The Evolution of the 24x24 Centerless Grinder Precision Engineering at Its Best
In the bustling world of manufacturing and machining, precision is king. Engineers and manufacturers seek tools that not only meet high standards but also enhance efficiency. One such tool that has been a game-changer in the industry is the 24x24 centerless grinder. Designed for the utmost accuracy and productivity, this type of grinder stands out in the crowded field of machining processes.
Understanding Centerless Grinding
Centerless grinding is a specialized form of grinding that allows for the efficient machining of cylindrical parts without the need for holding them in a chuck. Instead, the workpiece is placed between two wheels a grinding wheel and a regulating wheel. The grinding wheel removes material from the workpiece while the regulating wheel controls the speed and movement of the part. This innovative method not only increases throughput but also improves precision, making it a preferred choice for manufacturers dealing with high-volume production.
Features of the 24x24 Centerless Grinder
The term 24x24 typically refers to the size of the grinder, indicating that it can accommodate parts with a diameter of up to 24 inches and lengths of up to 24 inches. This size makes it versatile enough for various applications, from small components to larger, more complex parts. Here are some key features that set the 24x24 centerless grinder apart
1. High Precision The grinder is engineered to maintain tight tolerances, ensuring that the finished products meet stringent quality standards. This is crucial in industries such as aerospace, automotive, and medical devices, where precision is paramount.
2. Robust Construction Built to withstand heavy use, the machine typically features a rigid frame and high-quality components. This durability ensures longevity and consistent performance over time.
3. Advanced Grinding Technology Many modern 24x24 centerless grinders incorporate CNC (Computer Numerical Control) technology, allowing for automated adjustments and programming for different profiles. This automation reduces the risk of human error and speeds up the production process.
24x24 centerless grinder product
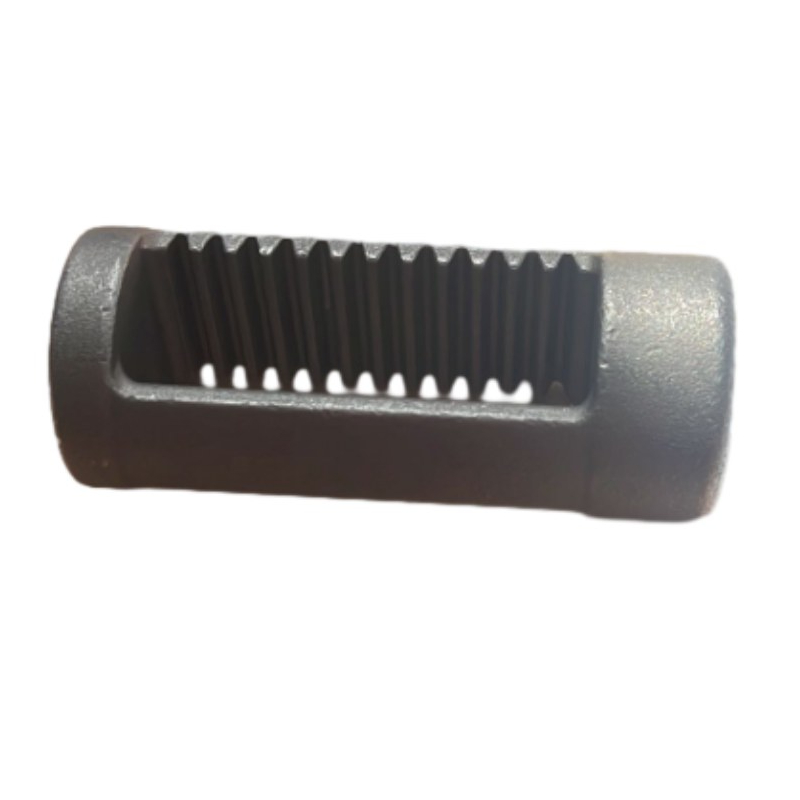
4. Ease of Use User-friendly interfaces allow operators to quickly set up and adjust the machine parameters. This ease of use translates to reduced training time and increased productivity.
Benefits of Using a 24x24 Centerless Grinder
The advantages of incorporating a 24x24 centerless grinder into manufacturing operations are considerable. Firstly, the speed of production is significantly enhanced. Traditional grinding methods can be time-consuming, especially in batch processing. Centerless grinding, on the other hand, allows for continuous processes, eliminating the need for downtime between cycles.
Secondly, the reduction in material wastage is another significant benefit. The precise nature of centerless grinding means that less material is lost during the shaping process, ultimately leading to a more cost-effective solution for manufacturers.
Moreover, the versatility of the 24x24 centerless grinder leads to space-saving benefits. Instead of requiring multiple machines for different operations, manufacturers can streamline their processes and reduce the footprint of their equipment.
Conclusion
In the modern manufacturing landscape, efficiency and precision are critical for success. The 24x24 centerless grinder exemplifies these qualities, serving as a powerful ally for engineers and manufacturers alike. With its advanced technology, robust construction, and versatility, it stands out as an essential tool for a wide range of industries.
As businesses continue to prioritize efficiency, the adoption of centerless grinding technology will likely grow. Investing in a 24x24 centerless grinder not only enhances productivity but also positions manufacturers to meet the ever-evolving demands of the market. With the continuous advancements in technology, the future looks bright for this indispensable machinery—ensuring that precision engineering remains at the forefront of manufacturing.