Centerless grinding is indispensable in modern manufacturing, delivering precision and cost-effectiveness across industries.
A critical aspect of centerless grinding is the coolant used in the process. The right coolant can significantly enhance grinding performance, tool lifespan, and part quality. This extensive discussion delves deep into what makes an excellent centerless grinder coolant and how leveraging the right one serves as a pivotal move for optimal outcomes.
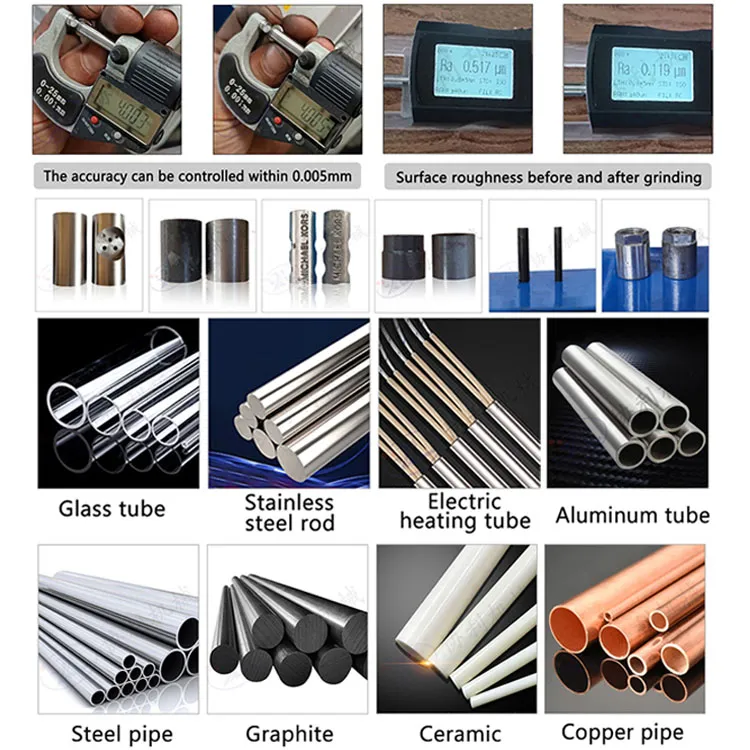
A well-formulated centerless grinder coolant performs multiple roles cooling, lubrication, chip removal, and corrosion resistance. Its primary function is cooling, as grinding generates considerable heat that can deform metals if not dissipated efficiently. Imagine running a marathon under the scorching sun without water—that's your grinding operation lacking an effective coolant.
Expert manufacturers prioritize coolants that are water-soluble or oil-based, balancing thermal conductivity and lubrication. Water-soluble coolants often have additives to prevent rust, bacterial growth, and extend fluid life. They are versatile and frequently used due to their effectiveness in cooling and compatibility with various materials and finishes. On the other hand, oil-based coolants provide superior lubrication and are more suitable for operations involving extreme pressure or when working with harder materials.

One standout choice is synthetic coolants, known for their stability and performance consistency. Their non-reactive nature makes them suitable for a wide range of metals and minimizes the risk of adverse chemical interactions. Additionally, their low misting properties contribute to a healthier workplace environment, aligning with the increasing emphasis on occupational safety and sustainability.
However, the journey to finding the ideal coolant for centerless grinding does not stop at choosing the type. Measurement and maintenance play pivotal roles. Regular monitoring of coolant concentration, pH, and contamination levels is crucial. Leading-edge companies implement automated tracking systems to ensure these parameters remain within optimal ranges, thereby maximizing efficiency and minimizing the risk of machine wear or workpiece defects.
The best practices observed in the industry include consistent filtration and recycling processes to extend coolant life. Advanced filtration systems are adopted widely, capable of removing metal fines and contaminants. Recycling systems help in reducing waste and operational costs, promoting sustainability.
centerless grinder coolant
From an authoritative standpoint, many industry leaders align their coolant choices with environmental and regulatory standards. Compliance with frameworks such as ISO 14001 demonstrates a commitment not only to quality but to responsible manufacturing practices. Coolants designed to align with these standards are gaining traction as they reinforce a company’s market reputation while adhering to legal obligations.
Trustworthy suppliers focus on customization, offering coolants tailored to specific industrial needs. Collaborating with suppliers that provide regular technical support ensures that users are well-informed about product usage and maintenance, thereby reducing potential downtimes and inefficiencies.
Advanced centerless grinding operations also integrate coolant management systems that digitally regulate flow and temperature, ensuring consistent coolant delivery and monitored usage. These systems reduce human error and ensure precision grinding, ultimately leading to zero defect manufacturing—a benchmark of modern production lines.
Emphasizing a product-centric approach doesn't merely push the product but showcases how adopting the right coolant aligns with broader manufacturing goals. Centerless grinder coolants are not ancillary but integral components of a symbiotic system where every detail matters. They contribute not just to the performance but to the entire value chain, from operator safety to the final product quality.
In sum, the selection and management of centerless grinder coolants are deeply embedded within quality control frameworks, optimizing the delicate balance between technical demands and economical considerations. With grinding operations poised towards automation and precision, coolants will continue to play a central role in powering industry innovation and operational excellence.