The Benefits of Rebuilding Centerless Grinders
In the manufacturing industry, precision and efficiency are paramount. Centerless grinders play a significant role in achieving high-precision surface finishes and maintaining tight tolerances for various metal components. However, over time, these machines may suffer from wear and tear, leading to reduced performance. That’s where rebuilding comes into play.
The Benefits of Rebuilding Centerless Grinders
Moreover, a rebuilt centerless grinder can offer improved accuracy and precision. During the rebuild process, skilled technicians can recalibrate critical elements such as the grinding wheel and regulating wheel to ensure they meet exact specifications. This meticulous attention to detail can yield better surface finishes and tighter tolerances, essential for industries such as automotive, aerospace, and medical manufacturing.
buy centerless grinder rebuild
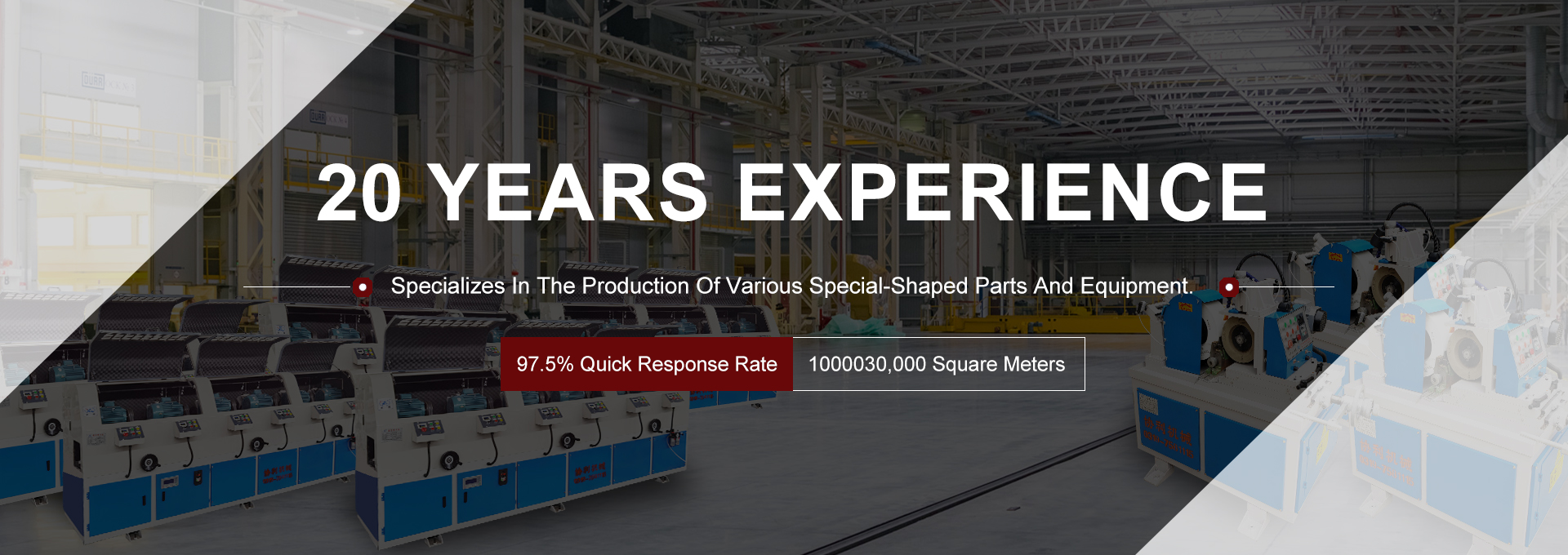
Another key benefit of rebuilding is the opportunity to upgrade. Older models may lack the advanced technology and features of newer machines. By investing in a rebuild, companies can incorporate modern advancements, such as enhanced automation capabilities and improved safety features, ultimately leading to increased productivity.
Additionally, rebuilding promotes sustainability. By repairing and refurbishing existing equipment rather than replacing it, companies can minimize waste and reduce their environmental impact. This approach aligns with the growing emphasis on sustainability within the manufacturing sector.
In conclusion, rebuilding a centerless grinder is a strategic decision that can yield significant benefits. It not only saves costs but also enhances performance and accuracy while promoting sustainability. Manufacturers looking to maintain a competitive edge should consider rebuilding their centerless grinders as an effective way to ensure long-term productivity and efficiency. Investing in rebuilding is not just about keeping machines operational—it's about optimizing them for the future.