Understanding the Efficiency of Centerless Grinders in Manufacturing
In the fast-paced world of manufacturing, the need for precision, efficiency, and cost-effectiveness is paramount. One essential tool that has significantly contributed to achieving these goals is the centerless grinder. This article explores the benefits and functionalities of centerless grinders, highlighting why they are a must-have in modern manufacturing processes.
What is a Centerless Grinder?
A centerless grinder is a type of grinding machine that offers a fast and efficient way to achieve precise shapes and finishes on metal and other materials. Unlike traditional grinding methods, where the workpiece is held between two centers, a centerless grinder utilizes a setup where the workpiece is supported by an input roller and a regulating wheel. This enables continuous and uninterrupted processing of parts, making it ideal for high-volume production.
The Mechanics Behind Centerless Grinding
The mechanism of a centerless grinder involves several key components the grinding wheel, the regulating wheel, and the work rest blade. The grinding wheel removes material from the workpiece, while the regulating wheel controls the speed and position of the workpiece as it passes through the grinding process. The work rest blade stabilizes the workpiece and ensures accuracy during grinding.
This configuration allows for multiple parts to be processed simultaneously, significantly increasing throughput. Furthermore, the absence of traditional clamping methods leads to reduced setup times, enabling manufacturers to maintain higher productivity levels.
Advantages of Using Centerless Grinders
buy centerless grinder
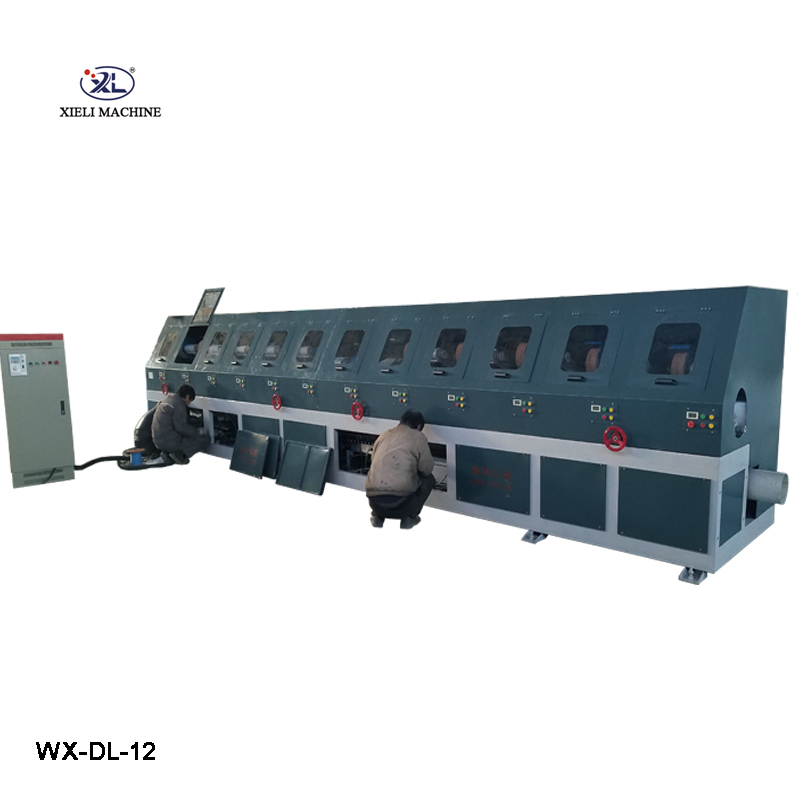
1. High Production Efficiency Centerless grinders are built for high-volume production, capable of processing multiple parts at once. This efficiency translates into lower operational costs and quicker turnaround times, which is essential for meeting market demands and customer expectations.
2. Consistent Precision The design of centerless grinders allows for exceptional precision and uniformity in dimensions. Manufacturers can achieve tight tolerances, which is crucial in applications such as aerospace, automotive, and medical device manufacturing where even the slightest deviation can lead to failures.
3. Versatility Centerless grinders can handle a wide variety of materials, including metals like steel, aluminum, and titanium, as well as plastics and composites. This versatility makes them suitable for various industries and applications.
4. Reduced Handling Since the parts do not need to be clamped, the chances of damage during handling are minimized. Moreover, this reduces the need for secondary operations, further streamlining the manufacturing process.
5. Compact Footprint Centerless grinders are generally smaller than conventional grinding machines, allowing manufacturers to conserve space in their facilities. This compact design does not compromise performance, making it an efficient choice for factories with limited space.
Conclusion
The centerless grinder is an invaluable asset in the manufacturing sector, providing unparalleled efficiency and precision. Its unique design facilitates high-volume production while maintaining excellent dimensional accuracy. By integrating centerless grinding into their operations, manufacturers can achieve significant cost savings, enhance productivity, and improve the overall quality of their products.
Investing in a centerless grinder not only streamlines the manufacturing process but also equips businesses to compete in a challenging market. As industries continue to evolve, the importance of advanced machining technology like centerless grinding cannot be overstated. For manufacturers seeking to enhance efficiency and precision, adopting a centerless grinder may very well be the key to success in today’s competitive landscape.