- Introduction to Paragon Centerless Grinding Machine and Market Overview
- Technical Advantages and Precision Performance
- Comparative Analysis: Leading Manufacturers’ Centerless Grinding Machines
- OEM Paragon Centerless Grinding Machine: Customization and Integration
- Solutions for Various Industries and Use Cases
- Discount Strategies and Sourcing Reliable China Paragon Centerless Grinding Machine Suppliers
- Final Thoughts: Paragon Centerless Grinding Machine for the Future of Precision Machining
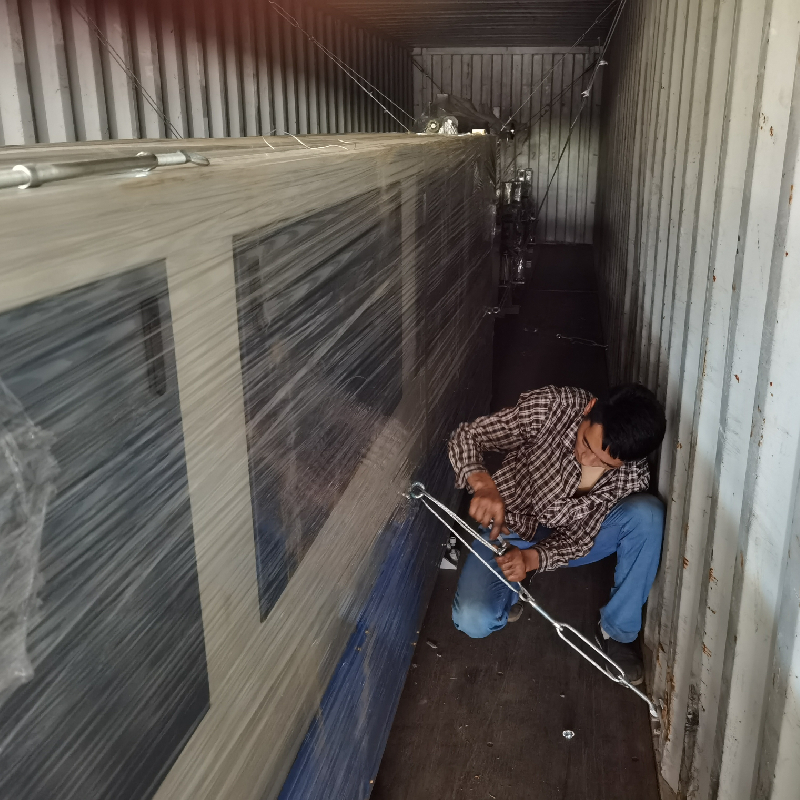
(paragon centerless grinding machine)
Paragon Centerless Grinding Machine: Market Overview and Industrial Demand
The Paragon centerless grinding machine holds a pivotal position in modern industrial manufacturing, thriving on an ever-growing demand for precision and efficiency. Centerless grinding has ascended as a preferred approach in automotive, aerospace, medical device, and heavy equipment production, primarily due to its ability to consistently deliver ultra-fine finishes and tight tolerance parts. According to market analysis, the global grinding machine market, valued at approximately $4.6 billion in 2022, is projected to reach over $6.2 billion by 2028, growing at a CAGR of 5.2%. Nearly 28% of this segment focuses on centerless grinding technology, with Paragon emerging as a leader due to their dedicated emphasis on quality, automation, and versatility. The technology’s appeal lies in its cost-effective production runs, reduced human intervention, and compatibility with a wide range of materials.
Unmatched Technical Advantages and Precision Performance
Users of Paragon centerless grinding machines benefit from a suite of advanced technical features. Core attributes include CNC-controlled wheel dressing, adaptive grinding force systems, and enhanced spindles capable of maintaining rigid concentricity. Integration of automatic loading solutions and high-speed servo motors propels output while minimizing downtime. Paragon’s design enables runout values as low as 0.001 mm, perfectly aligning with international ISO and DIN tolerances. With a typical removal rate of up to 60% faster than traditional OD grinding, and surface roughness levels (Ra) consistently below 0.1 μm, productivity accelerates without compromising quality. These advancements directly translate to reduced labor overhead, lower per-unit costs, and robust repeatability, serving both high-volume and low-volume production needs.
Manufacturer Comparison Table: Paragon vs. Major Brands
Distinguishing the China Paragon centerless grinding machine from its competitors highlights clear strengths in performance, flexibility, and long-term reliability. Below is a comparative analysis of four leading manufacturers based on key specifications:
Feature | Paragon | Brand A (European) | Brand B (Japanese) | Brand C (USA) |
---|---|---|---|---|
Max Grinding Diameter (mm) | 200 | 160 | 150 | 180 |
Typical Tolerances (mm) | ±0.001 | ±0.002 | ±0.0015 | ±0.002 |
Surface Finish (Ra, μm) | ≤0.08 | 0.15 | 0.12 | 0.10 |
Automation Support | Full CNC, Robot Loading | Partial CNC | CNC with limited Auto | Semi-automatic |
Annual Maintenance Cost (USD, est.) | 2,500 | 5,500 | 4,800 | 6,200 |
Global Installations | 8,000+ | 3,700 | 4,500 | 2,900 |
Warranty (Years) | 2 | 1 | 1.5 | 1 |
The above data not only demonstrate Paragon's technical leadership but also underscore its cost efficiency, sustainability, and ability to support Industry 4.0-ready smart factories.
OEM Paragon Centerless Grinding Machine: Customization and Integration
Selecting an OEM Paragon centerless grinding machine provides immense flexibility to meet specific production requirements. OEM solutions are particularly advantageous for manufacturers seeking tailored features, such as custom wheel sizes, bespoke automation interfaces, and integration of real-time monitoring systems linked with MES or ERP software. Paragon’s engineering team liaises closely with clients to develop grinding systems that fit legacy production lines or high-throughput robotic cells. This collaborative approach results in unique solutions—from coolant system upgrades for exotic materials to modular CNC controls that adapt to fluctuating market needs. Customization options also extend to safety standards compliance and energy-saving enhancements, further elevating operational value.
Applications and Industry Use Cases
Paragon centerless grinding machines have built a reputation as the backbone of precision manufacturing across multi-sectoral applications. Their technology is deployed in producing fuel injection parts, transmission shafts, surgical instruments, and bearing rollers. For instance, in the automotive sector, Paragon systems support the production of camshafts with tolerances of ±0.0008 mm, facilitating higher fuel efficiency and reduced emissions in vehicles. Aerospace contractors report cycle time reductions of up to 40% compared to standard grinding methods when machining critical landing gear pins. Medical device OEMs leverage the surface integrity and biocompatibility achieved by Paragon machines to ensure regulatory compliance and functional longevity. The adaptability of these grinders makes them central to both prototyping and mass production, reducing lead times, minimizing waste, and consistently achieving stringent international standards.
Discount Paragon Centerless Grinding Machine Sourcing from China: Key Considerations
Businesses seeking a discount Paragon centerless grinding machine need to balance cost optimization with supplier credibility. Sourcing directly from top-rated Chinese manufacturers allows for lower acquisition costs—often 18-30% less than Western competitors—without sacrificing essential technology or warranty coverage. Programs run by Chinese suppliers often include scalable discounting for bulk orders, integrated training, and long-term service contracts. Potential buyers should evaluate certifications (such as CE, ISO9001, and national safety standards), factory production capacity, and the manufacturer’s track record for export logistics. Transparent post-sales support, technical documentation availability, and responsive local service offices enhance the procurement experience. By leveraging these factors, businesses can secure performance machines at very competitive prices, maximizing capital efficiency across their machining operations.
Paragon Centerless Grinding Machine: Driving the Future of Precision and Productivity
The Paragon centerless grinding machine symbolizes a commitment to accuracy, productivity, and continuous innovation in manufacturing. With technical leadership, robust after-sales service, and extensive customization options, Paragon stands at the forefront of the global centerless grinding market. Companies that invest in Paragon technology report improvements in process flow, reduction of cycle times, and enhanced quality metrics that future-proof their production lines. As manufacturing standards evolve, Paragon’s alignment with digitalization and automation trends ensures it remains the trusted choice for precision engineering enterprises worldwide. By adopting a Paragon system, manufacturers secure not just a machine, but a long-term partner in achieving operational excellence.
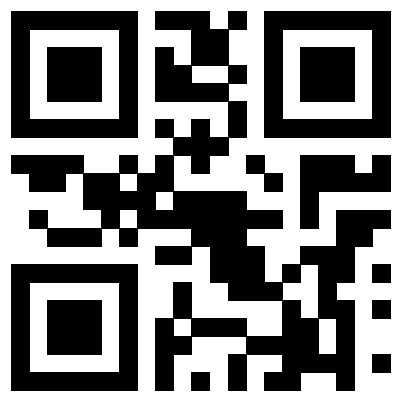
(paragon centerless grinding machine)