Centerless surface grinders have long been a cornerstone in the realm of precision machining, providing unmatched accuracy and efficiency for applications ranging from aerospace to medical device manufacturing. This article delves into the unique features, advantages, and real-world applications of centerless surface grinder products, reinforcing their standing as indispensable tools in modern manufacturing.
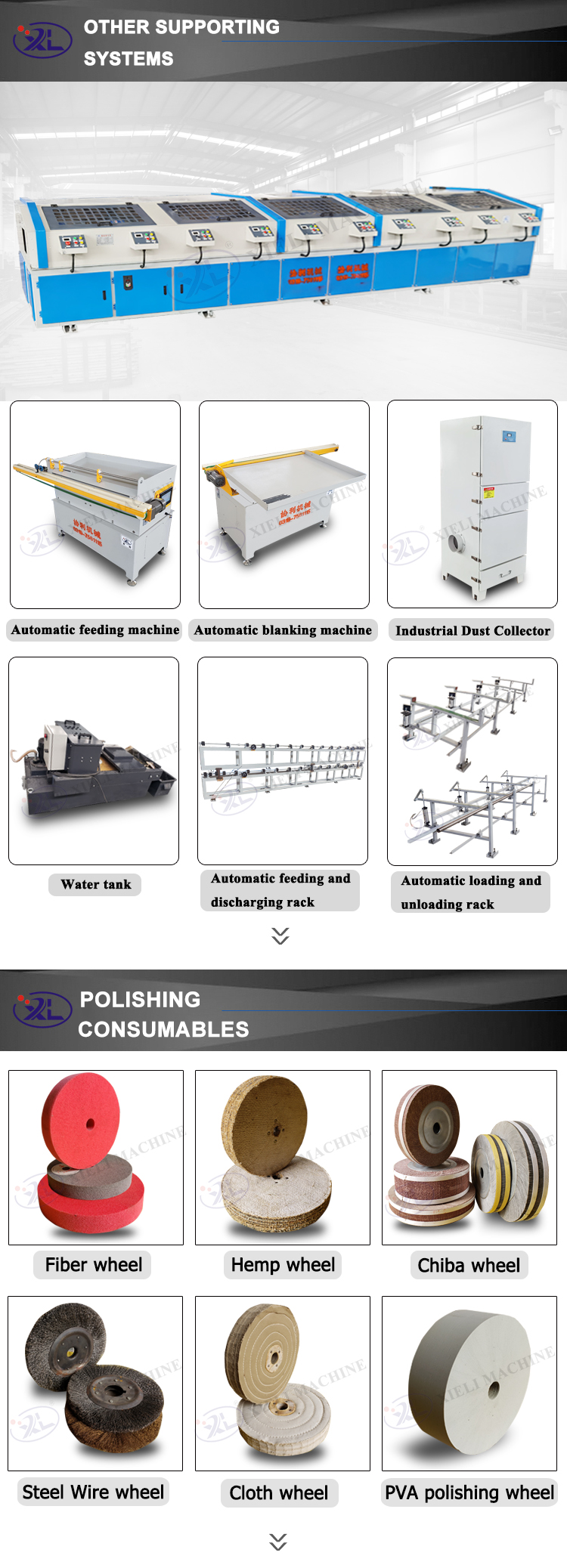
The heart of a centerless surface grinder lies in its innovative design, which eliminates the need for a spindle or fixture to hold the workpiece. This breakthrough enables the machine to support the workpiece between a grinding wheel and a regulating wheel, allowing for high throughput and minimal downtime. This makes centerless grinding exceptionally efficient for mass production environments, delivering consistency and precision at scale.
A key strength of centerless surface grinders is their ability to handle workpieces of varying sizes and shapes. This versatility is particularly advantageous in industries such as automotive manufacturing, where components like camshafts, bearings, and pistons require exacting tolerances and finishes. By dynamically adjusting the speed and positioning of the regulating wheel, manufacturers can effortlessly shift between different product requirements, optimizing the production process and reducing lead times.
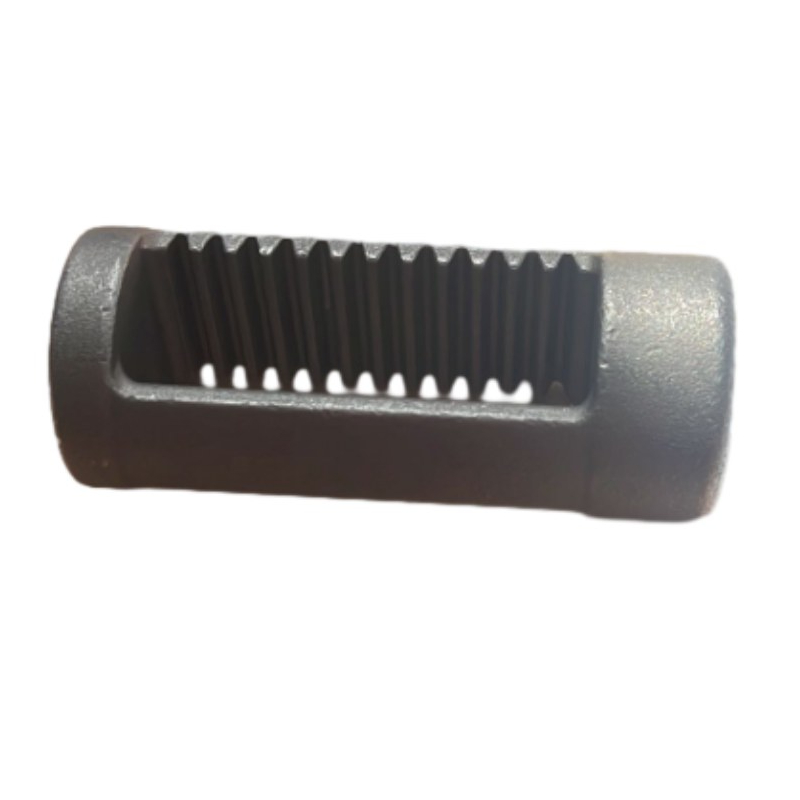
Moreover, centerless surface grinders excel in delivering exceptional surface finishes, a critical consideration for applications demanding low roughness averages. This capability is crucial in the production of medical equipment and precision instruments, where material smoothness directly impacts performance and functionality. The grinders' capacity to achieve superfine finishes ensures compliance with the rigorous standards observed in these industries, safeguarding product reliability and patient safety.
The integration of advanced automation and control systems has further enhanced the appeal of centerless surface grinders. Modern machines boast CNC interfaces and real-time monitoring tools, empowering operators to execute complex grinding tasks with unprecedented precision. Additionally, automation minimizes human intervention, reducing the risk of error and promoting efficiency across prolonged manufacturing runs. As a result, manufacturers can maintain superior quality control, bolstering trust and reliability among their clients.
centerless surface grinder products
Another critical advantage of centerless surface grinders is their eco-friendliness and sustainability. With growing emphasis on reducing industrial waste and energy consumption, these machines present an opportunity to minimize both. Their streamlined processes result in lower material waste, and innovations in grinding wheel technology have improved energy efficiency, aligning with global environmental objectives.
Real-world testimonials from industry experts illuminate the profound impact that centerless surface grinders have on productivity and cost-effectiveness. For instance, a leading aerospace component manufacturer reported a 40% increase in throughput following the implementation of a centerless grinding solution. This improvement significantly cut operational costs and enhanced competitiveness in a fiercely challenging market.
Ensuring trustworthiness and reliability, manufacturers of centerless surface grinders adhere to stringent quality assurance protocols, sourcing premium materials and employing expert craftsmanship. Comprehensive testing regimens and adherence to international standards such as ISO and ANSI further affirm these machines' credibility, providing customers with peace of mind and long-lasting performance.
In conclusion, centerless surface grinder products represent the pinnacle of precision machining technology, offering unparalleled flexibility, efficiency, and quality. Through continuous innovation, these machines stand poised to meet the evolving needs of diverse industries, driving advancements that pave the way to future achievements. By understanding their unique capacities, professionals in the manufacturing sector can harness these tools' full potential, securing a competitive advantage and reinforcing their authority in their respective fields.
For More Details Pls Contact Us
Fiberglass Reinforced Plastic (FRP), also known as fiber-reinforced plastic, is a composite material widely used across various industries.