Custom Automatic Centerless Grinding Machine Revolutionizing Precision Engineering
In the realm of precision engineering, where efficiency and accuracy are paramount, custom automatic centerless grinding machines have emerged as a game-changer. These machines are specifically designed to meet the unique needs of various industries, enhancing productivity while ensuring the highest standards of precision. This article delves into the features, benefits, and applications of custom automatic centerless grinding machines, illustrating their vital role in modern manufacturing.
What is Centerless Grinding?
Centerless grinding is a machining process that removes material from the outer diameter of a workpiece. Unlike conventional grinding methods, where the workpiece is held between two centers, centerless grinding relies on a support blade and the grinding wheel to keep the workpiece in place. This method offers several advantages, including higher throughput rates, improved consistency, and reduced setup times, making it ideal for mass production.
Key Features of Custom Automatic Machines
One of the primary advantages of custom automatic centerless grinding machines lies in their adaptability. Manufacturers can tailor these machines to their specific production requirements, incorporating advanced features such as
1. Automation Automatic feed systems allow for continuous operation without the need for manual intervention, significantly increasing production speed and decreasing labor costs.
2. Precision Controls Advanced CNC (Computer Numerical Control) technology enables precise control over grinding parameters, ensuring optimal surface finish and dimensional accuracy.
3. Versatile Design Custom machines can be designed to accommodate various workpieces, from small components to larger parts, allowing for flexibility in production lines.
custom automatic centerless grinding machine
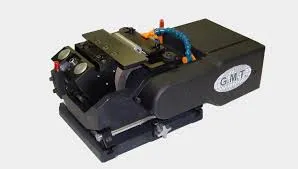
5. Safety Features Enhanced safety protocols, such as emergency shutdown systems and protective enclosures, ensure a safe working environment for operators.
Benefits of Custom Centerless Grinding Machines
The shift to custom automatic centerless grinding machines offers numerous benefits. Firstly, they can significantly reduce manufacturing costs. By automating the grinding process, manufacturers minimize labor expenses and improve overall throughput. This efficiency translates into a shorter time-to-market for products, providing a competitive edge in today’s fast-paced industrial landscape.
Secondly, the precision afforded by these machines leads to higher quality products. Tighter tolerances mean fewer defects and a better finish, which is crucial in industries such as aerospace, automotive, and medical device manufacturing, where quality is non-negotiable.
Additionally, the adaptability of custom machines allows manufacturers to respond swiftly to changing customer demands. By reconfiguring existing machines, they can accommodate new designs or production volumes, which is invaluable in industries that experience fluctuating market conditions.
Applications Across Industries
Custom automatic centerless grinding machines are utilized across a multitude of sectors. In the automotive industry, they are essential for manufacturing parts such as shaft components, bushings, and bearings, all of which require precise tolerances.
In the aerospace sector, these machines play a critical role in producing engine components and structural parts, where even the slightest deviation can have catastrophic consequences. The medical device industry also benefits from centerless grinding technology, particularly in the production of surgical instruments and implants that demand high precision.
Conclusion
In conclusion, custom automatic centerless grinding machines represent a significant advancement in manufacturing technology. Their ability to deliver precision, efficiency, and adaptability makes them an invaluable asset for modern production processes. As industries continue to evolve and demand higher quality at lower costs, the importance of these machines will only grow, establishing them as essential tools in the quest for excellence in precision engineering. Embracing this technology not only enhances production capabilities but also paves the way for innovation in manufacturing practices, ultimately benefiting both manufacturers and consumers alike.