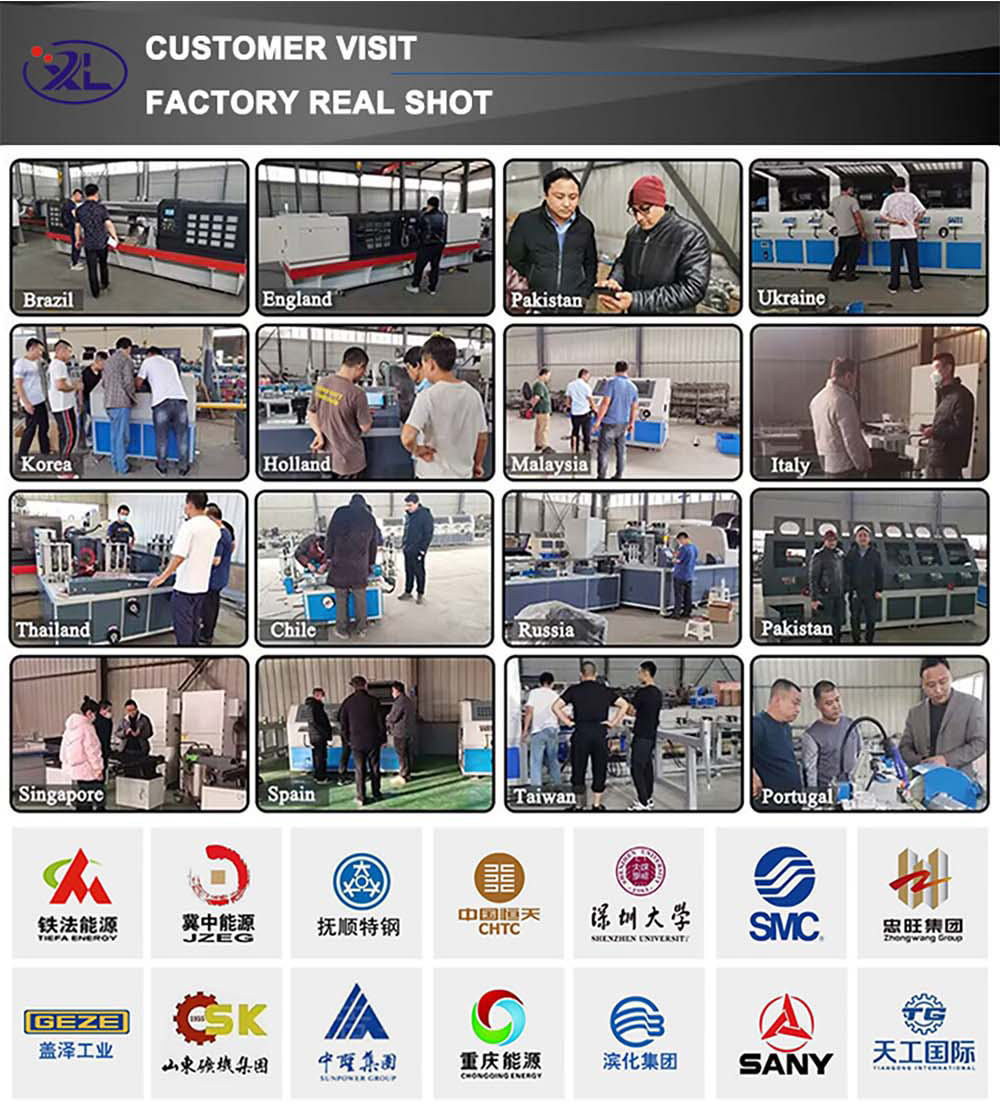
4. Drive Mechanism The drive mechanism powers both the grinding and regulating wheels. This system is crucial for maintaining consistent speeds and feeds, and it may include electric motors, belts, pulleys, and gear systems. A well-functioning drive mechanism ensures efficient operation and optimal performance.
5. Workpiece Support System This system includes various fixtures and setups tailored to secure the workpiece during grinding. Depending on the specific application and design of the grinder, support mechanisms can vary greatly, ensuring that parts are held firmly and accurately in place throughout the grinding process.
6. Cooling System Heat generation during the grinding process can lead to thermal deformation of the workpiece and grinding wheels. A proper cooling system, often integrated with coolant delivery systems, helps maintain optimal temperatures, extends the life of the grinding wheels, and ensures consistent machining results.
7. Control Panel Modern centerless grinders come equipped with advanced control systems, allowing operators to monitor and adjust parameters such as speed, feed rate, and wheel wear. This interface is crucial for achieving precision and adapting to varying operational demands.
Conclusion
In essence, the components of a centerless grinder are intricately designed to work in harmony, resulting in efficient and precise grinding operations. Each part, from the grinding wheels to the cooling systems, plays a vital role in the overall effectiveness of the machine. Understanding these components helps operators maintain equipment, troubleshoot issues, and optimize production processes, ultimately enhancing the quality and uniformity of the manufactured parts. As industries continue to evolve, the role of centerless grinding remains critical, showcasing its indispensable contribution to modern manufacturing.