Understanding the Importance of Coolant in Centerless Grinding
Centerless grinding is a vital machining process utilized in various industries for precision part manufacturing. This technique allows for the grinding of cylindrical parts without the need for a spindle or fixture, enhancing efficiency and accuracy. However, to achieve optimal performance and extend the lifespan of the grinding machine, the use of proper coolant is crucial. In this article, we will explore the essential role of coolant in centerless grinding processes and consider factors that influence the selection of a good coolant.
The Role of Coolant in Centerless Grinding
Coolant serves several important functions during the centerless grinding process
1. Temperature Control One of the primary functions of coolant is to dissipate heat generated during the grinding operation. Excessive heat can lead to thermal deformation of the workpiece, affecting tolerances and surface finish. A quality coolant maintains a consistent temperature, ensuring that the grinding wheel and workpiece remain within acceptable limits.
2. Lubrication Coolants act as lubricants, reducing friction between the grinding wheel and the material being machined. This lubrication not only helps to minimize wear on the grinding wheel but also reduces the force required for grinding, thereby improving efficiency.
3. Chip Removal During the grinding process, chips and debris are produced. Effective coolant systems assist in flushing these chips away from the work area. This not only keeps the grinding area clean but also prevents re-cutting of chips that could damage the workpiece or the grinding wheel.
4. Surface Finish Improvement The right coolant can enhance the surface finish of the ground parts. By allowing better chip removal and reducing thermal effects, coolants can contribute to a smoother, finer finish, vital for many precision applications.
buy centerless grinder coolant
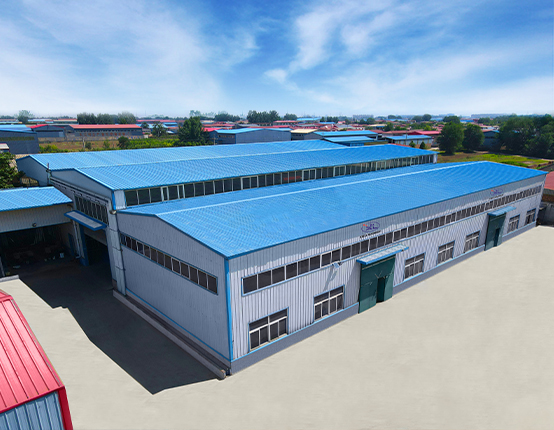
Selecting the Right Coolant
When it comes to choosing the correct coolant for your centerless grinding operation, several factors should be considered
1. Type of Material Different materials require different types of coolants. For instance, ferrous materials may require specific coolant formulations to prevent rust, while non-ferrous materials may benefit from different properties.
2. Grinding Wheel The composition and type of grinding wheel used (e.g., ceramic, diamond, or cubic boron nitride) can influence coolant selection. Some wheels work better with water-based coolants, while others may require oil-based options for optimal performance.
3. Environmental and Health Considerations Today, there is a growing emphasis on using eco-friendly coolants that minimize environmental impact and health risks to workers. Biodegradable and low-toxicity options are increasingly preferred.
4. Cost and Efficiency Finally, the cost of the coolant and its efficiency should also influence your decision. It is often more economical to invest in a high-quality coolant that extends machine life and reduces downtime than to opt for cheaper alternatives that may not perform as well.
Conclusion
In conclusion, the significance of coolant in centerless grinding cannot be overstated. It plays a critical role in heat management, lubrication, chip removal, and improving surface quality. By carefully selecting the right coolant based on the specific needs of the grinding operation and material types, manufacturers can ensure enhanced performance, increased efficiency, and superior product quality. Understanding the dynamics of coolant in centerless grinding is essential for any manufacturing operation looking to achieve higher standards of precision and productivity.