The Evolution of Centerless Tube Grinding Machines
In the realm of precision manufacturing, the importance of achieving a smooth and consistent finish on metal components cannot be understated. Among various machining processes, centerless grinding stands out as a highly efficient method for processing cylindrical parts, particularly tubes. The evolution of centerless tube grinding machines has transformed manufacturing practices, enabling industries to produce high-quality components with remarkable speed and precision.
Understanding Centerless Grinding
Centerless grinding differs from traditional cylindrical grinding methods by eliminating the need for external centers to support the workpiece. Instead, the tube or cylindrical part is held in place by a combination of a grinding wheel and a regulating wheel. This configuration allows for continuous grinding processes, making it highly effective for mass production.
The fundamental principle of centerless grinding involves three key components the grinding wheel, the regulating wheel, and the workpiece. The grinding wheel performs the cutting operation, while the regulating wheel governs the rotational speed and position of the tube. By adjusting the relative positions and angles of these wheels, operators can achieve precise dimensions and surface finishes that meet stringent quality standards.
Advantages of Centerless Tube Grinding Machines
One of the most significant advantages of centerless tube grinding machines is their ability to grind multiple parts simultaneously
. This capability dramatically increases productivity, especially in high-volume manufacturing scenarios. The machines can process long lengths of tubing without the need for additional setups, saving time and reducing production costs.odm centerless tube grinding machine
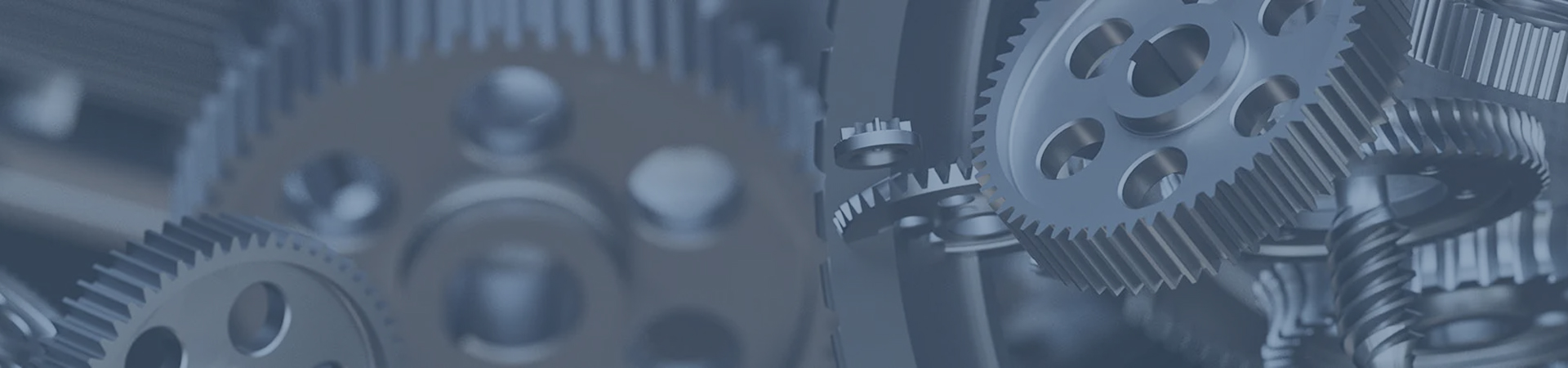
Moreover, centerless grinding is exceptionally efficient in removing material. As the workpiece moves through the grinding zone, it experiences a consistent and uniform surface finish with minimal heat generation. This attribute not only enhances the quality of the finished product but also prolongs the lifespan of the grinding wheels.
Centerless tube grinding machines are also highly automated, allowing for seamless integration into modern manufacturing workflows. Advanced controls and automation systems enable precise monitoring and adjustment of grinding parameters, leading to better consistency and reduced human error. This level of automation is particularly beneficial in industries where tight tolerances and repeatability are crucial, such as aerospace, automotive, and medical manufacturing.
Technological Advances in Centerless Grinding
Over the years, technological advancements have significantly improved the performance and capabilities of centerless tube grinding machines. Innovations such as CNC (Computer Numerical Control) technology allow for greater precision in the grinding process, enabling manufacturers to produce complex geometries that were previously challenging to achieve.
Additionally, the introduction of advanced grinding wheels made from superabrasive materials, such as diamond and CBN (Cubic Boron Nitride), has enhanced the material removal rates and surface finishes attainable through centerless grinding. These materials enable faster grinding speeds while reducing wear, leading to lower maintenance costs and higher productivity.
Conclusion
In conclusion, centerless tube grinding machines have become a cornerstone of modern manufacturing processes due to their ability to deliver high quality, efficiency, and automation. As industries continue to demand precise components at an increasingly rapid pace, the importance of these machines cannot be overstated. With ongoing advancements in technology and materials, the future of centerless grinding looks promising, ensuring that it will remain a vital process in the manufacturing landscape for years to come. As manufacturers adopt these innovations, they stand to benefit from enhanced productivity, reduced costs, and improved quality in their operations.