Centerless Grinding on Surface Grinders A Revolutionary Product in Manufacturing
In the realm of precision manufacturing, centerless grinding on surface grinders has emerged as a revolutionary product that is transforming the way components are finished. This advanced technique offers numerous advantages over traditional grinding methods, making it an indispensable tool for industries ranging from automotive to aerospace.
Centerless grinding, as the name suggests, involves grinding without a central support or chuck. Instead, workpieces are supported between two rotating wheels—one acting as the grinding wheel and the other as the regulating wheel. This unique setup allows for continuous through-feed grinding, where the material is fed into the machine and ground as it moves along the axis, significantly reducing setup time and increasing productivity.
One of the key benefits of centerless grinding on surface grinders is its ability to produce high-precision parts with minimal geometric tolerances. The absence of a chuck eliminates the possibility of chuck marks or distortions that can occur when gripping force is applied. Moreover, the consistent pressure applied by the regulating wheel ensures that each part is ground to the same specifications, resulting in a higher level of consistency across the entire production run.
Another advantage of this technology is its versatility. Centerless grinding on surface grinders can handle a wide variety of materials, including metals, ceramics, and composites. It is also capable of grinding complex shapes and profiles that would be difficult or impossible to achieve with conventional grinding methods. This makes it an ideal solution for industries that require custom-shaped components with tight tolerances This makes it an ideal solution for industries that require custom-shaped components with tight tolerances
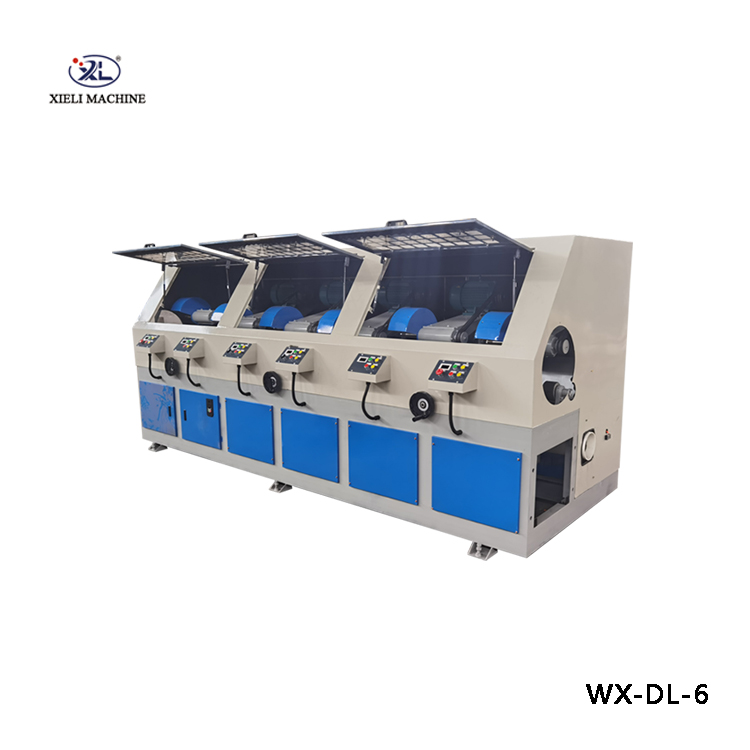
This makes it an ideal solution for industries that require custom-shaped components with tight tolerances This makes it an ideal solution for industries that require custom-shaped components with tight tolerances
centerless grinding on surface grinder product.
In addition to its technical benefits, centerless grinding on surface grinders also offers economic advantages. By reducing the need for multiple setups and minimizing waste, manufacturers can achieve significant cost savings. Furthermore, the increased efficiency and reduced downtime associated with this process can help businesses stay competitive in today's fast-paced market.
Despite these numerous benefits, implementing centerless grinding on surface grinders does require specialized knowledge and training. Operators must have a deep understanding of the process parameters and how they impact the quality of the finished product. Additionally, proper maintenance and regular inspections are essential to ensure optimal performance and prevent potential issues before they arise.
In conclusion, centerless grinding on surface grinders represents a paradigm shift in the world of precision manufacturing. Its ability to deliver high-quality parts with exceptional consistency and efficiency has made it an invaluable tool for industries worldwide. As technology continues to advance, it is likely that we will see even more innovations in this field, further enhancing the capabilities of this already impressive product.