The Importance of Buying Centerless Grinder Blades
In the world of precision machining, centerless grinders are essential tools for achieving tight tolerances and surface finishes on cylindrical workpieces. These machines operate without the need for a conventional spindle, allowing for continuous production of high-quality components. A crucial aspect of maintaining the performance of a centerless grinder is the selection and purchase of the appropriate grinding blades. This article will explore the importance of buying the right centerless grinder blades and the factors to consider during the purchasing process.
Understanding Centerless Grinding
Before delving into the specifics of grinder blades, it's crucial to understand the mechanics of centerless grinding. The process involves placing a workpiece between two wheels the grinding wheel and the regulating wheel. The grinding wheel does the cutting, while the regulating wheel controls the workpiece's speed and its position. This configuration allows for various types of materials to be ground into precise dimensions quickly and consistently.
The Role of Grinding Blades
The grinding blades, or wheels, are the heart of the centerless grinding process. They determine the efficiency, precision, and quality of the finished product. Choosing the right blades is critical because improper or low-quality blades can lead to several issues, including
- Reduced Efficiency Dull blades may slow down the grinding process, requiring more frequent replacements and maintenance. - Increased Heat Generation Poorly matched blades can generate excess heat, leading to thermal damage to both the workpiece and the grinding machine. - Poor Surface Finish The end quality of the machined part largely depends on the sharpness and composition of the grinding blades.
Factors to Consider When Buying Centerless Grinder Blades
When purchasing centerless grinder blades, several factors should be taken into account to ensure optimal performance
buy centerless grinder blades
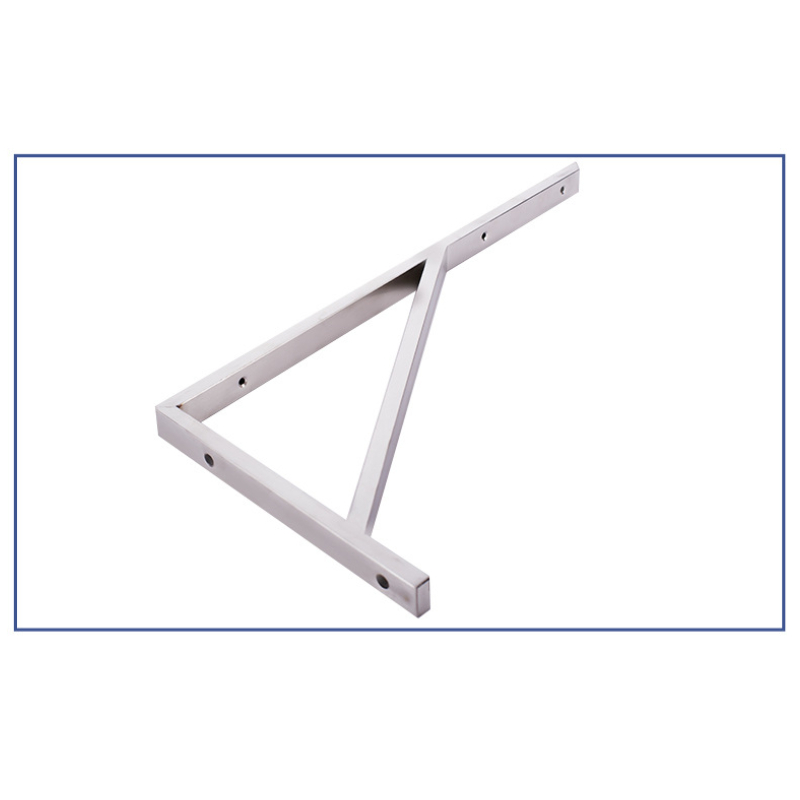
1. Material Composition Grinding wheels can be made from various materials, including aluminum oxide, silicon carbide, and cubic boron nitride (CBN). The choice of material affects the wheel’s cutting efficiency and wear resistance. For harder materials, CBN wheels are often preferred due to their durability.
2. Grit Size The grit size of the grinding wheel influences the surface finish of the workpiece. Finer grits produce smoother finishes but may remove material more slowly, while coarser grits are more aggressive and faster at material removal but may leave a rougher surface.
3. Wheel Type Centerless grinding wheels come in different shapes and designs tailored to specific grinding applications. Ensure that the type of wheel you choose is compatible with your machine and suited for the materials you'll be working with.
4. Hub Compatibility Check the specifications of your centerless grinder to identify the correct hub size and design for the grinding wheels you intend to buy. A mismatched hub can lead to operational issues and reduced grinding efficiency.
5. Supplier Reputation When buying centerless grinder blades, it's essential to choose suppliers with a solid reputation for quality and customer service. Consider reading reviews and seeking recommendations from industry colleagues to find reliable sources.
6. Cost vs. Value While it's tempting to opt for less expensive blades, it's crucial to weigh cost against performance. Investing in high-quality blades can lead to improved productivity and reduced downtime, ultimately saving money in the long run.
Conclusion
Choosing the right centerless grinder blades is vital for achieving efficiency, quality, and performance in precision machining. By understanding the key factors involved in the purchasing process and the impact of blade quality on overall operations, manufacturers can make informed decisions that enhance their production processes. Always remember that the right blade is an investment in the future success of your machining endeavors.