The Essential Role of Custom CNC Centerless Grinders in Modern Manufacturing
In the contemporary manufacturing landscape, precision and efficiency are paramount. One of the most innovative solutions that has emerged to meet these demands is the custom CNC centerless grinder. Unlike traditional grinding methods, centerless grinding offers several advantages, making it a favored choice in various industries.
Understanding Centerless Grinding
Centerless grinding is a machining process that involves the removal of material from a workpiece without the need for a spindle. In this method, the workpiece is placed between two grinding wheels, with one wheel fixed and the other in motion. This unique setup allows for continuous production of parts with a minimal risk of damage to the workpiece. The absence of a central support allows for a variety of shapes and sizes to be processed efficiently.
Customization in CNC machining
The term custom CNC centerless grinder signifies the ability to tailor grinding machines to meet specific production requirements. CNC, or Computer Numerical Control, technology enables manufacturers to program precise movements and operations into the grinder. This capability is particularly beneficial for industries that require high precision and repeatability across large production runs.
Custom CNC centerless grinders can be designed to accommodate different materials, tolerances, and surface finishes. For example, manufacturers can configure the machines to grind metals, plastics, or composites, depending on the project needs. Furthermore, specific designs can be implemented to achieve various types of finishes, such as mirror-like surfaces or textured finishes, thereby broadening the scope of applications.
Advantages of Custom CNC Centerless Grinders
custom cnc centerless grinder
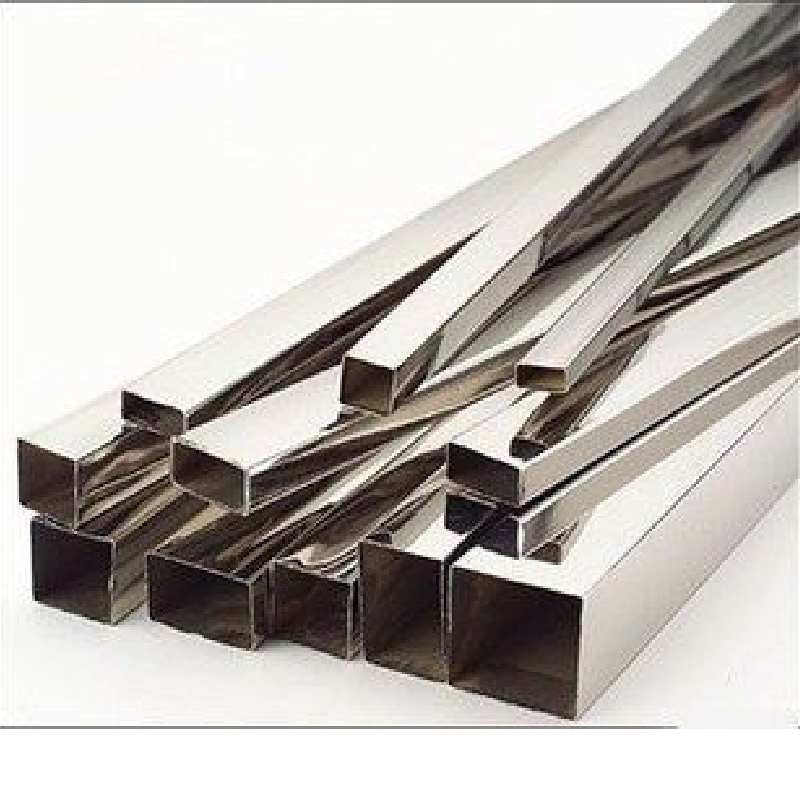
1. Increased Precision The integration of CNC technology allows for higher levels of precision than manual grinding methods. Custom programming ensures that every component meets exact specifications, significantly reducing the risk of tolerances being exceeded.
2. Enhanced Efficiency The ability to run multiple parts simultaneously without downtime increases productivity. Custom CNC centerless grinders can be programmed to execute complex operations in a single pass, cutting down on cycle times and freeing up production resources.
3. Versatility A custom grinder can be adjusted to handle an array of part sizes and shapes, making it suitable for diverse manufacturing needs. This adaptability is particularly advantageous for businesses that handle varying production runs.
4. Reduced Labor Costs With the automation that CNC technology provides, businesses can operate with fewer personnel, streamlining labor costs and improving overall workplace safety.
5. Quality Control Automated systems offer enhanced monitoring and quality checks during the grinding process, ensuring consistency and reducing waste.
Conclusion
As manufacturing continues to evolve, the demand for precision and speed escalates. Custom CNC centerless grinders stand out as a crucial asset in meeting these challenges. By offering tailored solutions that enhance efficiency, precision, and versatility, these machines play an integral role in ensuring that manufacturers can produce high-quality products at competitive rates. For companies looking to improve their grinding processes, investing in custom CNC centerless grinders may very well be a transformative decision, driving their success in an increasingly competitive market.